鉄鋼業界のカーボンニュートラル
鉄鋼業界は国内産業界で最も多くのCO2を排出しており、遅ればせながら脱炭素化に向け「グリーンスチール」の商品化を加速している。
中でも、神戸製鋼は低CO2高炉鋼材”Kobenable Steel”を他社に先駆けて商品化し、低炭素Al合金板材も含めて日産自動車に供給を開始した。2023年春を目指して新型EVの「セレナe-POWER」、「アリア」や、中型SUVの新型「エクストレイル」などへの適用が進められている。
欧州
戦略:
■電炉+直接還元製鉄/水素直接還元製鉄 ➡ 主流、天然ガスから水素への転換を計画
■高炉(転炉)+CCUS(CO2の回収・再利用・貯留)➡ 2020年以降の新規計画はない
■電炉(スクラップ利用)➡ 実用炉の建設Pjが発表
再生可能エネルギー導入が進み、自動車メーカーからの要請を受け、鉄鋼業界はグリーンスチール生産に動き出した。ドイツSalzgitterはウィンドファームを建設、Tata Steel Europeは電炉+水素直接還元製鉄を選択して高炉+CCUSは保留、ドイツThyssenkruppは直接還元製鉄への大型投資を発表。
米国の戦略
戦略:
■電炉(スクラップ利用)➡ 高級鋼の製造
■溶融酸化物電気分解法(MOE:Molten oxide electrolysis)➡ スタートアップBoston Metal
USスチールは300万トン/年の電炉・鋼板工場を新設予定。最大90%のスクラップ鉄を利用した高張力鋼の生産でCO2排出量の75%削減を実現した。また、MOEによる製鉄では、酸化鉄を直接電気分解することで鉄鉱石中の酸素を除去し、鉄鉱石から直接粗鋼を取り出すことで注目を集めている。
アジアの戦略
戦略:
■韓国:流動層還元法をベースとした水素還元製鉄
■中国:酸素高炉、ミニ高炉(水素還元)、電炉拡大などを検討中
韓国POSCOは2007年に開発した流動層還元法をベースに、2030年に向け水素還元技術HyREXを開発中である。中国大手鉄鋼メーカーは熱風に代り純酸素を吹き込むことで石炭使用量を減らす酸素高炉を検討中、またミニ高炉による水素還元製鉄の研究を進めている。
出典:星野岳穂:カーボンニュートラル実現に向けた鉄鋼業の取り組みと課題、2023年3月29日
日本の鉄鋼メーカーの動向
日本の産業部門におけるCO2の総排出量は2.8億トン(2019年)にのぼり、その内訳は鉄鋼1.3億トン(48%)、化学0.6億トン(20%)、窯業他0.2億トン(9%)、紙パルプ0.2億トン(6%)、機械0.1億トン(4%)、その他0.4億トン(14%)である。鉄鋼業界は最も多くのCO2を排出している。
日本はカーボンニュートラルに向けた戦略として、欧州で保留となったプロセス「高炉(転炉)+CCUS」を追求し、2013年にNEDO事業「環境調和型製鉄プロセス技術開発」で開始し、2016年にパイロットプラントが完成した。世界のトレンドが水素直接還元製鉄に向いており、見直す必要はないか?
政府の支援
2025年1月、経済産業省は自動車メーカーに「グリーン鉄」導入を促すため、グリーン鉄を採用したEVなどエコカー購入者に対する補助金を最大5万円上乗せする制度を始めると発表。2025年度の新車購入者から対象とし、各メーカーに2030年度までのグリーン鉄の調達量や導入比率などの計画提出を求める。
今後、メーカー毎の上乗せ額を設定し、同じメーカーのEVであれば一律で最大5万円となるが、軽EV、PHV、FCVなどの種別により異なる。「クリーンエネルギー自動車導入促進補助金」は、車種や性能・機能などで異なり、基本額は最大でEVが85万円、軽EV・PHVが55万円、FCVが255万円で、この額に上乗せされる。
*グリーン鉄は強度や軽さなど性能は遜色ないが、製造コストが高い。日本自動車工業会によると、車1台に必要な鋼材は1.5トンで、CO2を3割削減するには3万円/台のコスト増になる。現状、自動車メーカーへの導入はほとんど進んでいないのが実情である。
神戸製鋼所
2022年5月、従来の高炉工程で発生するCO2排出量を大幅に削減した低CO2高炉鋼材“Kobenable Steel(コベナブルスチール)”を国内で初めて商品化した。使用する鉄鉱石の一部を還元済みの熱間成形還元鉄(HBI)に置き換え、同社加古川製鉄所の高炉に多量装入して製造する。
従来の高炉法に比べて製鉄工程でのCO2排出量を20~40%抑制でき、2種類の低CO2高炉鋼材の販売を開始している。「マスバランス方式」適用により、英国の第三者機関から「CO2排出量100%削減」の認定を受けている。
2023年は8000トン/年を供給し、日産自動車の「セレナ」や、東京豊洲で建設中の高層ビルの鉄骨で採用されている。
低CO2高炉鋼材“Kobenable Steel”の製造:
