航空機の燃料消費低減のために軽量化は重要課題であり、機体やエンジン部品(ファン、ファンケース)への軽量合金や炭素繊維強化プラスチックス(CFRP:Carbon Fiber Reinforced Plastics)の適用のための開発が、継続的に進められている。
ジェットエンジンでは、圧縮機の高圧力比化・高温化やタービン入口温度の高温化に向け、耐熱材料開発、冷却技術開発、空力設計技術の開発が行われてきた。最近では、燃焼器やタービンなど高温部へのセラミックス基複合材料(CMC:Ceramics Matrix Composite)の適用が進められている。
機体構造材料の軽量化
航空機における燃費の向上や航続距離の延伸のために、機体構造材料の軽量化は必須であり継続的に開発が進められてきた。図1には、各種構造材料について比強度(強度σf/密度ρ)と比弾性(弾性率E/密度ρ)の関係を示す。比強度と比弾性が大きい材料ほど、機体の軽量化には有効である。
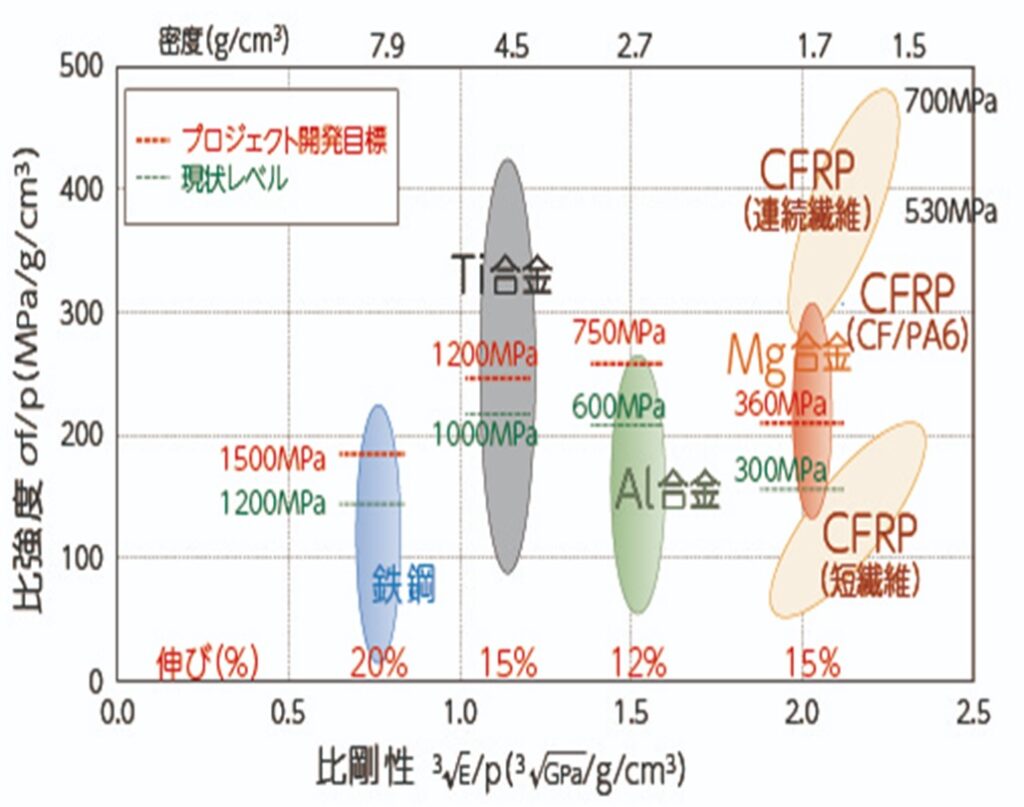
出典:新構造材料技術研究組合(ISMA)
機体構造材料の変遷
軽量化に向けて、航空機の機体構造材料は以下のような変遷をたどっている。
●1930年代、布・木・鋼に替えて、アルミニウム合金が航空機の機体材料として使用され始めた。その後、アルミニウム合金の高強度化が進められ、機体材料の主流となり適用範囲が拡大される。
●1940年代、比弾性に優れたマグネシウム合金の開発が始まり、2010年代に座席など内装品への適用が認可された。しかし、現時点でアルミニウム合金の代替には至っていない。
●1940年代後半、高強度アルミニウム合金(ジュラルミンなど)の代用としてフラップ、舵構造材などの2次構造材にガラス繊維強化プラスチック(GFRP:Glass Fiber Reinforced Plastics)が採用された。しかし、GFRPはアルミニウム合金と比べて比強度は高いが比弾性は劣るため、1次構造材への採用には至っていない。
●1950年代、チタン合金(主にTi-6Al-4V合金)の使用検討が開始された。
●1960 年代後半、アルミニウム合金よりも圧倒的に比強度と比弾性が高い各種の先進複合材料(Advanced Composites)の開発が進み、炭素繊維強化プラスチック(CFRP:Carbon Fiber Reinforced Plastics)の航空機構造材料への採用検討が開始された。
●1980年代に入ると、CFRPは航空機の2次構造材である主翼と尾翼のラダー(方向舵)や客室桁材などに採用された。
