2020年度の国内年間発電電力量は、水力を含む再生可能エネルギー20%、原子力発電所4%、火力発電所76%(LNG39%、石炭31%、石油等6%)である。欧米の先進国を中心として世界的に進む「脱石炭火力発電所」の動きに、日本は大きく遅れているのが現状である
国内の事業用火力発電所は、石炭火力発電所とLNG焚コンバインドサイクル発電所が中心に運用されており、石油火力発電所は予備電源と位置付けられている。一方、再エネ出力制御が定常化しつつある現状で、ガスエンジン発電の注目度が上がっている。
火力発電システムの分類
多くの熱機関の中で、一般に火力発電には外燃機関である蒸気タービンと、内燃機関であるガスタービン、ガスエンジン、ディーゼルエンジンが実用化されている。
蒸気タービンによる火力発電システムはボイラを別置きとするため大規模設備となるが、スケール効果が大きく大規模集中型電源として多用されている。ガスタービンは燃焼ガスを直接タービン翼に吹き付けて回転力を得るため、蒸気タービンに比べてコンパクトで起動性能に優れている。
事業用火力発電所には蒸気タービンのみによる石炭火力発電システムと、ガスタービンで発電した後、その高温排熱を利用して蒸気タービンを回転させる高効率のLNG焚ガスタービン・コンバインドサイクル発電システムが主に採用され、石油火力発電所は予備電源と位置付けられている。
また、ガスタービン、ガスエンジン、ディーゼルエンジンは、自家発電や非常用電源などの分散型発電として使われてきた。天然・都市ガス焚ガスコージェネレーションシステムは、発電と同時に発生する熱を有効利用することで、70~85%の高い総合エネルギー効率を実現している。
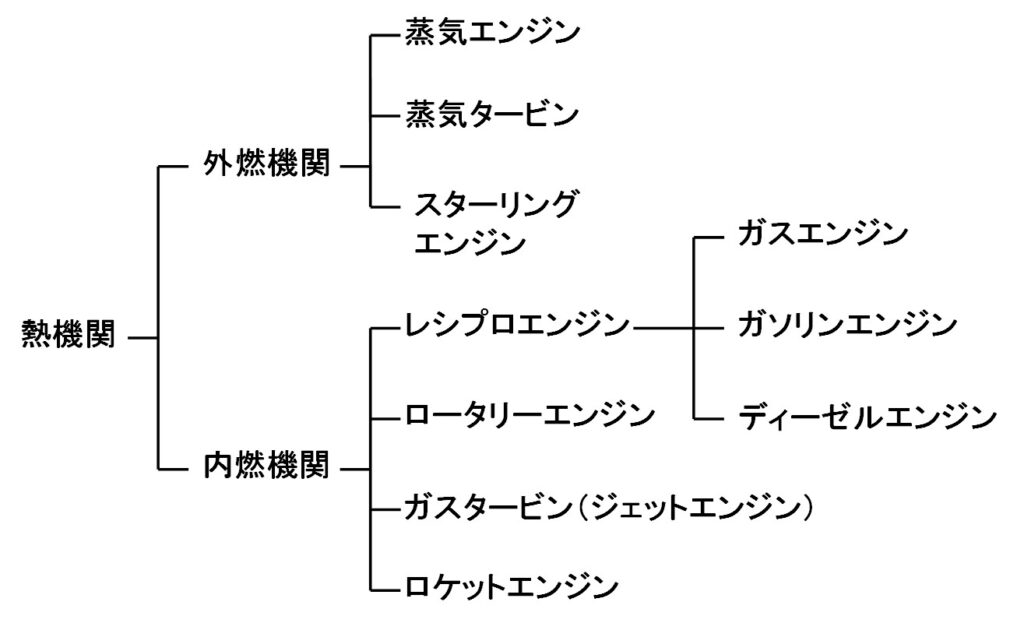
火力発電電力量の推移
現在、火力発電所で使われている燃料は液化天然ガス(LNG:Liquid Natural Gas)、石炭、石油である。1970年代の石油ショック後、エネルギー基本計画で石油火力発電を減らし、代替エネルギーとして原子力発電、LNG火力発電、石炭火力発電を積極的に導入してきた。
しかし、2011年3月、東日本大震災で東京電力福島第一原子力発電所事故を契機に状況は大きく変化する。安全対策を含む総点検のために発電電力量の25%を占めた原子力発電所を順次に休止させ、再生可能エネルギーを主力電源とし、不足分を火力発電所の増強により補う計画を進めた。
しかし、東日本大震災から11年を経たにも関わらず、エネルギー基本計画で主力電源と位置付けた再生可能エネルギーは10%程度の増強に留まり、安全を最優先に進めるとした原子力発電所の再稼働も十分には進められず、出来る限り引き下げるとした火力発電比率もほぼ横ばいとなった。(図2参照)
その結果、2020年度の国内年間発電電力量は、水力を含む再生可能エネルギー20%、原子力発電所4%、火力発電所76%(LNG39%、石炭31%、石油等6%)である。欧米の先進国を中心として世界的に進む「脱石炭火力発電所」の動きに、日本は大きく遅れている注)。
注)フランスは2021年、英国は2025年、カナダとイタリアは2030年までに、石炭火力発電所の廃止を表明している。石炭火力発電の割合の高いドイツも段階的廃止の完了時期を2030年に前倒しを表明し、米国は豊富に産するシェールガスを燃料とするLNG火力発電への移行が進む見通しである。
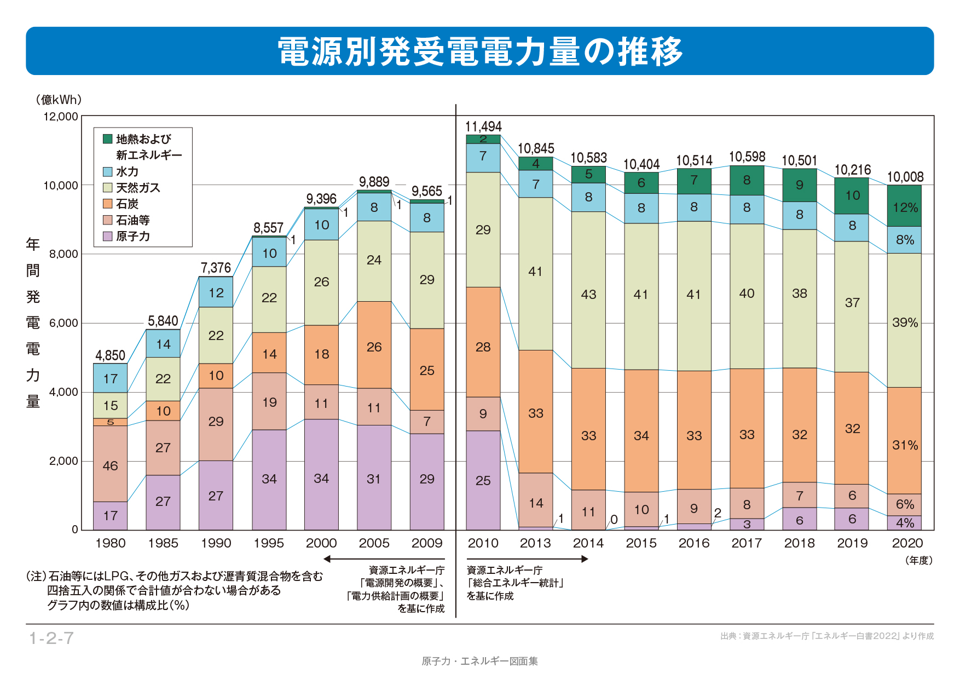
ところで、火力発電に使われる石油は環境規制をクリアするために、硫黄酸化物(SOx)の発生量が少ない超低硫黄原油(硫黄分0.1%以下)が主に使われており、助燃用には重油も使われている。常温で液体の石油は、LNGや石炭と比べて貯蔵や運搬が容易であるが、燃料価格は割高である。