■天然ガス(主にCH4)を還元材とし、粉鉱石を加工したペレットを使ってシャフト炉で還元鉄を製造し、ミドレックス技術により高温の還元鉄を運搬に適する大きさの熱間成形還元鉄(HBI:Hot Briquetted Iron)にして高炉へ移送する。
■鉄鉱石の一部を既に還元済みのHBIに置き換え、従来、高炉で使用するコークス量を減らし、CO2排出量を削減する。販売にあたっては、全体でのCO2削減効果を特定の鋼材に割り当てる「マスバランス方式」を採用する。
また、低炭素アルミニウム(Al)合金板材は、原料鉱石(ボーキサイト)からAl地金を造る「電解精錬工程」に太陽光発電の電力のみを使用する。これにより、Al地金製造時のCO2排出量を従来比で約50%削減する。また、製造現場で発生したリサイクル原料も活用し、CO2 排出量を削減する。
低炭素アルミニウム合金板材の製造:
■太陽光発電によるAl地金の生産は、アラブ首長国連邦(UAE)のEmirates Global Aluminium(EGA)が担当し、同社が生産した地金を伊藤忠商事が神戸製鋼に供給する。伊藤忠から調達したAl地金を用いて、神戸製鋼の真岡製造所でAl合金板材を生産する。
JFEスチール
2022年10月、CO2排出量を減らし実質ゼロにする「グリーン鋼材「JGreeX(ジェイグリークス)」を、2023年上期から販売すると公表した。第三者機関(日本海事協会)からの認証を得たうえで、販売にあたっては全体でのCO2削減効果を特定の鋼材に割り当てる「マスバランス方式」を採用する。
2023年度の供給可能量は20万トン程度で、東日本製鉄所(千葉地区)第4製鋼工場へ新たなアーク式電気炉の導入を発表している。また、2030年度時点で500万トン/年のグリーン鋼材を販売する計画で、2027~2030年度にも岡山県の高炉1基を電炉に転換する検討を進めている。
2023年6月、20万トン/年程度の供給を9月に開始する。広島県の造船会社が自社用船に採用し、12月からは国内海運8社が発注する貨物船向けにも供給する。
2024年7月、グリーン鋼材を、苫小牧栗林運輸が新設する倉庫向けに供給する。8月に着工し2025年7月の完成を見込む苫小牧市内の倉庫に使う500トンの鋼材のうち、250トンでグリーン鋼材を採用する。倉庫の総工費は7億円を見込むが、グリーン鋼材の採用による総工費の増加分は1〜2%である。
道内では今後、GX関連の投資が相次ぎ、洋上風力発電の基礎部分や、データセンターなどの建築でもグリーン鋼材の採用余地は大きい。
日本製鉄
2022年5月、CO2排出量が実質ゼロの「NSCarbolex Neutral(エヌエスカーボレックス ニュートラル)」を2023年度から販売すると公表した。
2022年度下期以降に商業運転を開始する瀬戸内製鉄所広畑地区他に新設した電炉で、グリーン電力を使って生産する。2023年9月から販売を開始し、初年度の供給量は30万トン規模で、生産量は70トン/年で、主に電磁鋼板と自動車用鋼板を製造する。
最高級の電磁鋼板を電炉で造るのは世界で初めての試みとなるが、低コスト化には原発の再稼働が必要としている。また、高炉で生産する鉄鋼は水素還元製鉄により炭素の使用量を減らせても、ゼロにはできないため、CCUS(CO2の回収・再利用・貯留)導入が必須としている。
2023年7月、液化水素向けの新鋼材の開発を発表した。水素ステーション向け需要を取り込み、2023年度から本格販売を目指す。一定以上のクロムを添加したステンレス鋼の一種で、低温の液化水素が触れても割れないよう、金属中の特定化合物を減らすなど成分調整を加えた。
現状、液化水素を受け入れるタイプの水素ステーションを導入する事業者は限られる。ただ、通常の気体と比べて体積を1/800に抑えられ運搬効率が高まるため、将来的には普及が期待されている。
2024年12月、高炉水素還元で、CO2を43%削減する技術を東日本製鉄君津地区の試験炉で確立した。加熱水素の使用や高炉内の熱バランス調整で向上させ、今後は50%以上の削減と実機高炉での活用をめざす。2026年4月に君津地区の第2高炉で実証試験を始める予定で、水素吹き込みの工事を今後進める。
東京製鉄
大成建設に建設用鋼材の供給を予定している。
自動車メーカーの動向
日産自動車
2022年12月、国内で生産する新型車に、神戸製鋼所が開発した低炭素鋼材と低炭素アルミニウム(Al)合金板材を採用すると公表した。自動車部品を製造する工程でのCO2排出量削減が狙いである。
低炭素鋼材は、2023年春に発売予定の中型ミニバンの新型「セレナe-POWER」から採用し、順次採用車種を増やす。適用部位は、鋼材をプレス成形して造るボディー骨格部品である。
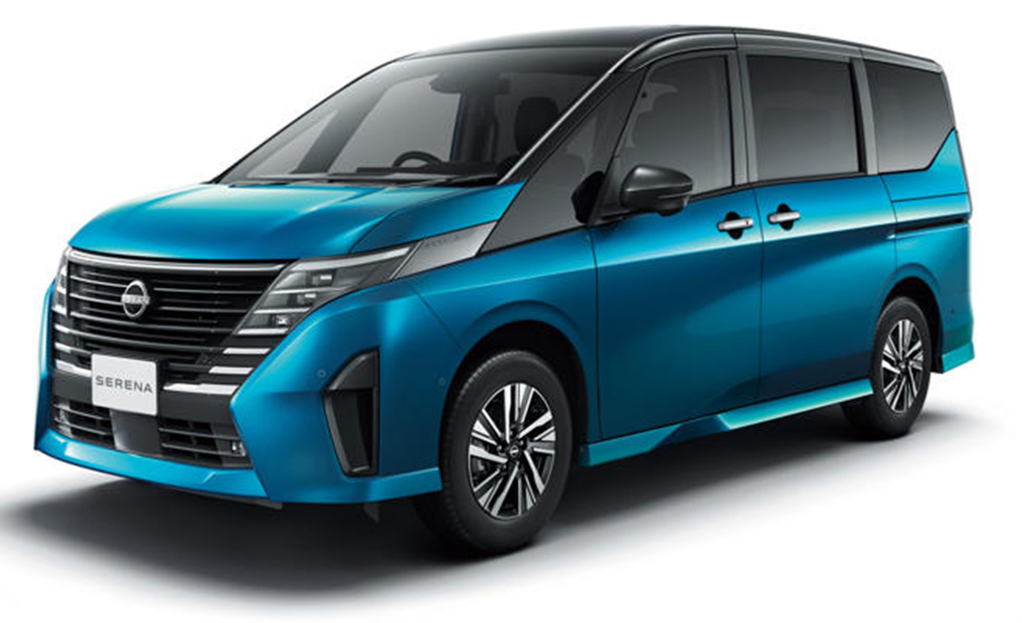
低炭素Al合金板材は、新型EV「アリア」や中型SUVの新型「エクストレイル」から採用し、順次採用車種を増やす。採用時期は2023年春以降で、適用部位はフロントフードやドアの外板などになる。