●1980年代後半、大型の1次構造材である垂直・水平尾翼安定板や胴体へのCFRPの採用が進められた。CFRPー金属材料継手では、腐食電位差により金属材料側にガルバニック腐食が生じるため、CFRPを多用する機体ではガルバニック腐食を生じにくいチタン合金が多用されている。
ただし、高価なチタン合金は大負荷が作用する主脚、エンジンを支えるパイロン、垂直尾翼、補助動力装置(APU:Auxiliary Power Unit)取付部、尾翼を支える下部構造などに限定される。
材料メーカーの動向
2022年3月、国際航空運送協会(IATA)は2024年の世界の航空旅客数が40億人とコロナ前の2019年を3%上回ると予測している。
新型コロナの感染拡大で、2021年の国内線・国際線を合計した旅客数は2019年比で47%に留まったが、2022年には83%に、2023年には94%にまで回復し、2024年には103%に、2025年には111%に増加すると予測している。
今後も航空業界では難局が続くと考えられているが、2022年6月に入り、新型コロナ禍で低迷した航空機部材メーカーの生産回復が進められている。ウクライナ危機による燃料高騰や環境規制の強化により、航空機軽量部材の需要は強まっている。
東レは、新型コロナ感染拡大の影響で2020年夏に停止した米国サウスカロライナ州の炭素繊維の主力工場で、2022年内に航空機向けの出荷を再開する方針を示した。原糸製造からCFRP加工まで一貫生産を担う中核拠点で、ボーイングの中型機B787の主翼や胴体などに使われる予定である。
帝人は、航空機向けの炭素繊維とCFRP部材の生産について、日本とドイツの工場で稼働率を高め、2022年3月期比で2023年3月期には2割の増産、2024年3月期には4割の増産計画を表明している。
東邦亜鉛は、航空機の降着装置(ランディングギア)やエンジン部品の耐久性を高める電解鉄(世界シェア7割)の増産を表明している。2023年3月期には生産を前期比2割増と新型コロナ感染拡大前の水準に戻す。2024年3月期には自動車向けの出荷も増して同7割増にする。
国際民間航空機関(ICAO)は2021年、航空各社がCO2排出を2019年より増やさないとのルールを導入した。現在は各国の自主的な対応となっているが、2027年には義務化する方針である。環境規制が強まれば、金属の代わりに軽量高強度のCFRP需要が増える。
航空機の機体材料
米国ボーイングの中型ワイドボディ機B787では機体材料に占めるアルミニウム合金の重量比が20%に減少し、複合材料(CFRP、GFRPなど)の重量比が50%に高まった。欧州エアバスの中型ワイドボディ機A350XWB機ではアルミニウム合金の重量比が21%に減少し、CFRPの重量比53%に高まった。