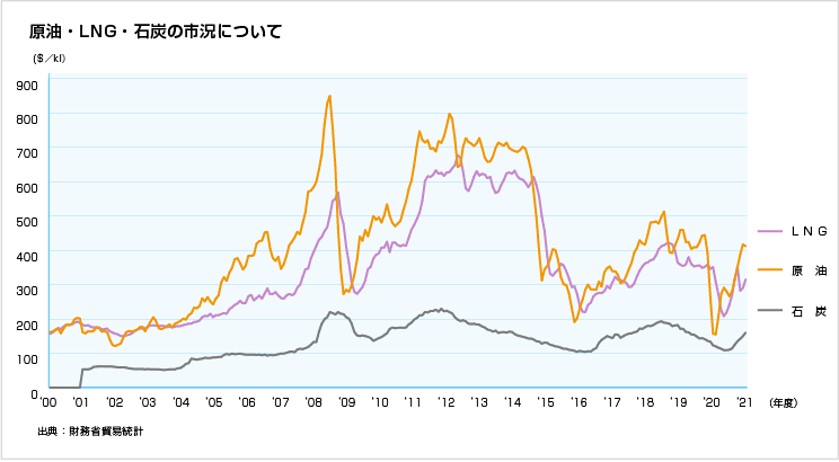
日本では1970年代の石油ショック以後、石油火力発電を減らすことをエネルギー政策として進めてきた。発電所の新設も原則禁止しており、老朽化により石油火力発電は日本各地から少しずつ無くなっている状況にある。現在は電力不足時のピーク電源として使用されることが多い。
日本の火力発電は、石炭火力発電とLNG焚コンバインド・サイクル発電が主体である。
石炭火力発電所とは
石炭は一般炭と原料炭に分類されるが、石炭火力発電用に使われるのは「一般炭」で、単位重量あたりの発熱量は相対的に低く、燃焼させるには大型ボイラが必要である。また、固体のためコンベアなどの運搬設備が必要で、硫黄・窒素の含有量が多いため燃焼時にSOxゃNOxも発生する。
石炭火力発電所の全体構成
石炭火力発電所の全体構成を、図4に示す。
石炭船から陸揚げされた石炭は、貯炭場を経て微粉炭機で粉砕される。ボイラ内で微粉炭を燃焼して蒸気を発生させ、蒸気タービンを回転させて発電機で発電する。蒸気タービンを駆動させた蒸気は復水器で冷却されて水に戻り、再びボイラに送り蒸気に変換され、これが繰り返される。
日本では復水器の冷却には、大量の海水が使われる。ボイラの排ガス中に含まれる有害物質は排煙脱硝装置、電気式集じん装置、排煙脱硫装置により排出基準値以下となるよう除去した後に、煙突から大気中に放出される。
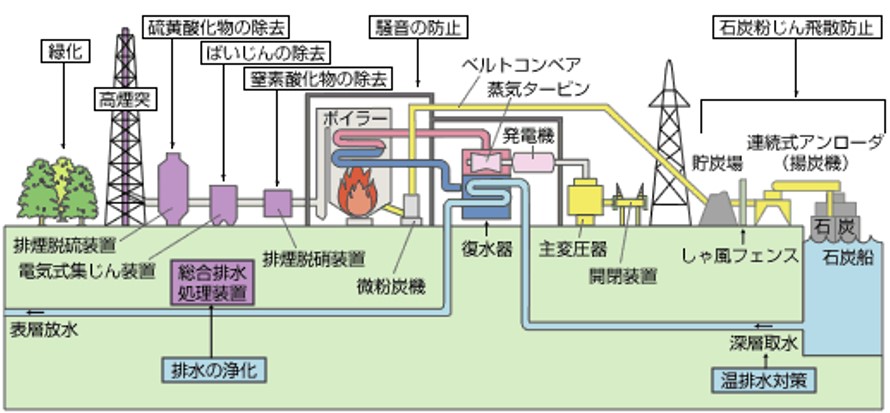
発電用ボイラの構造例
図5に、発電用ボイラの構造例を示す。ボイラでは復水器から戻された水を過熱器により蒸気に変換し、主蒸気管を使って高圧タービン入口に送る。仕事をした蒸気は温度が下がり湿り度が増すため、高圧タービン出口から蒸気を抽出し、再熱器に送って再加熱して中圧あるいは低圧タービン入口に送る。
ボイラでは、このような再熱サイクルを加えることで中圧あるいは低圧タービンでの液滴による損傷を防止すると共に熱効率を高めている。ボイラの中で過熱器管および再熱器管は最も高温にさらされ、過熱器管は高圧を受けることから構造材料の選択が重要となる。
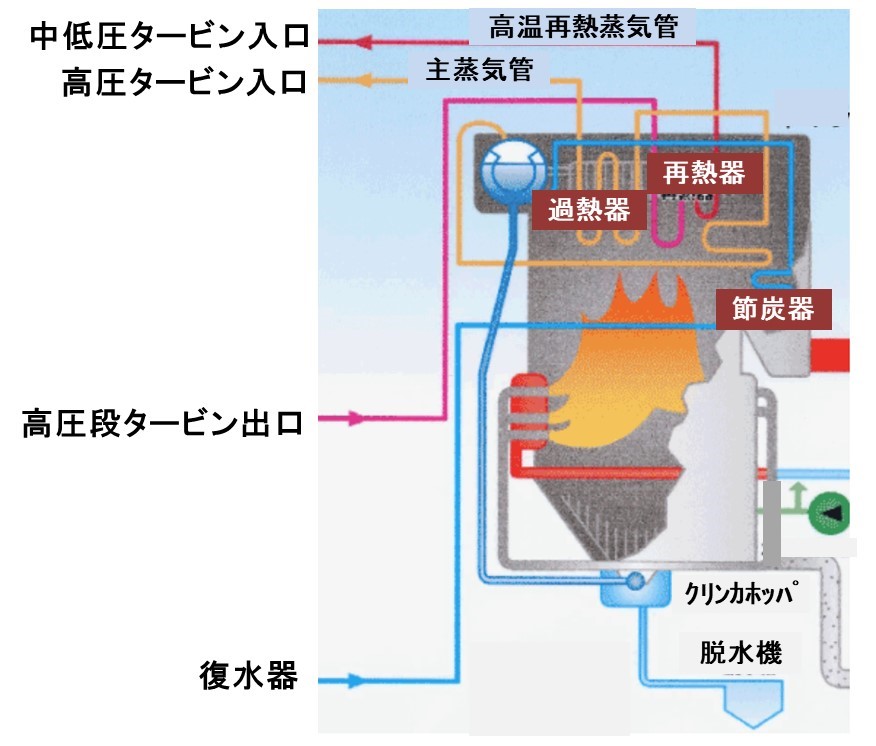
発電用蒸気タービンの構造例
図6に、発電用火力発電用の蒸気タービン構造例を示す。再熱再生復水タービンと呼ばれ、高圧段と中圧段に圧力の異なる高温蒸気がボイラから供給される。各段落ではケーシングに固定されたノズル(静翼)を通して、ロータに植えつけた動翼に蒸気が吹き付けられ、ロータが回転力を得る。
また、中圧段で仕事をした蒸気はクロスオーバー管を通じて低圧段に送られ、同様にケーシングに固定されたノズルを通してロータに植えつけた動翼に吹き付けられ、ロータが回転力を得る。
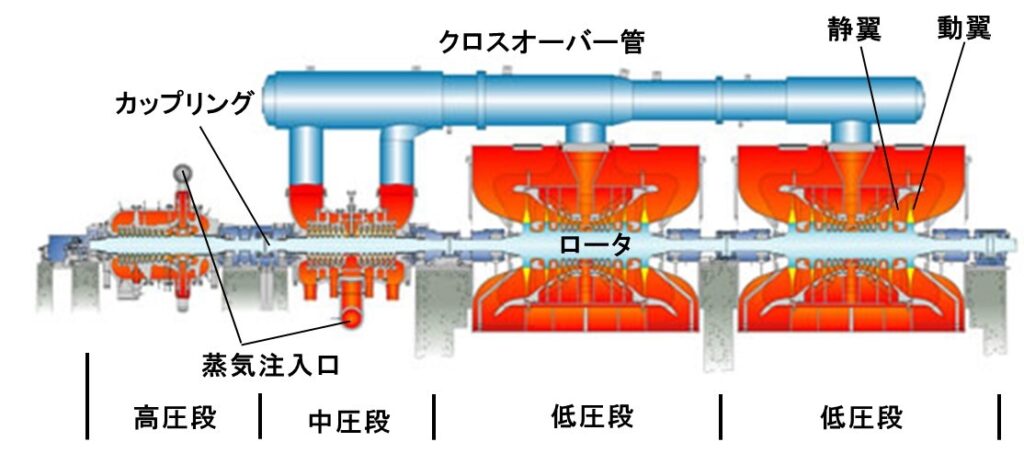
蒸気タービンのロータは発電機ロータに直結されており、発電機のコイルの中で発電機ロータに設置された磁石を回転させ、電磁誘導現象により回転運動を電気に変換する。
石炭火力発電所の高温・高圧化
火力発電プラントの高効率化は、蒸気条件の高温・高圧化の歴史である。これを実現できたのはボイラ材料と蒸気タービン材料の開発が大きな役割を果たしている。
(火力発電設備用材料、火力原子力発電、67-4、(2016.4)44-8.)
『火力発電プラントの高温・高圧化の歴史』
●1960年までに、石炭火力発電で主蒸気温度:566℃、主蒸気圧力:16.6MPaが採用
その後、石炭から重由・原油へと燃料転換が行われ、石油火力の大容量化と高効率化が推進