2025年2月、日産自動車は、「グリーン鉄」の採用を拡大すると発表。日本で製造する自動車向けの鋼板を対象に、2025年度にグリーン鉄の使用量を2023年度比で約5倍に増やす。鉄部品は車両重量の6割ほどを占める主要素材で、車両製造に関わるCO2の削減をめざす。
2023年から、主力のミニバン「セレナ」向けに神戸製鋼所のグリーン鉄を採用してきたが、今後は日本製鉄やJFEスチール、韓国鉄鋼大手ポスコホールディングスのグリーン鉄も段階的に採用を増やす。
メルセデスベンツ(Mercedes-Benz)
2021年5月、スウェーデンのH2グリーンスチール(H2 Green Steel)と提携を結び、自動車生産にCO2を含まない鋼材(グリーンスチール)の使用を2025年から開始すると公表した。「Ambition 2039」目標の一環で、EUが求めるよりも11年早い2039年にCO2ニュートラル達成を目指している。
2020年に創業したH2グリーンスチールは、鉄鋼生産において石炭(コークス)の代わりに水力、風力など再生可能エネルギー由来のグリーン水素と電力を使用する水素還元製鉄を進めている。鋼材生産過程で排出するCO2を最大95%削減できるとしている。
BMW
2022年2月、ドイツの鉄鋼メーカーであるザルツギッター(Salzgitter)と、2026年からグリーンスチールを調達する契約の締結を発表した。
ザルツギッターは、石炭(コークス)の代わりに水素を使って鉄鉱石を還元する水素還元製鉄や、電力に再生可能エネルギーを用いるなどして、CO2排出量を95%削減する。
他に2025年より、スウェーデンのH2グリーンスチールとも調達契約を結んでおり、欧州工場での鋼材使用量の40%以上をグリーンスチールに切り替え、40万トン/年のCO2削減を目指している。
ドイツの大手自動車部品メーカーのシェフラー
2025年以降、H2グリーンスチールから10万トン/年のグリーンスチールを調達する予定で、20万トン/年のCO2削減を目指す。また、2025年までには自社工場の75%、2030年までに自社工場のすべてについて、実質的な温室効果ガス排出量をゼロにすることを目標に掲げている。
自動車のボディー骨格を造る際に排出されるCO2をいかに減らすか──。素材~骨格部品の製造工程まで脱炭素化の観点から変革が進められている。その中で、今後、高張力鋼板(グリーンスチール)の冷間プレス材が主体となる方向が見えてきた。
一方、米国テスラが「モデルY」のリアボディー部品への採用を公表したことから、アルミニウム合金で一体成型するギガプレスが注目を集めている。今後、溶接組み立てから溶湯加圧成型による低コスト化がEVトレンドとなる可能性が出てきた。
ボディー骨格のプレス成形技術
これまでボディー骨格にはホットスタンプ材が使われてきた。それは厳しくなる世界の衝突安全基準への対応であり、衝突時の衝撃荷重でキャビン(乗員室)を変形させないため、特に強度が必要な骨格部品についてはホットスタンプ材が採用されてきた経緯がある。
トヨタ自動車
2023年3月、新型HEV「プリウス」(2023年1月に発売)から、先代車のボディー骨格で使っていた熱間プレス材(ホットスタンプ材)を冷間プレス材に変更したことが公表された。今後、脱ホットスタンプの対象は、高級ブランド「レクサス」を含む多機種へと拡大される。
新型プリウスでは、引張強さ1.5GPa級の熱間プレス材(ホットスタンプ材)を使っていたが、CO2排出量削減のために、1.5GPa級の冷間プレス材に変えたのである。鋼材を加熱しない冷間プレス材に変更することで、新型「プリウス」だけでCO2排出量を868トン/年削減できると試算している。
これまで製造コストが安い冷間プレス加工は、高強度・高延性・高寸法精度の骨格部品を造るのが難しく、引張強さ1GPa以下の骨格部品に使われてきた。今回、素材と成形方法を改良することで引張強さ1.5GPa級の骨格部品にも使用する。製造コストはホットスタンプ材と大きく変わらないという。
新型プリウスの骨格部品は、素材をJFEスチールなどから調達し、フタバ産業と豊田鉄工が製造する。部品表面に「ビード」(溝のような凹凸)を付けるなどでスプリングバック量を減らして寸法精度を高め、成形時の「しわ」や「割れ」などの防止対策が行われている。
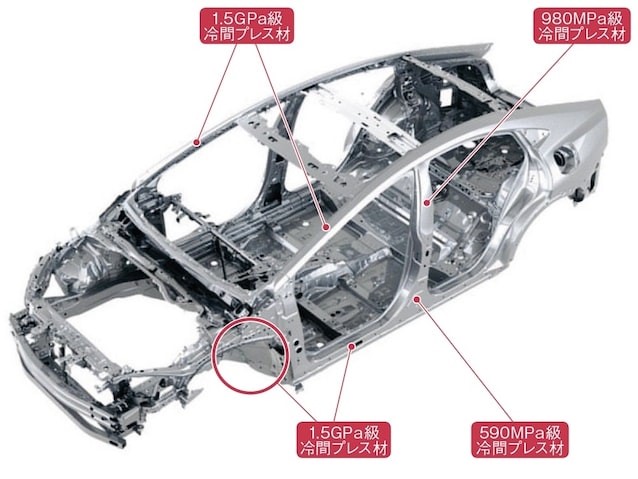
2023年9月、約3分間で車体の1/3を一体成型できる「ギガキャスト」の試作機を明知工場で公開した。高さ約6m、幅約7m、奥行き約15mの設備で、溶かしたアルミ合金を流し型に流し込み、700℃から250℃まで一気に冷却して固めて取り出す。2026年投入予定のEVで採用する。
マツダ
鋼板を主体としたボディー骨格を選択しており、冷間プレス材を基本とし、骨格部品ごとにホットスタンプ材と冷間プレス材を使い分けて、製造時のCO2排出量削減と経済性の両立を追求している。