ボーイング787
米国ボーイングの747、767、777では機体材料の70~80%を占めていたアルミニウム合金の使用比率が、最新のB787(Boeing 787 Dreamliner)では20%に減少し、複合材料(CFRP、GFRPなど)の使用比率が50%にまで高まった。
炭素繊維は同じ強度で比較すると重量は鋼の1/4程度で済み、ボーイング787はCFRPを多く使うことで、従来機より燃費性能が2割向上した。
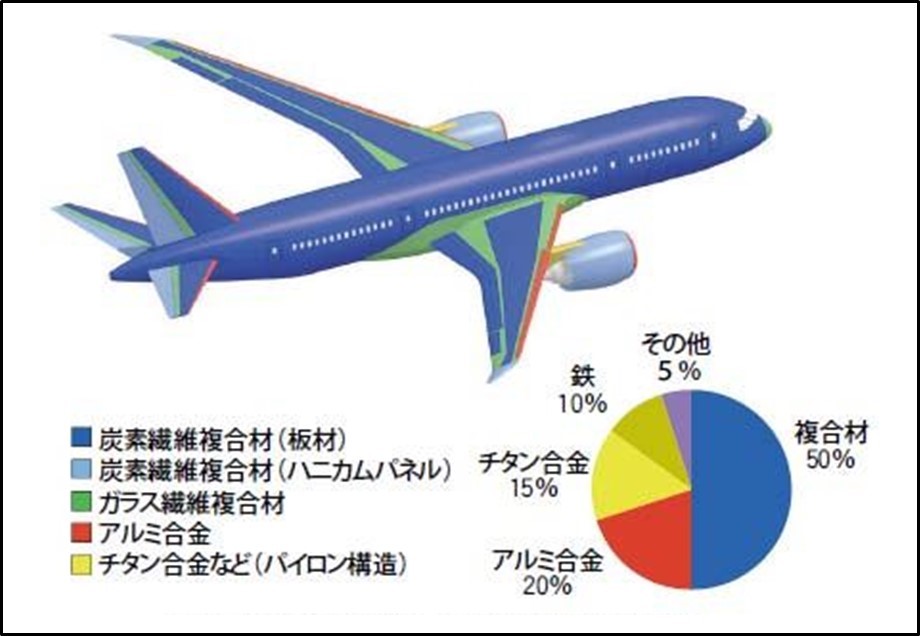
出典:炭素繊維協会
2011年から就航した長距離用中型のワイドボディ機B787(全幅:60m、全長:57m、全高:17m)には、Trent1000もしくはGEnxエンジンが搭載されており、図2のように機体へのCFRP適用が重量比で50%に達している。
機体材料の重量比20%を占めるアルミニウム合金は、新たにアルミニウム・リチウム合金(Al-Li合金、2098-T8)の板材が適用されている。機体材料の15%を占めるチタン合金については、主要部品である主脚(ランディングギア)にTi-5Al-5Mo-5V-3Cr 合金が用いられている
2023年に就航予定の大型旅客機であるボーイング777X(全長:69.79m(777-8機)、76.72m(777-9機))には、GE9X エンジンが搭載されており、CFRP製の主翼が採用されている。
この主翼は折りたたみ式のウィングチップが採用され、駐機時は折りたたみ(翼幅:64.82m)、飛行時には7m長くなるよう展開(71.75m)し、大きな揚力を発生させ燃費効率を最大化している。
また、アルミニウム合金には、銀(Ag)が添加された2029-T8 クラッド材やAl-Li 合金(2098-T84) 板材および2055-T84 押出材などが適用されている。
エアバス380
欧州エアバスでも複合材料(CFRP、GFRPなど)の使用比率は増加する傾向にあり、エアバス320で15%、A380では 22%と増加し、最新のワイドボディ機A350XWB(Airbus A350 eXtra Wide Body))では、図3に示すように53%に達している。
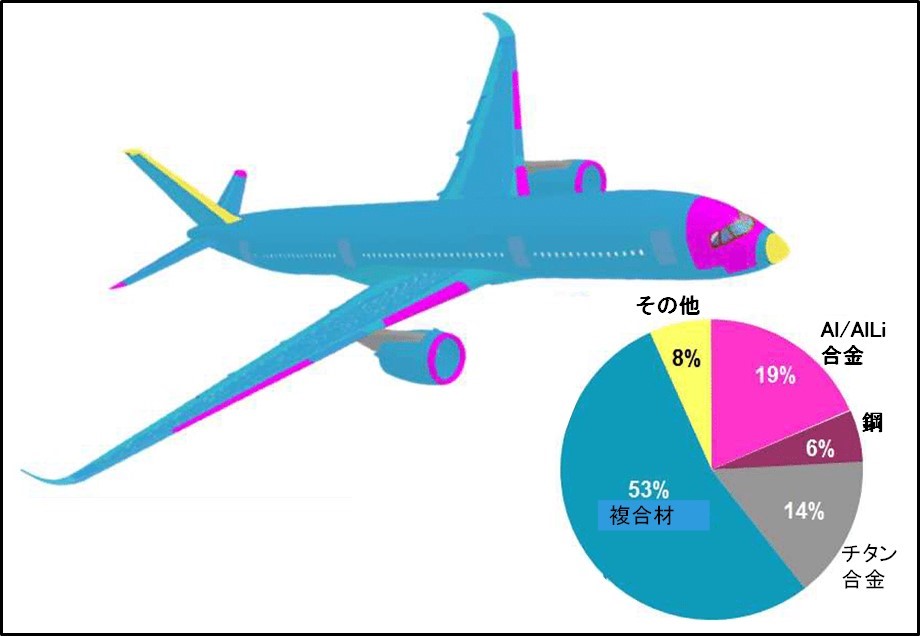
出典: Science China Technological Sciences
60-9,(2017)、1301-1317.