●1960年代後半に、石油火力発電で主蒸気温度:538℃、主蒸気圧力:24.1MP、出力:60万kWの超臨界圧プラントが建設
1973年の1979年の石油ショック後、石油→石炭への燃料転換が行われ、大容量石炭火力が実現
●1985年には微粉炭焚き超臨界圧プラント(主蒸気温度:538 ℃、主蒸気圧力:24.1MPa、出力:60万kW)が稼働
●1990年には微粉炭焚き超臨界圧プラント(主蒸気温度:538 ℃、主蒸気圧力:24.1MPa、出力:100万kW)が稼働
●1993年には再熱サイクルで蒸気温度:593℃が採用された微粉炭焚き超々臨界圧プラント(主蒸気温度:538℃,主蒸気圧力:24.1MPa,出力:70万kW)が稼働
その後、石炭火力で再熱蒸気温度の上昇により高効率化が実現
●1998年には微粉炭焚き超々臨界圧プラント(主蒸気温度:600℃、再熱蒸気温度:600℃,主蒸気圧力:24.5MPa,出力:100万kW)が稼働
●2000年には微粉炭焚き超々臨界圧プラント(主蒸気温度:600℃、再熱蒸気温度は610℃、主蒸気圧力:25.0MPa、出力:105万kW、発電端効率・LHVは45%)が稼働
●2009年には微粉炭焚き超々臨界圧プラント(主蒸気温度:600℃,再熱蒸気温度:620℃,主蒸気圧力:25.0MPa、出力:60万kW)が稼働
注釈:ボイラから蒸気タービンへ送給される水蒸気を、水の臨界点(373.95℃、22.064 MPa)を超える高温・高圧条件とすることで、水を蒸発させるための熱エネルギーを低減することができる。超臨界圧(SC:Super Critical)とは、蒸気圧力:22.064MPa以上、蒸気温度:566℃以下。超々臨界圧(USC:Ultra Super Critical)とは超臨界圧(SC)のうち、蒸気温度が566℃を超えるプラント。
超臨界圧火力プラントのボイラ材料
火力発電プラントの蒸気温度と蒸気圧力は、プラントの高効率化を目指して上昇してきたが、これを可能としたのは、高温強度に優れた構造材料の開発である。超臨界圧火力プラントのボイラ耐圧部で使用されている代表的な材料を表1に示す。
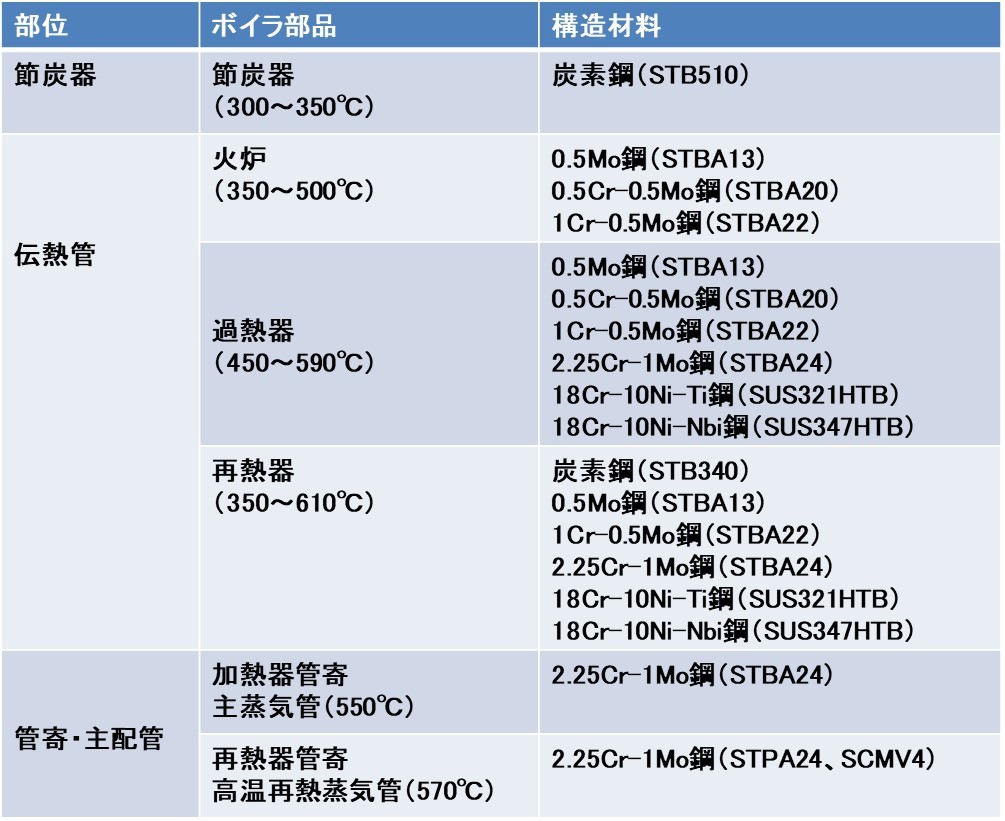
ボイラ材料は使用される温度域に応じて、高温強度、耐高温腐食性、耐水蒸気酸化性、組織安定性、溶接などの加工性、経済性などを考慮して選定される。
炭素鋼は400℃以上の高温で使用した場合に炭化物球状化や黒鉛化と呼ばれる劣化現象が生じる。そのため高温での使用は困難であり、非クリープ温度域で使用される節炭器に採用されている。
クリープ温度域ではあるが500℃以下で使用される火炉には、Mo、Crを少量添加した0.5Mo鋼や1Cr-0.5Mo鋼が採用されている。
500℃以上のクリープ温度域で使用される過熱器と再熱器には、クリープ&疲労強度、管内面の耐水蒸気酸化性、管外面の燃料不純物(Na、K、V、S)による耐高温腐食性も考慮した耐熱材料が開発されている。
実際に、従来の耐熱鋼にV、Nbを微量添加したフェライト系高Cr鋼である2.25Cr-1Mo鋼などや、304系ステンレス鋼にNb,Cuなどを添加したオーステナイト系高強度ステンレス鋼である18Cr-10Ni-Ti鋼、18Cr-10Ni-Nb鋼などが採用されている。
管寄および主配管は厚肉となるため、熱膨張係数が比較的小さい2.25Cr-1Mo鋼が採用されている。
超臨界圧火力プラントの蒸気タービン材料
超臨界圧火力プラントの蒸気タービンには鋳造・鍛造部品が多用され、代表的な材料を表2に示す。
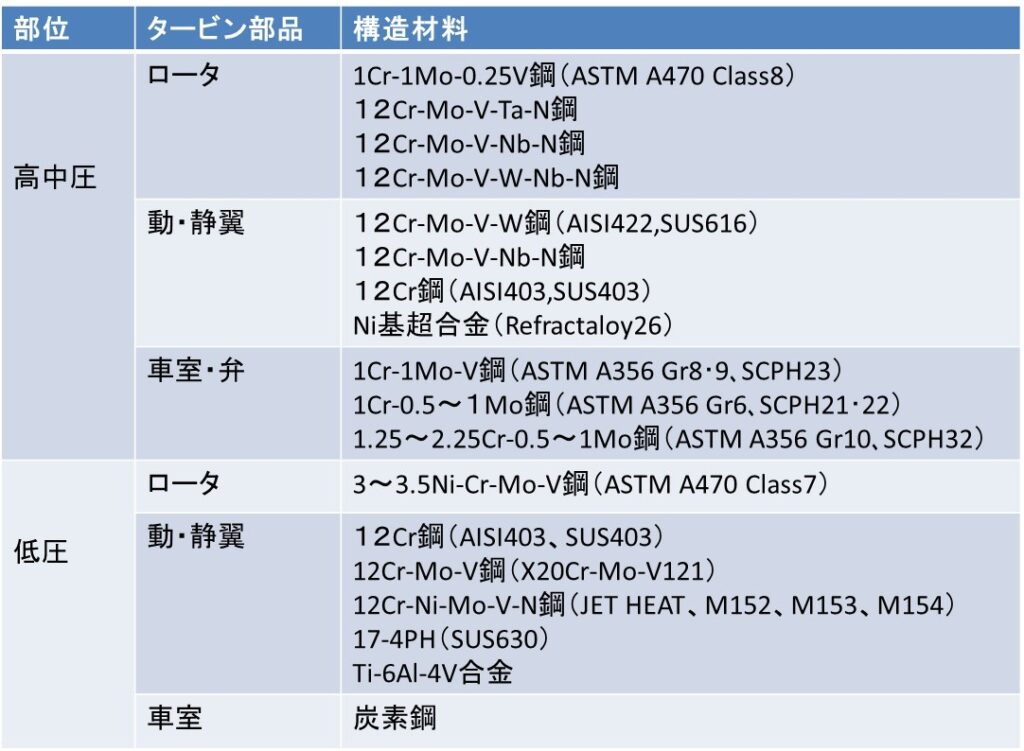