CO2排出量削減の観点からは、ホットスタンプ材は骨格部品の成形工程(加熱工程)でCO2を多く排出する。一方で、冷間プレス材は加熱が不要のため成形工程におけるCO2排出量は少ないが、鉄鋼メーカーの鋼材製造工程(必要な強度を出すための熱処理工程)でCO2を排出する。
そのため、CO2排出量削減に関しては、鋼材の製造から骨格部品の製造までのトータルでみる必要があるとし、経済性を含めて鉄鋼メーカーと共同で検証する方針を示している。
経済性の観点からは、ホットスタンプ材は冷間プレス材よりも生産性は良いが、製造コストが高い。そのため、熱間プレス成形時の「多数個取り」、「パッチワーク工法」、「熱間トリム加工」などの採用で低コスト化の検討を進めている。
日産自動車
採用を進めているグリーン鋼材は、熱間プレス加工と冷間プレス加工のいずれも適用できるため、基本的にはどの骨格部品にも適用は可能である。グリーン鋼材は通常の鋼材に比べて材料コストは高いが、骨格部品の鋼材製造工程からのCO2排出量の削減を重視して採用を決めている。
ボディー部品の溶湯加圧成型技術
アルミニウム合金を溶かして大型の鋳型に高圧で流し込み、車体部品の1/3ほどをアルミニウム合金で一体成型できる米国テスラのギガプレスが注目を集めている。多数の部品を溶接で組み立てる従来プロセスに比べて圧倒的な低コスト化が可能で、「モデルY」への採用を公表した。
大型成型機の開発を先駆けたのは中国の工作機械大手のLKテクノロジー・ホールディングス(力勁科技集団)で、2008年にイタリア機械大手イドラを買収し、2019年に6000トン級を発売した。現在は2万トン級を開発中で、合衆新能源汽車のEVブランド「NETA」と連携し同社工場に納入を予定している。
LKテクノロジー傘下イドラや中国海天グループ、スイス機械大手ビューラーも開発・販売を強化している。
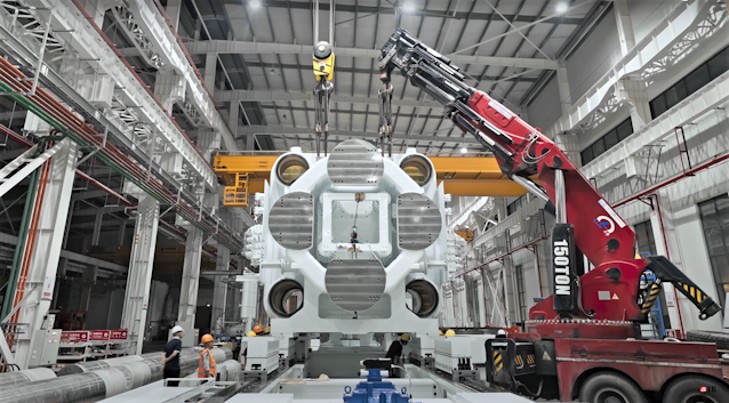
米国テスラ
ここ数年、製造を大幅に簡素化できる大型鋳造部品を実現するため、アルミニウムの鋳造技術や合金技術に積極的に投資し、世界最大級の鋳造機を数台導入し、米国フリーモント、テキサス、ドイツベルリン、中国上海のギガファクトリーに配備している。
2021年12月、巨大な鋳造機(12000トン・ギガプレス)を使って、「モデル3」では70個の部品で構成されていたリアボディー部品を、2個のリアボディー部品に置き換えた「モデルY」を公表している。同じアプローチの中国自動車メーカー約6社とも協力している。

米国テスラでは約170個あった金属部品を2個の大型アルミ部品に置き換え、約1600カ所必要であった溶接を不要とした。米国ゴールドマン・サックスによると、テスラのEV原価は2021年には3万6000ドル(約480万円)で、一体成型を採用する前の2017年当時と比べて1/2になった。

トヨタ自動車
2023年6月、トヨタ自動車は、2030年にBEVの世界販売台数を、2022年実績の約140倍に相当する350万台に伸ばす計画を掲げる。このうち170万台は、BEVファクトリーによる次世代BEVが占める見通しで、「ギガキャスト」と呼ばれる溶湯加圧成型部品を採用する。
2027年に投入する「レクサス」のEVからギガキャストを採用し、車体下部の前部と後部でギガキャストを用いる。試作では前部の91部品・51工程を1部品・1工程に集約でき大幅なコスト削減を実現している。未完成車両が無人で自走し、次工程に移動する仕組みも取り入れ、生産コストの半減をめざす。
UBEマシナリー
2023年4月、溶湯加圧成型装置を開発したと発表。2024年8月、EV等の車体構造部品をアルミニウム合金で一体成形するダイカスト技術「ギガキャスト」に対応したダイカストマシンを開発・上市した。型締力9000トンのダイカストマシンを「UH9000」として標準ラインナップ、装置価格は周辺機器を含めて数十億円/台である。
トヨタ上郷工場(愛知県豊田市)に納入し、田原工場(同県田原市)への追加設置も検討中である。
アルミニウム合金を溶かして大型の鋳型に高圧で流し込み、車体部品の1/3ほどをアルミニウム合金で一体成型できる。そのため、多数の部品を溶接で組み立てる従来プロセスに比べ、車体コストが約20%下がる。また、鋼をアルミニウム合金に置き換えることで、車体重量も30%程度軽くできる。
リョービ
2023年7月、自動車アルミ部品大手のリョービは、EV向けの生産技術「ギガキャスト」を使う大型車体部品の生産に参入する。約50億円を投じて静岡県の菊川工場の敷地内に建屋を新設し、6000トン級の成型機を導入する。2025年3月から、主に国内の自動車メーカーなどからの部品受注を見込む。
将来は自動車メーカーの工場への成型機の設置や運用、保守なども行う。同事業には、カナダのアルミ部品大手のリナマーなどが参入を表明している。ギガキャストは部品製造時のCO2排出量を減らせる。アルミニウムのリサイクル品を使うことで、新品のアルミ合金に比べて1/10以下となる。