2007年就航の超大型ワイドボディ機のエアバス380(全長:72.7 m、全幅:79.8 m、全高:24.1 m)には、エンジン・アライアンス GP7200もしくはロールス・ロイス Trent900エンジンが搭載され、中央翼、水平・垂直尾翼など1次構造部材へのCFRP適用が30トンを超え、重量比で22%に達した。
重量比で61%のアルミニウム合金は、主翼桁材に7040-T7651合金、リブ材に7449-T7651合金、主翼下面ストリンガにZr添加2027-T3511合金、主翼上面外板材に7056-T7951合金が使用された。
また、Al-Li合金はメインデッキ、クロスビーム、床、ストリンガに2099-T83、2196-T8511押出材、主翼の桁やリブなどの内部構造に、2050-T84 厚板が採用された。しかし、2019年2月、販売不振によりA380機は、2021年以降の生産打ち切りが発表された。
2015年に就航した中型ワイドボディ機のA350XWB(全長:66.8m(350XWB-900)、73.79m(350XWB-1000)、全幅:64.75m、全高:17.5(350XWB-900)、17.8m(350XWB-1000))には、ロールス・ロイス製Trent XWBエンジンが搭載された。
重量比で53%にCFRPは主翼、中央翼とキールビーム、テールコーン、スキンパネル、フレーム、ストリンガー、ダブラーなどに採用されている。重量比で21%を占めるアルミニウム合金は、バードストライク対策のため衝撃に弱いCFRP に代わり、コックピット周辺や主翼の前縁などに用いられている。
また、Al-Li 合金は、2198-T851 板材の成形品、主翼ボックスのリブなどに2050-T84 厚板、中央ビームに2050-T852 鍛造材が使用されている。重量比で14%を占めるチタン合金は、高荷重フレーム、ドア周辺、ランディングギア、パイロに用いられている。
ターボファンエンジンへの複合材料の適用
民間航空機用エンジンでは、1950年代に初めてターボジェット・エンジンが搭載されて以来、性能向上および効率改善が進められ、エンジン形式が低バイパス比ターボファン・エンジンから高バイパス比ターボファン・エンジン、さらには高性能高バイパス比ターボファン・エンジンへと進化してきた。
炭素繊維強化プラスチックス(CFRP)
現在、主流のターボファン・エンジンはターボジェット・エンジンにファンブレードを組み合わせた構造で、大口径ファンブレードにより高バイパス比化し、単位推力当たりの燃料消費量を低減している。しかし、ファンの大口径化は重量増加をもたらすため、ファン部品の軽量化が進められている。
実際に、図4に示すファンブレード、ファンケース、ストラクチャルガイドベーン(SGV:Structural Guide Vane)を対象に、従来材料であるチタン合金やアルミニウム合金から、CFRPへの代替による軽量化が、次のように進められている。

出典: Rolls-Royce HP.
●1970 年代から、ファンブレードのCFRP化が進められてきたが、鳥衝撃(Bird Strike)による破損問題が露呈し、高靱化エポキシ樹脂の採用により靱性を改善したCFRPが開発された。
●1990年代には、米国GEがボーイング777機用エンジン「GE90」向けに、CFRPファンブレードの実用化を行った。
●2010年代には、米国GEがボーイング787機用エンジン「GEnx」向けに、CFRPファンブレードに加えて、CFRPファンケースの実用化に成功した。
●2010年代後半には、CFMインターナショナル(GEとSNECMAの合弁会社)が次世代単通路機であるエアバス320neo機とボーイング737MAX機用エンジン「LeapXエンジン」向けに、3 次元構造織物と自動ワインディング・プレス成形法を組み合わせたCFRPファンブレード・CFRPファンケースを実用化した。
また、インターナショナル・エアロ・エンジンズ(IAE: Pratt & Whitney、ロールス・ロイス、日本航空機エンジン協会、MTUエアロ・エンジンズの合弁会社)は、「PW1100G-JM 」エンジン向けに、自動ワインディング成形によるCFRPファンケースと自動積層・プレス成形法を用いたCFRPストラクチャルガイドベーンを実用化した。
セラミックス基複合材料(CMC)
一般にターボジェットエンジンは、アニュラー型燃焼器で燃焼した高温排気でタービンを駆動させると共に、後部ノズルから噴出させて推進力としている。タービンの主要な高温部品は燃焼器、動翼、静翼であり、冷却技術、構造材料、材料表面のコーティング技術が高温化に大きな役割を果たしている。
- 燃焼器には加工性に優れた薄板のニッケルi基やコバルト基合金が使われており、その内面にはジルコニアセラミックスの遮熱コーティング(TBC:Thermal Barrier Coating)が施され、外面は圧縮空気による対流冷却が行われている。
- 静翼には高温強度と製造・保守性の観点から、溶接性・補修性に優れたコバルト基合金が使われている。その外面にはTBCが施されており、翼内に形成された複雑な冷却孔を通じて圧縮空気により内面の対流冷却、外面のフィルム冷却が行われている。