蒸気タービン材料は使用される温度域に対応し、ロータ、動翼、静翼、車室(ケーシング)などの要求特性に応じてタービンメーカーが選定している。
特に、耐SCC等の脆化対策も要求される蒸気タービン動翼は,遠心力による引張応力,蒸気推力による曲げ応力,回転に伴う振動応力を受けるため,高・中圧部には高いクリープ強度が,低圧部には高い降伏強さと破壊靭性値ならびに軽量化が要求される。
また,振動に対して減衰能が高い,切欠感受性が低いなどの特性と,耐脆化性,疲労強度が高いことも必要である。蒸気タービン静翼は高い曲げ応力を受けるため,優れた高温強度が必要である。
高圧・中圧ロータ材は高いクリープ強度と高温疲労強度が必要で、クリープ強度から570℃が適用上限の12Cr鋼を約600℃に高めた改良12Cr鋼が開発され、動静翼を含めて改良12Cr鍛鋼が使用される。高圧・中圧車室や弁にはCrMoV系や2.25Cr系鋳鋼、高圧・中圧初段動翼にはNi基超合金が使用される。
低圧ロータ材には、大型動翼の大きな遠心力に耐える降伏強さと高い破壊靭性値が必要で、NiCrMoV系鋼が使用される。鍛造により外表面から軸芯部まで均一な組織とし、介在物の偏析や内部欠陥が低く抑えられている。低圧ロータと動静翼には12Cr系鍛鋼が,低圧車室には炭素鋼板が使用される。
複合サイクル発電とは
燃料の液化天然ガス(LNG)は、メタンを主成分とする天然ガスをー162℃の超低温に冷却・凝縮して容積を約1/580にしたものである。石炭や石油と比べて燃焼時のCO2排出量やNOx(窒素酸化物)の排出量が少なく、SOx(硫黄酸化物)とばいじんが発生しない比較的クリーンな化石燃料である。
LNG焚コンバインドサイクル発電の全体構成
国内の主流は、ガスタービンと蒸気タービンを一軸に組み合わせたガスタービン複合サイクル(GTCC:Gas Turbine Combined Cycle )発電方式である。(火力原子力発電技術協会、火原協会講座37 コンバインドサイクル発電 、2011年05月)
図7には、北海道電力(株)石狩湾新港発電所のLNG焚コンバインドサイクル発電システムの全体構成を示す。米国GEが開発した1600℃級ガスタービン(9HA.01)に東芝の高効率蒸気タービンと発電機を組み合わせた定格出力:56.94万kW、発電端効率・LHV:62%のGTCCである。
2019年2月に1号機が稼働しており、1~3号機を合わせて総出力:170.82万kWの計画である。再生可能エネルギー向けに調整用電源として使用されており、連続運転可能な最低負荷運転がコンバインドサイクル出力の15%と低いのが特徴である。
GTCCでは、貯留タンクから供給されたLNGを燃焼器で燃焼させ、高温の燃焼ガスでガスタービンを回転させることにより発電を行う。さらに高温排ガスを排熱回収ボイラに導き、得られた蒸気で蒸気タービンも回転させて高効率発電を行う。
通常の石炭火力発電などに比べて起動・停止が短時間で可能であり、高効率で燃料消費が少ないためCO2排出量も少ない。環境負荷低減はガスタービンの低NOx燃焼器と、排熱回収ボイラに設置された排煙脱硝装置により行われる。
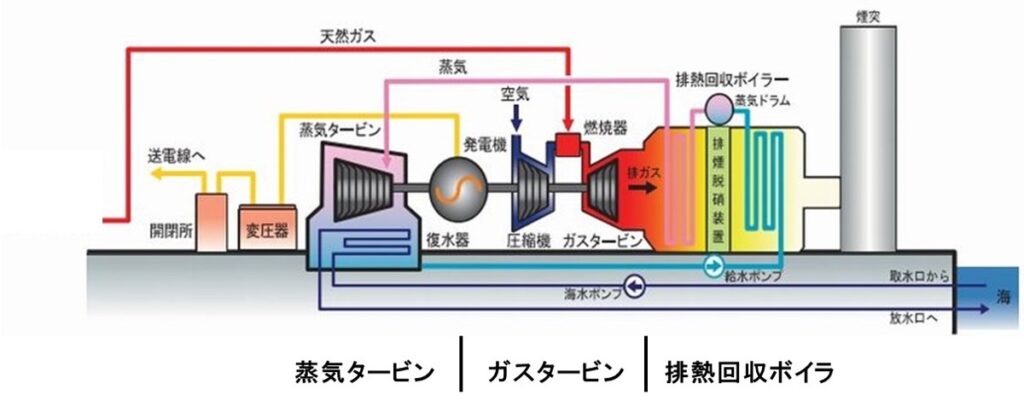
発電用ガスタービンの構造例
図8に、発電用ガスタービンの構造例を示す。吸気プレナムから吸引された空気は圧縮機で圧縮され、燃焼器内で燃料と混合後に着火し、急激に体積膨張した燃焼ガスが、静翼を通して動翼に吹き付けられてロータを回転させる。高温排ガスは排気プレナムを通じて排熱回収ボイラに導かれる。