芝浦機械
2025年2月、ギガキャスト市場への参入を発表。型締め力:6100〜1万2000トンの鋳造設備を開発しており、3月中に発売し、日本、北米、インド、韓国の自動車メーカーや大手サプライヤーなどに売り込み10台/年の販売をめざす。一般的には型締め力が6000トン以上のアルミ鋳造設備をギガキャストと呼ぶ。
型締め力1万2000トンの設備は国内最大級で、幅:27m、奥行き:9m、高さ:9mで、総重量は1100トンにも及ぶ。これまで135〜4000トン級を製造してきたが、ギガキャストは相模工場や海外の協力工場で部品を製造し、顧客の工場で最終的に組み立て、1台数十億円規模になる。
スウェーデンのボルボ・カー、ドイツのフォルクスワーゲン(VW)、中国の小鵬汽車(Xpeng)や浙江吉利控股集団なども、ギガキャストの導入を計画している。
しかし、ギガキャストで製造した部品が事故で破損した際、全て交換する必要が生じる可能性があり、修理費用が高額になりやすく、製造プロセスでも部品が大きいために品質安定化も重要課題である。
グリーン・タイヤとは
2023年4月、住友ゴム工業は製造段階で排出するCO2を実質ゼロに抑えたタイヤを公開した。太陽光発電と水素を活用し、製造段階で必要なエネルギーをまかない、高級車向けタイヤ「ファルケン」でカーボンニュートラルを実現した。福島県の白河工場で製造を開始し、6万本/年程度の製造を予定する。
一方、2024年6月、タイヤ大手がEV向けタイヤを相次いで投入していると報じられた。
2024年2月、ブリヂストンは、静粛性・乗り心地・運動性能などタイヤに求められる基本性能を進化させた乗用車用プレミアムブランド商品「REGNO GR-XⅢ」を発売した。「EV時代の新たなプレミアム」と位置付ける商品設計基盤技術ENLITENを、国内市販用乗用車向けタイヤとして初搭載した。
EVで課題となる航続距離を伸ばすため、ゴムの使用量を減らして軽量化し、乗り心地や運動性能も向上させたほか、新たな溝の形状を取り入れるなどして、静粛性も高めた。
2024年3月、住友ゴム工業は、低燃費(電費)性能を実現した小型EVトラック向けリブタイヤ「e. ENASAVE SPLT58」を発売した。航続距離を伸ばすことに加え、専用バッテリー搭載による車重増によるタイヤ摩耗を抑えることを目的に開発された。
トレッド幅とショルダープロファイルを最適化し、余分なゴムを削減して燃費悪化の要因となる無駄な発熱を抑制した。これにより、転がり抵抗係数を従来品「DUNLOP ENASAVE SPLT50M」比で21%低減した。
2024年6月、トーヨータイヤ(TOYO TIRE)は、小型EVトラック専用リブタイヤ「NANOENERGY M151 EV」を発売した。ラストワンマイルを担う小型トラックは、車両荷重が増大するほか、パワフルな駆動力によって加速性能が向上し、回生ブレーキが強くなるなど、タイヤに対する負荷が高い。
非対称パターンと溝形状の工夫、ゴムの耐摩耗ナノ・コンポジット・ポリマー複合化により、低電費性能、転がり抵抗低減に加え、耐摩耗性能を従来品「低メンテナンスリブタイヤM125ZB」比で21%向上させた。
2025年1月、TOYO TIREは、植物由来やリサイクル材などサステナブル(持続可能)な素材が使用原材料の91%を占めるタイヤを開発した。2024年1月に発表した使用率が90%のタイヤを、さらに1ポイント高めた。主力ブランド「オープンカントリー」を冠し、実際に走行可能な強度・品質を備える状態で試作した。
TOYO TIREは市販するタイヤなどのサステナブル素材使用率を、2030年時点で40%、2050年には100%とする目標を掲げている。
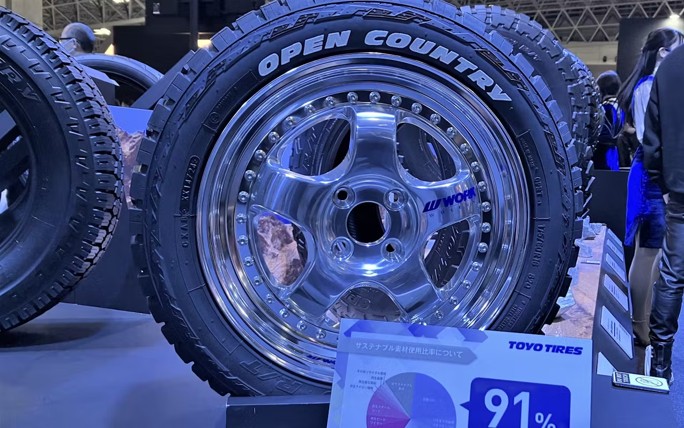
ブレーキ、その他
ディスクブレーキは、鋳鉄・鉄鋼製ロータ表面に耐熱・耐摩耗コーティングとして自溶性合金溶射、アーク溶射(AS)によるCu-FeCrC皮膜、APSや高速フレーム溶射(HVOF)によるWC-NiCo皮膜が採用され、ブレーキパッドで挟むことで安定した制動力を発生させている。
2023年11月に欧州議会で成立した次期排ガス規制(Euro7)で、タイヤとブレーキからの非排気粉塵が規制対象に加えられた。規制は2025年と2035年の2段階で強化される。また、米国ワシントン州とカリフォルニア州では、生態系への影響防止から、ブレーキ摩擦材に含まれる化学物質規制の州法が発効された。
そのため、ブレーキメーカーを中心に低粉塵摩擦材の開発や、レーザークラディングなどの新プロセスの適用が進められている。また、軽量化と耐熱性向上をめざすC/CコンポジットやSiC/SiC複合材料製のブレーキ用ディスクロータも、高級車向けに実用化しており、電気自動車向けの新展開が進められている。