- 動翼には必要とされる高温強度に応じて普通鋳造のニッケル基超合金(CC:Conventional Casting)、一方向凝固超合金(DS:Directional Solidification)、単結晶超合金(SC:Single Crystal)が開発されている。動翼外面にはTBCが施され、翼内に形成された複雑な冷却孔を通じて圧縮空気により内面の対流冷却、外面のフィルム冷却が行われている。
現在、タービンの主要な高温部品である燃焼器、動翼、静翼を対象に、従来材料であるコバルトやニッケル基合金から、セラミックス基複合材料(CMC:Ceramic Matrix Composite)への代替による軽量化が、次のように始められている。
ただし、SiC/SiC複合材料には燃焼ガス雰囲気において高温水蒸気腐食の問題が生じるため、これを回避する耐環境コーティング(EBC:Environmental Barrier Coating)が施されている。
●2000年初期、炭化ケイ素長繊維強化炭化ケイ素基複合材料(SiC/SiC composite、以下ではSiC/SiC複合材料)の基礎開発が終了した。第一世代のSiC/SiC複合材料の耐熱温度は1300℃であり、ニッケル基の単結晶合金に比べて約200℃と飛躍的な向上を実現した。
●CFMインターナショナル(米国GEとフランスSNECMAの合弁会社)は、LEAPエンジンの表面温度1200℃に曝される高圧タービン・シュラウドにSiC/SiC複合材料を適用した。
●2016年に、エアバス「A320neo」、2017年にボーイング「B737 MAX」と中国商用飛機有限責任公司(COMAC)「C919」のエンジンに、CMCシュラウドが搭載されて運航した。
●2021年8月に、米国GEのアッシュビルのCMC製造工場で、10万台目となるCMCシュラウドの出荷を公表した。
●2020年、GEは最新の航空機エンジン「GE9X」に関してFAAの認証を取得しており、ボーイングの次世代旅客機(B777X)に搭載される計画である。「GE9X」には、5種類の高温部品(高圧タービン第一段シュラウドと静翼、高圧タービン第二段静翼、燃焼器の内・外面ライナー)へのCMC採用を公表している。
2023年3月、東ソーは、アルミナ繊維、ムライト繊維と酸化物系マトリックスを組み合わせたCMC開発を発表した。高温におけるセラミック繊維の結晶粒成長を抑制する元素をドーピングする独自技術を開発し、従来は1000℃程度であった酸化物系CMCの耐熱性を1200℃まで高めた。
2023年10月、「JAXA革新的将来宇宙輸送プログラム」に選定された湘南先端材料研究所のSiC繊維強化Al2O3(CMC)が、JAXAのアーク加熱風洞試験(750kW)で850℃の耐熱性を実証した。
Al2O3マトリックスにホウケイ酸ガラスをベースとした特殊な添加剤を配合してプリプレグを積層し低温焼結するプロセスで、SiC繊維の表面コーティングを施さず、SiC繊維も低価格品を使用する。850℃の曲げ強度も十分高く、比重は3以下と軽量で、面積1m2×板厚2mmの量産コストは100万円以下を達成できる見込み。
2024年2月、三菱ケミカルグループは、高耐熱CMC材料(C/SiC)の開発を発表。ピッチ系炭素繊維を用い、表面に酸素透過バリア層を設けることで、空気中で1500℃×1h保持しても強度が低下しない。
「JAXA革新的将来宇宙輸送システム研究開発プログラム」で参考値として示されている1,600℃で800秒間の条件にも耐えうるものとしている。今後は、2030年代前半に実現をめざしている宇宙輸送システムの往還機熱シールドや宇宙利用・回収プラットフォーム部材への採用を視野にさらなる耐熱性向上をめざす。
2024年4月、東京工科大学セラミックス複合材料研究センター(TUT)は、米国レイセオン・テクノロジー傘下のプラット・アンド・ホイットニー(P&W)と、SiC/SiC複合材料の共同研究を開始した。P&Wが資金を提供し、SiC/SiC複合材料の各温度での基本特性を調べ、得られた特性について理論的な研究が行われる。
2024年8月、東ソーは高耐熱酸化物系CMCの開発を発表した。アルミナ繊維系「TCA-01」とムライト繊維系「TCM-01」で、大気中1200℃、1000時間の熱暴露後でも強度が低下しない。高温での繊維の粒成長を抑制する元素を、均質にドープする新規組織制御技術(UDM)を開発している。
新しい接合技術の適用
航空機構造では、溶接が比較的難しいアルミニウム合金やチタン合金、溶接が不可能なCFRPなどが多用されているため、胴体外板同士の締結や外板と補強部材の締結などにはリベットやボルトによる機械継手が多く採用されているのが現状である。
これら航空機構造の機械継手部や溶接継手部では安全率を高く設定する必要があり、機体の軽量化の障害となっている。そのため摩擦撹拌接合(FSW)や線形摩擦接合(LFW)などの高い信頼性を保持できる新しい接合技術の適用が望まれている。
摩擦撹拌接合(FSW)
摩擦撹拌接合(FSW:Friction Stir Welding)は、1991年に英国TWI(The Welding Institute)によって開発された新しい接合プロセスである。高速回転ツールを接合部に押し当て、摩擦熱を生じさせて軟化した部分を攪拌し、塑性流動を生じさせて固相接合する。