圧縮空気は燃焼用の他に高温部品の冷却用として使われる。圧縮機での圧力比は空気流量当たりの出力が最大となるよう設計され、最近は燃焼温度の高温化や出力上昇により高くなる傾向を示し、最新の1600℃級ガスタービンでは圧力比が20~25程度に達している。
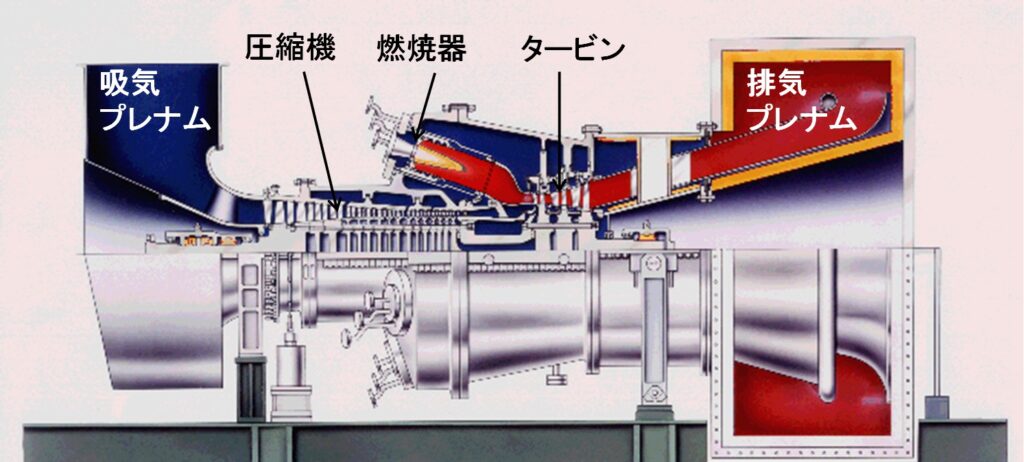
発電用蒸気タービンの構造例
図9に、GTCC用蒸気タービン(混圧タービン)の構造例を示す。排熱回収ボイラから高圧と中圧の蒸気供給を受け、中圧段から低圧段にはクロスオーバー管を通じて蒸気が供給される。各段落には圧力の異なる蒸気が供給され、静翼を通してロータに植えつけられた動翼に吹き付けられて回転力を得る。
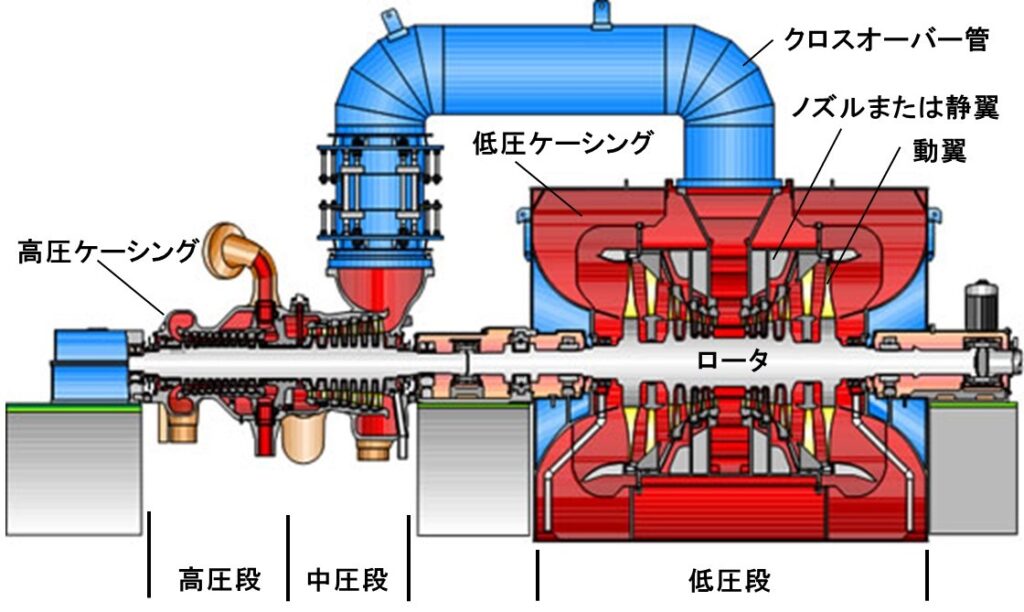
蒸気タービンのロータは発電機ロータに直結されており、発電機のコイルの中でロータに設置された磁石を回転させることで、電磁誘導現象により回転運動を電気に変換する。
複合発電の高温・高効率化
地球温暖化問題がクローズアップされる中で、急速なガスタービンの高温化による高効率化が進められ、電力会社によるLNG焚ガスタービン・コンバインドサイクル発電システム(GTCC:Gas Turbine Combined Cycle)の導入が始まった。
『LNG焚ガスタービン・コンバインドサイクル発電システムの導入』
●1980年代中頃、1100℃級GTCC、発電端効率・LHV基準で47~49%の導入が開始
●1990年代後半、ガスタービン入口の燃焼ガス温度を高温化した1300℃級改良型コンバインドサイクル(ACC:Advanced Combined Cycle)、発電端効率・LHV基準で54~56%の導入が加速
●2000年代後半、燃焼ガス温度をさらに高温化し、ガスタービン高温部品の蒸気冷却などの技術革新で、大容量の1500℃級コンバインドサイクル(MACC:More Advanced Combined Cycle)、発電端効率・LHV基準で58~59%が開発
●2010年代から、燃焼ガス温度をさらに高温化し、ガスタービン高温部品を空気冷却に戻し、高効率の1600℃級コンバインドサイクル(MACC2)、発電端効率・LHV基準で61~62%の導入が加速
現在は、CO2排出量と燃料費の削減を目指し、初期に導入された1100℃級ガスタービンを最新の高性能ガスタービンに置き換えるリプレース工事が始まっている。
2024年8月、東芝エネルギーシステムズ、東芝プラントシステムは、JERA、ENEOS Power、九州電力が共同出資する「五井ユナイテッドジェネレーション合同会社」から、五井火力発電所の更新工事を進めており、1号機の営業運転が開始されたと発表した。2024年11月に2号機、2025年3月に3号機の営業運転を開始する。
液化天然ガス(LNG)を燃料とする出力合計:234万kW(78万kW×3基)のガスタービン・コンバインドサイクル方式火力発電所で、GEベルノバ社製の最新鋭ガスタービンと東芝エネルギーシステムズ製の高効率蒸気タービンおよび発電機を組み合わせ、発電効率:約64%(低位発熱量基準)である。
発電用ガスタービン材料の高温化
発電用ガスタービンの主要な高温部品は動翼、静翼、燃焼器であり、冷却技術、構造材料、構造材料の表面に施されたコーティング技術が高温化に大きな役割を果たした。図10には、ガスタービン高温材料の開発状況と、それに伴うタービン入口温度の上昇を示す。
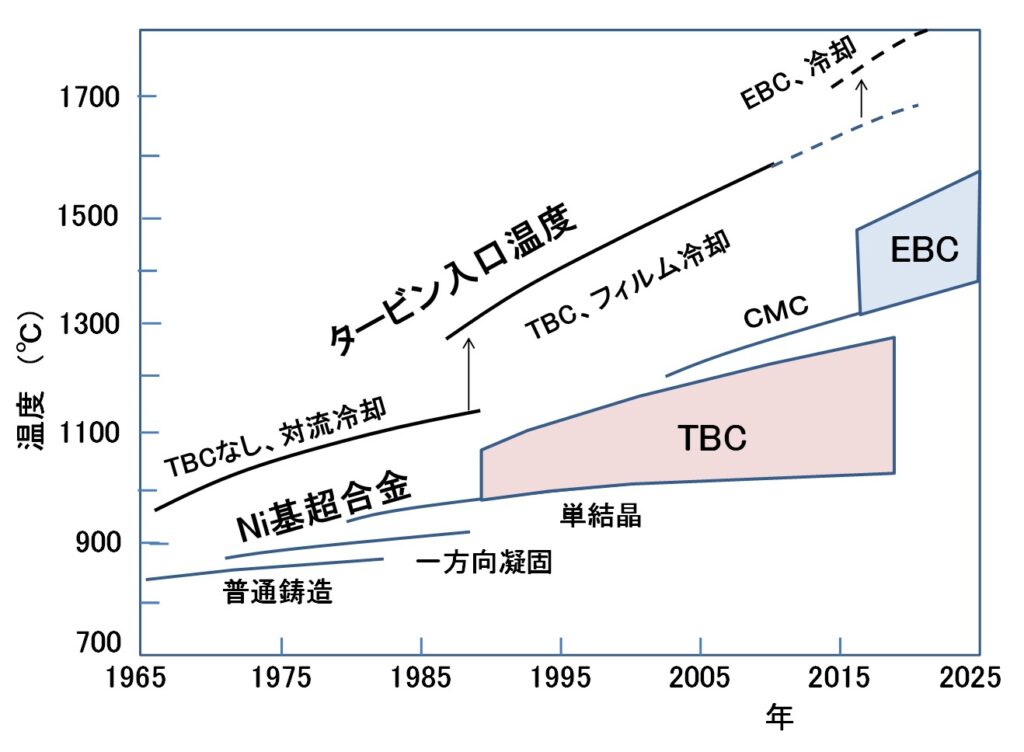
【燃焼器】
キャン型燃焼器はライナと静翼に通じるトランジションピースから構成され、起動停止や負荷変動等による低サイクル熱疲労特性、燃焼振動による高サイクル疲労特性、高温クリープ特性、耐熱衝撃特性が要求される。また、局部加熱に対する耐高温酸化性や補修のための溶接性も必要である。