2024年8月、日産自動車は、放射冷却素材の技術を持つ中国ラディクールと共同で自動車用に放射冷却塗料(自己放射冷却塗料)を開発した。塗膜に2種類のマイクロ構造粒子①近赤外線を反射させる粒子と、塗膜の温度が上昇した際に②電磁波を放射して熱を外に放出する粒子を分散させることで実現した。
新塗料はトップコートの下に塗るカラーコートとして使う。開発当初は120㎛と厚く、薄膜化を進めているが量産車で適用される20㎛には達していない。そのため、特装車両への適用や塗料としての販売を検討する。
日産自動車は、ラディクールジャパンの販売代理店である日本空港ビルデングの協力を得て、2023年11月から1年間の実証実験を羽田空港で実施している。ANAエアポートサービスが同空港で使用している「NV100クリッパーバン」に当該塗装を施し、塗装の効果や耐久性の検証を進めている。
マルチマテリアル化とは
自動車の燃費向上を目的に、エンジン効率向上、車体(ボディ)の空気抵抗低減、タイヤの低ころがり抵抗化などの研究開発は継続的に進められてきた。2010年代に入ると新構造材料による車両の軽量化に注目が集まり、新エネルギー・産業技術総合開発機構(NEDO)のプロジェクトが発足している。
すなわち、新構造材料研究組合(ISMA)では、30を超える企業・大学・研究機関と連携し、自動車を中心とした輸送機器の抜本的な軽量化(重量半減)に向けて、主要な構造材料の高性能化とマルチマテリアル化の技術開発を行う「革新的新構造材料等研究開発」プロジェクトが推進されている。
図1には、車体の軽量化に向けた適切な材料選択の例を示す。このようなマルチマテリアル化を実現するために、プロジェクトでは次のような開発が行われた。
・新構造材料研究組合HP、http://isma.jp/ja/works/
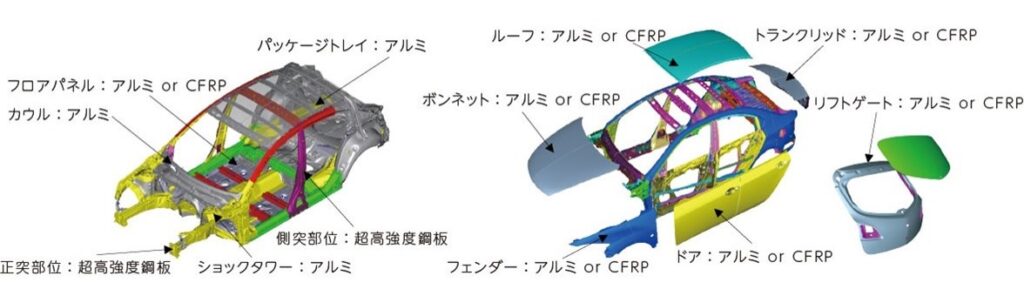
出典:新構造材料研究組合、http://isma.jp/ja/works/
2013~2017年には、高張力鋼の高延性化(引張強度:1500MPa、伸び:20%)、難燃性マグネシウム合金(引張強度:363MPa、伸び:15%)や高強度アルミニウム合金(引張強度:739MPa、伸び:15.3%)の開発などが行われた。
また、短繊維強化の熱可塑性炭素繊維強化樹脂(CFRTP:Carbon Fiber Reinforced Thermo Plastic)による車体/構造用部品の試作が行われた。
さらに、溶融接合や摩擦撹拌接合(FSW:Friction Stir Welding)による同種材料(炭素鋼板-炭素鋼板)の接合、異種材料の接合技術開発(炭素鋼板-CFRPの接着接合、アルミニウム合金-炭素鋼板のスポット溶接、アルミニウム合金―CFRPのFSWなど)が実施された。
また、2018~2020年には、マルチマテリアル化を目指した技術や部品化の課題を解決し、衝突安全性に考慮した構造設計を行うなど、自動車ホワイトボディのモデル化の検討を行うなど、実用化・事業化を目指した研究開発が推進された。
2022年6月、大王製紙はレース用EV部品への植物由来素材「セルロースナノファイバー(CNF)」の提供を発表した。2018年から部品提供を開始、2021年にドアやルーフパネルに採用され、今回は愛媛大学や川之江造機と開発した新成型方法でバンパーやボンネットなどの大型部品にCNFを適用した。
CNFは原料のパルプをナノ(ナノは10億分の1)メートル単位に細かく解きほぐして作り、同社のCNF成形体は引張強度がプラスチックの約5倍であり、車体の軽量化による燃費向上に寄与する。置き換えた部分は約5割の重さになり、米国コロラド州のレースでの公道検証が行われる。
マルチマテリアル化の本質的な目的は、適材適所よるものづくりにある。この適材適所はガソリン車、ハイブリッド車、電気自動車、燃料電池車などの車種とは無関係に、自動車に共通の課題である。
自動車において革新的な軽量化を実現するために、従来はオール炭素鋼製であったボディーを薄板の高張力鋼板に置き換えたり、部分的にアルミニウム合金、マグネシウム合金、炭素繊維強化樹脂(CFRP:Carbon Fiber Reinforced Plastic)などの軽量材料への置き換えが進められている。
一方で、これらの各種材料をボルトやリベットなどの機械的締結でつなぐことは、基本的に軽量化とは相反する。そのため、革新的な軽量化を実現するためには異種材料の継手設計と、異種材料間の接合技術の開発が不可欠となる。
異種材料の継手設計とは
異種材料の継手部が有する特有の力学的問題として、材料不連続による応力集中があげられる。すなわち、図2(a)に示すように、き裂のような応力集中源を有する平板が一様に引張荷重を受ける場合、き裂の先端近傍には(1)式で示すような顕著な応力集中が生じることは良く知られている。
・異種金属接合継手の設計法、機械の研究、55-7、(2003)757-766.