材料を局部的に溶かして接合する従来の溶接技術に比べて、溶接変形や強度劣化などを抑制でき、アルミニウム合金のような難溶接材料でも大気中での接合が可能であるため、鉄道車両への適用に始まり、自動車や航空宇宙機器への適用が急速に広がっている。
欧州ではWAFS(Welding of Airframes using Friction Stir)やTANGO(Technology Application to the Near Term Business Goals and Objectives of the Aerospace Industry)などの国家横断的プロジェクトなどで、航空機構造へのFSW適用が積極的に進められた。
欧州エアバスではリベット接合の代替として、中央翼、主翼、胴体などの 1 次構造部への適用検討が積極的に進められた。A350XWB機の胴体外板の長手方向の接合にFSW適用が検討されたが、設計変更により胴体構造がアルミニウム合金からCFRPに変更され、FSW 適用も立ち消えている。
米国ボーイングでは、宇宙機器であるデルタロケットやスペースシャトルのアルミニウム合金製あるいはアルミニウム-リチウム合金製の燃料タンク製造にFSWを適用している。
航空機の1 次構造部への適用検討は遅れているが、輸送機のアルミニウム合金製床構造部などへの適用が始まっており、B747やB777 Freighterのカーゴバリヤービーム組立にFSWが使用されている。
米国Eclipse Aviationでは、小型ジェット機「Eclipse 500」へのFSW適用を公表している。外板と骨材の重ね接合のリベットを廃してFSWを採用し、大幅なコスト低減を実現した。また、翼部材にもFSWを採用しており、富士重工業が施工している。
三菱重工業は、2005年にH-ⅡB ロケットのアルミニウム合金製の推進薬タンク製造にFSWの適用を公表している。ボビンツールと呼ばれる接合工具を実用化して裏当て金なしの状態でFSWを行い、タンク軸方向接合に加えて円周方向接合を実現している。
川崎重工業は、2012年にリベット結合や抵抗スポット溶接の代替となる摩擦攪拌点接合(FSJ:Friction Spot Joining)技術を開発し、自動車メーカーの生産ラインに導入された。接合部に工具の圧入痕が残るため、航空機の機体接合用に平滑な外観が得られる穴無しFSJ接合ツールを開発している。
現在、アルミニウム合金以外にも、FSWによる金属材料の接合技術開発は難燃性マグネシウム合金、チタン合金、各種鋼材などについても実施されている。
今後、航空機機体へのCFRP適用が増加すると、耐食性の観点からチタン合金の適用増が見込まれている。チタン合金とアルミニウム合金、チタン合金とCFRPなどの異種材料接合について、信頼性の高い接合・接着技術の開発と、継手設計や非破壊検査を含めた総合的な接合技術の開発が重要である。
線形摩擦接合(LFW)
航空機ジェットエンジンでは、動翼(Blade)とディスク(Disk)を一体化したブリスク(Blisk)を、ファンや圧縮機のロータに積極的に採用する事例が、民間機用の航空機エンジン(2008年:GEnx-1B、2014年:PW1100G-JM、2015年:LEAP-1A)で増加している。
このブリスクは、鍛造素材から動翼部を削り出す製造方法が一般的である。しかし、ファン、圧縮機のディスク、動翼には高価なチタン合金が使われることが多いため、コスト低減のために線形摩擦接合(LFW:Linear Friction Welding)が戦闘機用エンジンなどで採用されている。今後、民間機用の航空機エンジンへの適用拡大が想定されている。
このLFWは、接合する材料同士を押し付け、一方を接合面に平行に線形運動で擦りあわせ、接合界面に発生する摩擦熱を利用して、加圧により塑性変形を与えて接合する固相接合法である。
溶融溶接に比べて接合部の組織粗大化や気孔などの欠陥を生じないが、接合界面に融合不良を生じる場合もあることから、非破壊検査による確認は必須である。特に、異種材料間の接合については、接合界面に金属間化合物が形成される場合も想定され、継手強度評価が重要である。
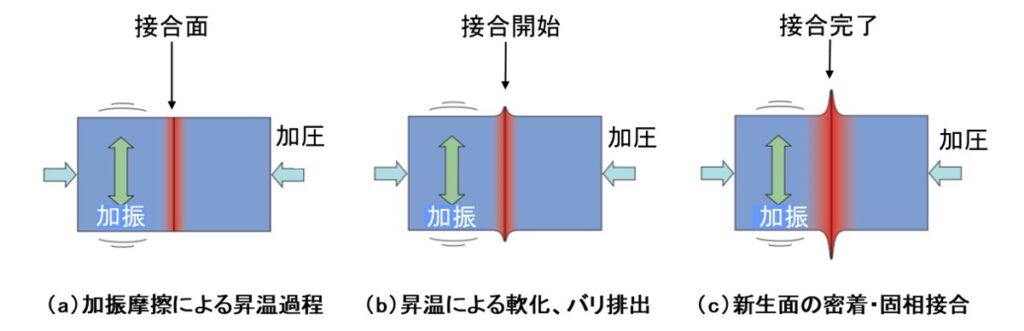
出典: IHI技報
積層造形技術(AM)
最近では、積層造形技術(AM:Additive Manufacturing)の航空機への適用が積極的に進められている。米国ボーイングはB787機にはエアダクト、内装品の小部品、後部ギャレーフィッティングなど25000点のAM部品が採用されている。
また、CFMインターナショナルのLEAPエンジンの燃焼器ノズルにもGEが開発したAM部品が採用されており、高低圧タービン翼やベアリングハウジングなどの試作が行われている。
材料表面へのサメ肌加工
サメ肌を模した微細なリブレット加工が、流体による摩擦抵抗の低減に有効なことは良く知られている。航空機の機体表面へのリブレット加工の実証試験が、航空各社(ルフトハンザ、ANA、JAL)で進められている。1~2%程度の燃費削減が可能な技術で、CO2削減にも有効とされている。
今後のリブレット加工の適用拡大には費用対効果が鍵となる。記録を争う高速水着では、それなりの意味はあったが、経済的に成り立たなければ大面積の航空機の機体での採用は難しい。
バイオミミクリーとは?