そのため加工性に優れた薄板のNi基やCo基合金が使われ、その内面には7~8mass%Y2O3-ZrO2のセラミック遮熱コーティング(TBC:Thermal Barrier Coating)が施され、外面は対流冷却が行われている。トランジションピースは内部で燃焼ガスが偏向して増速するため、ライナよりも高温となる。
【静翼】
静翼はケーシング内面に固定された状態で、動翼よりも高温の燃焼ガスに曝されるため高い熱応力が発生する。そのため、要求されるクリープ強度は動翼よりも低いが、曲げ応力に耐えうるクリープ強度、熱疲労特性が必要とされる。
また、製造・保守性の観点から、溶接性・補修性に優れたCo基合金が使われている。その外面にはTBCが施されており、翼に形成された複雑な冷却孔を通じて圧縮空気により内面の対流冷却、外面のフィルム冷却が行われている。
【動翼】
動翼は高速回転により高い遠心力が作用して高温の燃焼ガスに曝され、破損した場合のリスクが高いため、優れた高温クリープ特性、熱疲労特性、熱衝撃特性が求められる。γ‘相Ni3(Al,Ti)析出強化型の普通鋳造Ni基超合金(CC:Conventional Casting)であるRene 80、IN738LCなどが使われてきた。
その後、動翼長手方向に直角な結晶粒界をなくした一方向凝固(DS:Directional Solidification)化によるMar-M200Hf、MS5002などで約20℃、弱化要因である結晶粒界を完全に排除した単結晶(SC:Single Crystal)化によるTMS196、CMSX-4、Rene N5で約30℃の耐熱温度の向上が進められた。
いずれも、動翼外面にはTBC、冷却孔内面にはアルミナイズ処理が施されており、翼に形成された複雑な冷却孔を通じて圧縮空気により内面の対流冷却、外面のフィルム冷却などが行われている。
現在の単結晶Ni基超合金の耐熱温度は、約1100℃(強度設計上は安全をみて1000℃程度)でほぼ飽和傾向にある。そのため、TBCの厚肉化(0.3mm→1.0mm超)と冷却技術の高度化により、タービン入口温度の上昇に対応している。
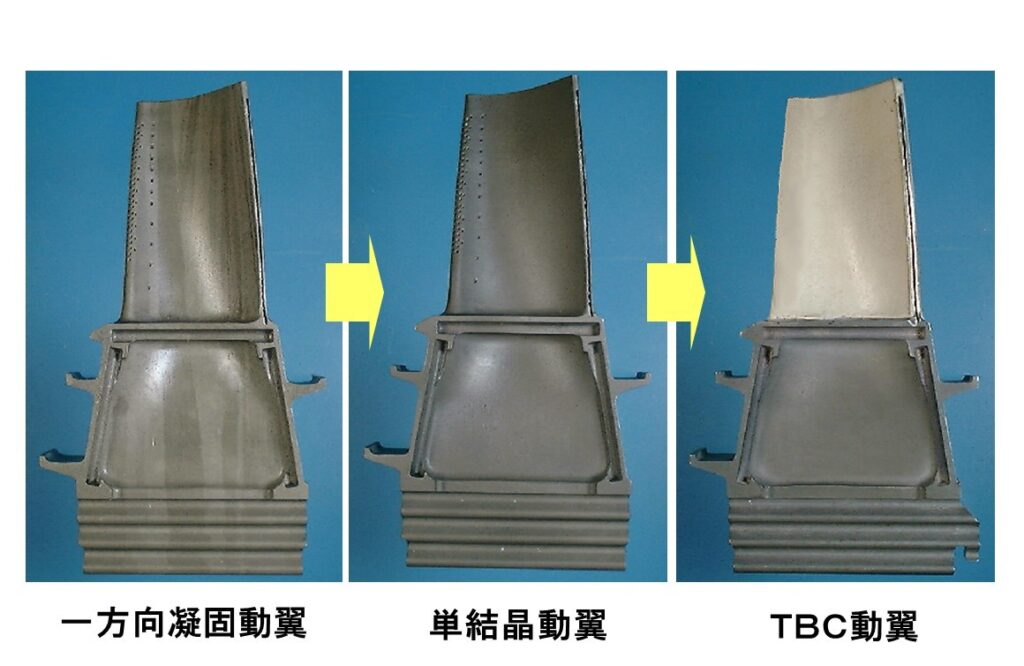
【セラミックス基複合材料】
次世代耐熱材料として期待されているセラミック基複合材料(CMC:Ceramic Matrix Composite)は、2000年初期に炭化ケイ素長繊維強化炭化ケイ素基複合材料(SiC/SiC composite、以下ではSiC/SiC複合材料)の基礎開発が終了している。
第一世代のSiC/SiC複合材料の耐熱温度は約1300℃であり、Ni基超合金(SC)に比べて約200℃と飛躍的な向上を実現し、2016年から航空機ジェットエンジンの高温部品への適用が始まっている。発電用ガスタービンへの適用は、今後の課題である。
SiC/SiC複合材料には、燃焼ガス雰囲気において高温水蒸気腐食の問題が生じる。そのため、これを回避するための耐環境コーティング(EBC:Environmental Barrier Coating)が施されている。
ガスエンジン発電とは
再生可能エネルギーの導入拡大に対し、電力貯蔵システムと系統連系による需給調整が十分に行えない現状において、電力の需給調整には火力発電が大きな役割を担っている。
従来、自家発電や非常用電源などの分散型発電システムとして使われてきた大型ガスエンジンが、その優れた起動性と部分負荷運転でも高い発電効率を維持することから、電力の需給調整を目的とした導入が行われている。しかし、脱炭素社会への過渡的ステップであることを忘れてはならない。