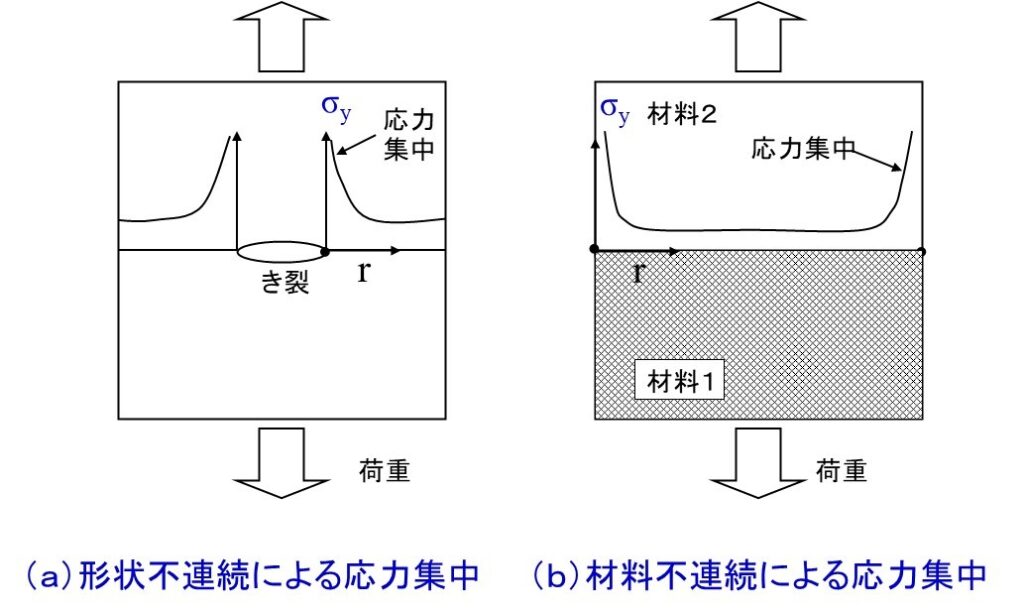
σy=KⅠ/(2πr)1/2 (1)
ただし、KⅠ:応力拡大係数であり、作用する荷重やき裂長さ、平板寸法で決まる。(π=3.14)
これは形状の不連続による応力集中と呼ぶことができ、脆性破壊や疲労破壊などのように局部応力によって破壊が生じる場合の原因となる。一般に接合部の多くは形状の不連続部に設けられるため、従来から接合部の継手設計においては形状による応力集中を十分に考慮する強度設計が行われている。
一方、図2(b)には材料不連続による応力集中を示すが、これに関しては十分に認識されているとは言い難いのが現状である。すなわち、図に示すように形状不連続のない平板の場合でも、異種材料の接合界面端部近傍には次式で示すような顕著な応力集中が生じる。
σy=KⅠ‘/(2πr)p (2)
ただし、KⅠ‘:接合界面端部の応力拡大係数、p(θ):応力特異性指数は材料1と材料2の接合界面端部でのアペックス角度θの関数である。(図1(b)ではθ=90°)
形状不連続による応力集中の度合いは、形状によって大きな影響を受けるが、材料不連続による応力集中の度合いは材料1と材料2の弾性定数(弾性率、ポアソン比)の差によって影響を受ける。
材料不連続による応力集中は(2)式から分かるように、接合界面端部近傍の応力が接合界面端部に向かって無限大に発散する。ただし、0<p(θ)<1であり、p(θ)が大きくなるほど応力集中は顕著となる傾向を示す。
p(θ)=0.5の場合には、(1)式で示すき裂と同じ応力特異性を示すことから、材料不連続による応力集中の厳しさは明らかである。しかし、アペックス角度θを適切に選定することでp(θ)=0とすれば応力特異性は消失し、接合界面の応力集中低減のためには有効な手段である。
このような異種材料接合界面の端部に生じる応力特異性については、多くの異種材料の組み合わせやその継手形状により異なるため、異種材料継手の設計法の概念を構築し、継手設計指針として体系的にまとめる必要がある。
図2には、異種材料の平板で構成される継手形状の基本形式をまとめて示す。突合せ継手は図中に示すI型突合せ継手(θ1=90°)が一般的であるが、異種材料継手においては接合面積を大きくするために、接合面を斜めとしたスカーフ継手(θ1≠90°)が使われる場合も多い。
この場合の接合界面端部近傍の応力集中は、図中の右側に示すように材料1と材料2の接合界面が自由縁とアペックス角度θ1で交差する場合にモデル化することができる。アペックス角度θ1を適切に選定することでp(θ)=0とすれば応力集中を軽減することが可能である。
その他、T継手、角継手、重ね継手などがある。中でも、重ね継手は接合面積を自由に選ぶことができるため、異種材料継手では多用される。これら3種類の異種材料継手の接合界面端部近傍の応力集中は、図3右側に示すように材料2が端部角度θ1で材料1と接合される場合にモデル化できる。
このようなモデル化した各種の異種材料継手(アルミニウムータングステン、アルミニウムー炭素鋼、アルミニウムー銅、チタン―ニッケル、チタンー銅など)のスカーフ継手については応力特異性解析が行われており、応力特性指数p(θ1)を低減できる継手端部角度θ1が明らかにされている。
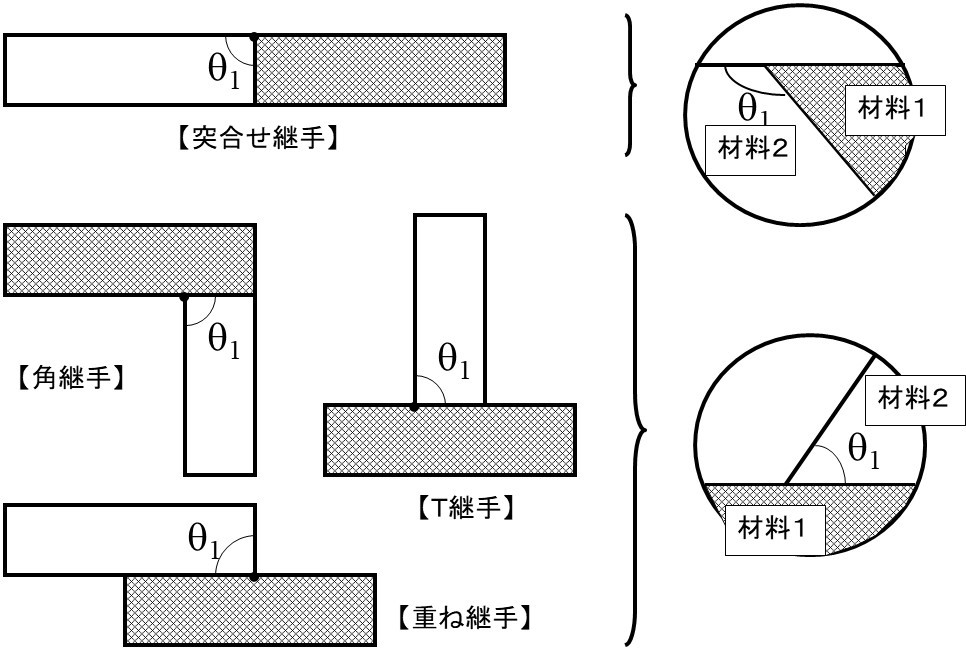
以上で示した異種材料継手の設計法の有効性は、有限要素法解析や実験検証により確認されている。
実際に、接合界面に脆弱な金属間化合物層が形成された銅とアルミニウムの摩擦圧接継手を対象に、接合界面形状を制御して接合界面端部における応力集中を低減することで、衝撃強度が大幅に向上し信頼性が改善できることが明らかにされている。