バイオミミクリー(生物模模倣)とは、ギリシャ語で「生命」を意味するbiosと「模倣」を意味するmimesisを組み合わせた造語で、生命・自然界における形状・プロセス・生態系から学び、注意深く模倣することで、より持続可能なデザインイノベーションを生み出すことである。
持続可能な社会に向けて、長い年月で進化してきた自然界の叡智に敬意を払い、学ぶことがバイオミミクリーの本質である。
バイオミミクリーが注目を集めた一つに、北京オリンピックに向けて2007年に登場した英国speedoが開発した水着のLZR Racer(レーザー・レーサー)が良く知られている。
サメ肌には、水の抵抗を減らし推進力を高める効果があることが知られており、これを模して高速水着の表面には微細なリブレット加工が施されていた。多くの水泳選手が着用し、次々と世界新記録を出したことは記憶に新しい。2010年4月、高速水着は規制され、実質的な禁止措置が取られたが、、、
サメ肌に関する最近の研究
2018年3月、ハーバード大学とサウスカロライナ大学は共同でサメの皮膚に関する研究を行い、皮膚の微細構造が推進力を高めるメカニズムを解明した。サメの皮膚を電子顕微鏡で見ると、数千もの小さな鱗(うろこ)または小歯状突起で覆われている。
研究チームは小歯状突起をマイクロCTスキャンを使って3次元モデル化し、それを湾曲した翼体の表面に3Dプリントして風洞実験を行った。その結果、小歯状突起形状は薄型の微細な渦発生装置として作用し、翼体の揚力を大きく増加させることを発見した。
一般に、翼体の表面に凹凸を付けると流体による摩擦抵抗は増える。しかし、小歯状突起形状の場合は微細な渦が多数発生して翼体の揚力を大きく増加させることで、摩擦抵抗の増大よりも圧力抵抗の低減の効果が顕著となるのである。最近の新しい知見である。
なるほど、本わさびを擦りおろす時にサメ肌を使うと、きめ細かくクリーミーに仕上がる理由が分かる。空気を多く含ませることで、本わさびの香りとツンとくる刺激が強化されるようだ。
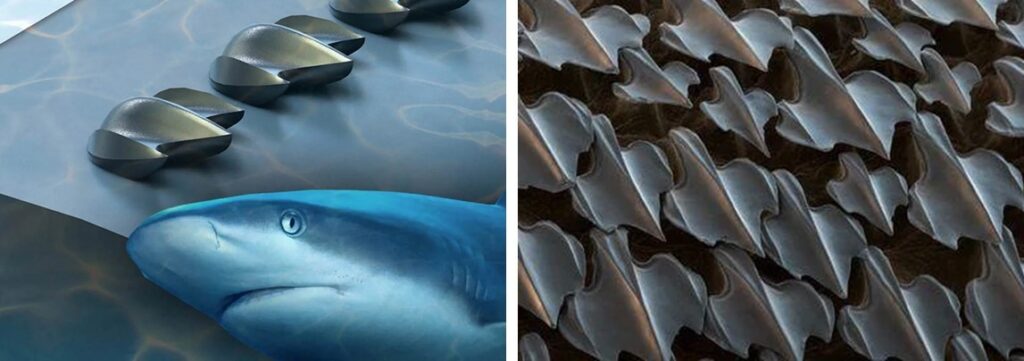
しかし、現時点ではこのサメ肌を直接に翼体の表面に再現するのは経済的に難しい。そのため、高速水着のように微細なリブレット加工(縦溝)を施すことで、様々な機械部品表面の摩擦抵抗の低減が検討されている。
リブレットは摩擦抵抗の低減に有効である。乱流と呼ばれる領域では壁面境界層に強いヘアピン渦が発生し、それに伴う壁面近傍の連続的な縦渦の発生により摩擦抵抗が生じる。リブレット加工を施すと、渦と壁面との間に距離が生じ、接触面積が少なくなることで接触摩擦抵抗を低減する。
リブレット効果を最大化するには、対象部位毎の流体状況(流速・密度・粘性・流れの向き等)に応じて計算流体力学による縦溝構造の設計が重要である。2021年5月、ニコンは、オーストリアのバイオニック・サーフェス・テクノロジーズと、リブレット加工技術の戦略的共同開発契約を締結した。
また、ニコンは、リブレットのレーザー加工の受託サービスを行っており、従来の樹脂フィルムに加えて、樹脂、金属、コーティング・塗膜などにもリブレットを直接付与することが可能である。実際に、ガスタービン圧縮機や超小型ジェットエンジン部品などへの適用検討を進めている。

また、オーウエルは、既存の塗膜上に水溶性の型(モールド)を使ってリブレット(縦溝)を形成する「Paint-to-Paint Method」を開発している。
所定のリブレット形状を写した水溶性モールドに、航空機と同じ塗料を塗工してフィルム化し、航空機の既存の塗膜の上に同フィルムを圧着する。塗膜が硬化した後、水洗いすることで水溶性モールドを除去する手法で、高さ50μmのリブレットを寸法誤差±5%以下で形成できる。
2024年9月、ニコンは、風力発電機の羽根に「リブレット加工」で発電効率を高める実証実験を始めた。摩擦抵抗を抑える効果があり、ユーラスエナジーホールディングスが北海道稚内市に持つ風車の羽根にフィルムを、発電量を1年間かけて比べる。小型風車を使った試験では、発電効率が約3%改善した。
航空機体へのリブレット加工の適用
ルフトハンザ
2021年5月、ルフトハンザグループの子会社Lufthansa Technikとドイツの総合化学メーカーBASFは、サメ肌を模した新フィルム「AeroSHARK」を開発し、ルフトハンザカーゴが2022年より全機に適用すると発表した。機体への新フィルム貼付により、1%程度の燃料削減を見積もっている。