大型ガスエンジンの仕組み
ガスタービン、ガスエンジン、ディーゼルエンジンは、いずれも内燃機関であり、その作動原理も、吸気・圧縮・燃焼(膨張)・排気という同じサイクルで作動する。しかし、その基本的運動はレシプロエンジンの往復運動に対して、ガスタービンは回転運動という大きな相違点がある。
ガスエンジンは、シリンダー内部で燃料の爆発(膨張)を発生させ、その圧力でピストンを往復動させ、その往復動を回転エネルギーに変える。この基本動作は自動車のガソリンエンジンと同じであるが、供給される燃料は天然ガスや都市ガスなど気体である点が異なる。

川崎重工業は、出力:5000~7800kW、発電効率49~51%の大型ガスエンジンをラインアップしている。2011年の初受注以降、180台以上の販売実績がある従来機をベースに、さらなる性能向上を図った最上位機種「KG-18-T」を、2020年6月に開発している。
「KG-18-T」の出力は7800kW(50Hz)、7500kW(60Hz)で、新開発した2段過給システムの搭載により発電効率は51%と高く、NOx排出量は200ppm以下(O2=0%換算)に抑えている。
また、起動指令後5分で最大出力に到達可能な優れた起動性を有し、部分負荷(20~100%)運転においても高い発電効率を維持し、電力網の需給調整力の向上に有効であるとしている。

そのほか大型ガスエンジンは、三菱重工業が「MACHガスエンジン」で出力:3650~5750kWをラインアップしており、希薄燃焼でNOx排出量100ppm以下(O2=0%換算)を達成している。また、IHIは「ニイガタ ガスエンジンAG・AGSシリーズ」で出力:2000~6000kWをラインアップしている。
ガスエンジン発電の導入状況
海外のガスエンジン発電
再生可能エネルギー導入が進むドイツにおいて、電力需要がピークとなる2017年1月中の電力需要と褐炭、石炭、ガス火力の発電状況を図4に示す。電力需要(赤線)と供給(風力+太陽光発電)の差を埋めるために、褐炭、石炭、ガス火力の発電電力量は大きく変動していることが分かる。
最も低コストの褐炭火力がベースロードとなっているが低負荷時には部分負荷運転し、石炭火力は日間起動停止(DSS)と週末起動停止(WSS)、ガスエンジン(コジェネを除く)は短い周期でオンオフ運転を行い、それぞれの特性に合わせて柔軟性を発揮している。
ここで注目されるのは各火力発電の使い分けである。特に、ガスエンジンを短い周期でオンオフ運転し、再生可能エネルギーの細かい出力変動に柔軟に対応している点である。

出典:VGB ” Showcase Germany”, APPFベルリン会合資料
米国では2010年代後半にガスエンジンの導入が急拡大し、テキサス州、カンザス州、カリフォルニア州など、再生可能エネルギーの導入が進む地域に集中的に設置された。
EIA(米国エネルギー情報局)によると、レシプロエンジン発電所の規模は出力:0.5万kW未満が一般的であったが、2010年代後半には平均1.2万kWと大型化し、20万kWを超える発電所もある。
国内のガスエンジン発電
2023年4月、東京ガスは合計30万kWのガスエンジン発電所の新設・取得に踏み出したことが公表された。30万kWは東京ガスが保有する火力発電所の約1割に相当する。
東京ガスは、天然ガス焚のガスエンジン発電所(出力:約10万kW)を千葉県袖ケ浦市の発電所跡地に新設し、2024年度中の稼働を予定している。舶用・エネルギー機器大手、フィンランドのバルチラのガスエンジン(出力:1万kW)を10台程度購入する計画である。