また、炭素鋼とアクリル樹脂(PMMA)の接着継手の曲げ強度の向上や、アルミニウム合金基材に形成された13Cr鋼溶射皮膜の界面端部からのはく離強度の向上などにも有効であることが明らかにされている。
接合・接着技術の取り組み
図4には、自動車生産で利用されている接合技術と、次世代に向けて適用開発が進められている接合技術をまとめる。現在、自動車で利用されている機械的締結は、リベット接合や下穴をあけずに上板を貫通し下板を貫通させないセルフピアスリベット(SPR:Self Piercing Rivet)締結である。
海外では、上下板をスクリューで貫通させる一方向ドリルスクリュー(FDS:Flow Drilling Screw)締結も採用されている。SPRとFDSは、同種材料接合あるいは異種材料接合でも適用が可能である。
また、自動車用鋼板は薄板が多いため、溶接入熱を下げて鋼板のひずみを抑制する必要がある。そのため溶接する鋼板を電極で挟み込み、加圧しながら電気を流して抵抗熱で接合する抵抗スポット溶接、抵抗シーム溶接が多用されており、低入熱アーク溶接、鋼板の抵抗スポット溶接に代るレーザースクリュー溶接(LSW:Laser Screw Welding)などが採用されている。
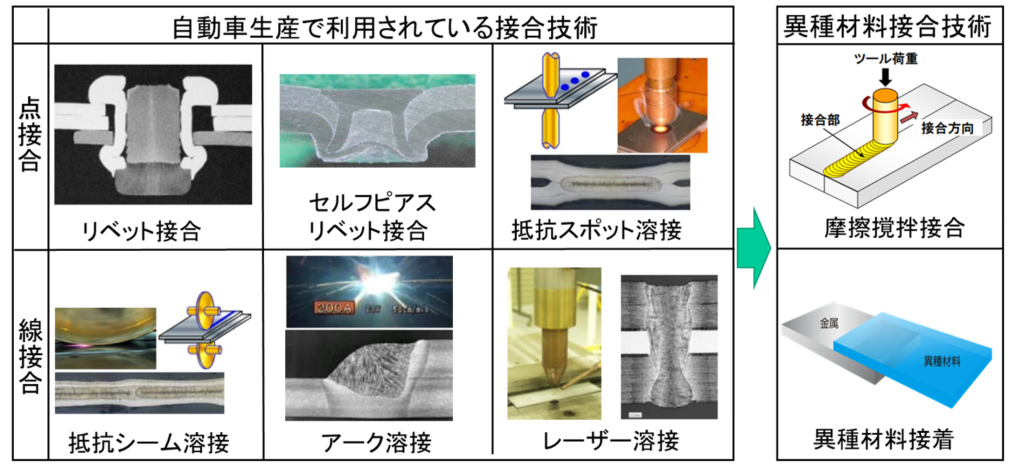
次世代の異種材料接合技術として注目度の高いのは、1991年に英国溶接研究所(TWI:The Welding Institute)で開発された摩擦撹拌接合(FSW:Friction Stir Welding)である。
先端に突起のある円筒状の回転ツールを接合部材に圧入し、その摩擦熱で部材を軟化させ、回転力で接合部周辺を塑性流動させて接合するプロセスである。大気中での溶接が難しいアルミニウム合金の接合プロセスとして多用され、電車の車体に採用されている。
最近ではアルミニウム合金と他の材料(炭素鋼、マグネシウム合金、チタン合金、樹脂など)との異種材料接合技術としてFSWの適用が検討されている。
・(株)東レリサーチセンター、FSWによる異種材料接合に係る最近の研究概況、No.0356 、2018/06/04
- アルミニウム合金ー熱可塑性樹脂(ポリアミド(PA)、ポリカーボネート(PC)、アクリロニトリル・ブタジエン・スチレン(ABS)、ポリエチレンテレフタレート(PET)、高密度ポリエチレン(HDPE)など)
- 炭素鋼ー熱可塑性樹脂(同上)
- アルミニウム合金ー炭素繊維強化プラスチック(CFRP)
- 炭素鋼ー炭素繊維強化プラスチック(CFRP)
その他、FSW以外のプロセスによる異種材料接合技術としては、炭素繊維強化熱可塑性プラスチックと金属材料間の接合に注目度が高まっている。
- 超音波振動ツールによるアルミニウム合金ーCFRTPの接合
- 高周波誘導加熱によるアルミニウム合金ーCFRTPの接合
- レーザー加熱による亜鉛メッキ鋼板ーCFRTPの接合
一方で、熱可塑性樹脂(CFRTPを含む)ー金属材料の接着技術の開発も着実に進められており、あらかじめ金属表面を化学処理やレーザー加工の前処理により凹凸を付与することで、アンカー効果により高い接着継手強度が実現されている。
ただし、前処理と接合工程までの時間経過により、接着継手強度が低下するため、品質保証上の問題となっている。そのため前処理後にすぐに接合ができる複合装置の開発が行われている。
・日経クロステック、https://xtech.nikkei.com/atcl/nxt/column/18/01516/00004/
また、接着剤をシート状に加工した加熱硬化型の「粘接着フィルム」の開発も行われている。接着継手の強度は、接着層の厚さが増すほど低下する傾向を示す。そのため接着剤を厚さが100μm程度のシート状にすることで、接着継手の品質を高め、同時に接着作業の効率化が行われている。