「AeroSHARK」には、リブレットという高さ50μmの微小突起物が何百万個もあり、このフィルムを機体に貼ることで空気抵抗を減らす。ルフトハンザカーゴのボーイング777Fの場合、保有する全10機で約3700トン/年の燃料削減と、1.17万トン/年のCO2排出量の削減が可能である。
2022年3月には、ルフトハンザグループ傘下のスイス航空で機体への「AeroSHARK」の適用を公表している。ボーイング777型機の胴体とエンジン部分の表面に合計950m2のフィルムを貼ることで、約1.1%の燃料削減できるとしている。
スイス航空は2022年半ば以降、順次ボーイング777型機にフィルムを導入する。運航する全てのボーイング777型機で適用が進むと約4800トン/年の燃料削減と、最大1.52万トン/年のCO2排出量の削減が可能である。

全日本空輸(ANA)
2022年10月、ANAはB787型機の特別塗装機「ANAグリーンジェット」を公開した。胴体の一部に燃費改善効果があるニコンの「リブレットフィルム」を国内航空会社として初適用し、2機を使って耐久性を検証する。1機目は羽田―サンフランシスコの定期便、2機目は11月に国内線で運行する。
仮にANA全機の機体表面の約8割にリブレットフィルを装着すれば、約30万トン/年のCO2排出量の削減が見込めると試算している。
2024年8月、ボーイング777型機の貨物専用機(フレイター)と旅客機に、ルフトハンザ テクニックとBASFが共同開発した「AeroSHARK」フィルムを導入する。2024年9月の貨物定期便より、ボーイング777型フレイター(JA771F)が初めて就航し、来春から2号機目の旅客機(JA796A)を国際線にて運航する。
「AeroSHARK」フィルムは、1枚当たり幅約1m×高さ約0.5mで、50㎛程度の微細加工が施されており、機体胴体の大部分にこのフィルムを貼付することで、一機当たり年間約250トンの燃料消費量と約800トンのCO2排出量を削減することができる。2機の運航を通じて、その効果を検証した上で、同型機材への拡大を進める。
日本航空(JAL)
2023年2月、JALは、JAXA、ニコン、オーウエルと共同で、B737-800型機の2機で胴体外板の塗膜上にリブレット加工を施し、2022年7月から国内線で飛行試験(1機は750時間、もう1機は1500時間)を実施した結果、燃費改善効果と実用化に十分な耐久性を確認したと発表した。
1機にはニコンによる塗膜上に直接レーザーでリブレット加工、もう1機にはオーエンによるPaint-to-Paint Methodのリブレット加工を、胴体下部のサービスパネル(機体内部を点検・整備するために開閉できる蓋)上の2箇所(約7.5cm2)に施した。
ピッチに対して高さを半分にすると摩擦低減効果が高くなるため、リブレット加工は高さ50μm、ピッチ100μmとした。JAXAの試算では、リブレット加工を航空機全面に施工すると、約2%の燃費改善が見込める。
今後、737-800型機に対してより大面積のリブレット加工を施した実証機で飛行試験を継続し、その後、国内線の大型機、国際線機材へと順次展開していく計画としている。
しかし、航空機の機体表面80%以上への適用で1~2%程度の燃費削減が可能な技術では、費用対効果が課題となるであろう。より一層の低コストプロセスの開発が急務である。
2025年1月、機体表面に「サメ肌」状の塗装を施した1機を国際線で1月中旬から導入する。機体と空気の摩擦抵抗を従来より0.24%減らし燃費改善をめざす。羽田空港内で凸凹のリブレット形状を施したボーイング中型機「787」を公開し、ロサンゼルス便やフランクフルト便などの中長距離路線に充てる。
宇宙航空研究開発機構(JAXA)や塗料などを扱うオーウエルと共に、翼を含めた機体全体の約20%、機体胴体の約30%にリブレット形状の塗装を施した。約119トン/年の燃料改善、CO2排出量も約381トン減少する。
機体の塗装を除去し、新たにリブレット塗装を施すため、ルフトハンザ航空やANAなどのフィルム貼付法に比べて機体が重くならず、フィルムのはく離も生じない。塗装の耐用年数は8〜10年としている。