また、日本テクノの茂原パワーステーション(出力:約11万kW)と椎の森パワーステーション(約9万kW)を2022年に買収して運用を開始した。川崎重工業製ガスエンジンの既設発電所であり、上記の新設分と合わせて約30万kWのガスエンジン発電所を保有することになる。
そのほか国内で、日本テクノは川崎重工業製ガスエンジン(出力:7800kW)を14基連ねた11万kWの発電所を千葉県袖ケ浦市、新潟県上越市、茨城県那珂市の3カ所に所有する。沖縄電力は、沖縄本島にガスエンジン発電所を建設中で、北海道ガス、静岡ガス、英国シェルの子会社も導入している。
需給調整に優れたガスエンジン
100%負荷時の発電効率を比較すると、ガスタービン・コンバインドサイクルが52~57%と高く、ガスエンジン(レシプロエンジン)が45~47%、ガスタービン単体が35~39%である。発電効率のみを考えると、国内大手電力会社が導入を進めたガスタービン・コンバインドサイクル発電が優れている。
一方、火力発電所の需給調整力を比較するには、表2の①ホット起動時間、②最小負荷、③50%負荷時効率、④出力変化率(ランプレート)、⑤コールド起動時間が参考となる。①と⑤は短い方、②は低い方、③は高い方、④は速い方が需給調整の柔軟性が高いといえる。
ガスエンジンの特性:
■①ホット起動時間と⑤コールド起動時間が短いため、ガスエンジンは起動から定格運転到達までの時間が短く、起動に要する費用も安い。また、完全停止後のコールド起動時間も圧倒的に短い。
■②最小負荷が低く、③50%負荷時効率が低下しないため、低負荷運転が可能で出力調整幅が大きい。ガスエンジンを数台導入することで、数%の低負荷から定格負荷までの高速調整ができる。
■ガスエンジンの④出力変化率(ランプレート)は100%超と圧倒的に高く、1分以内に最小負荷から定格負荷まで高速調整ができる。すなわち、再エネの短時間変動への追従性が極めて高い。

ガスエンジン発電所の課題
国内では、一般に石炭火力発電所はベースロードとして発電運転を行い、再生可能エネルギーによる大きな変動はガスタービン・コンバインドサイクル発電により対応し、今後、短時間での変動はガスエンジンで対応して需給調整を行うことが考えられる。
しかし、ガスエンジンの抱える大きな課題で注目されているのはメタンスリップである。天然ガス燃料の主成分であるメタン(CH4)が燃え残り、大気中に放出される問題で、CH4の地球温暖化係数(GWP100)はCO2の28倍と高く、わずかな量でも環境上大きな問題となる。
日立造船、商船三井、ヤンマーパワーテクノロジーは、NEDO支援を受けて2021年度から2026年度までの6年間でメタン酸化触媒とエンジンの改良を組み合わせてLNG燃料船のメタンスリップ削減率70%以上の実現を目指している。開発された技術は、ガスエンジン発電所にも適用可能であろう。
しかし、ガスエンジンの燃料として化石燃料(天然ガス、都市ガス)を使うかぎり、CO2排出をゼロとすることはできない。2022年3月、川崎重工業は大型ガスエンジン(出力:5000kW)で水素を体積比30%まで天然ガスと混焼する技術を開発し、水素専焼やアンモニア利用の研究開発も進めている。
また、三菱重工エンジン&ターボチャージャも水素ガスエンジンの実用化開発を進めている。燃料多様化への対応力はレシプロエンジン(ガスエンジン、ディーゼルエンジン)の方が優れており、水素ガスタービンよりも早く実用化される可能性がある。
再生可能エネルギーの導入拡大を実現するためには、太陽光・風力発電の出力変動対策は不可欠である。その需給調整には電力貯蔵システム、系統連系強化、グリーン燃料による火力発電が選択肢としてあげられる。いずれも経済性と実現時期が実現の可否を決めることになる。