水素(H2)と二酸化炭素(CO2)を原料とし、触媒(Ni、Ruなど)を用いて熱化学的にメタンを合成する(メタネーション)技術が開発され、実用化されている。
現在、再生可能エネルギーを使いメタンを合成するメタネーション変換効率は55~60%である。最近、再生可能エネルギーを使いSOFCの逆反応であるSOECメタネーションの開発が進められている。水蒸気とCO2を使って電気分解し、高い変換効率85~90%を達成している。
メタネーション技術の開発
メタネーション技術とは?
1902年、フランスのPaul Sabatier(ポール・サバティエ)により、水素(H2)と二酸化炭素(CO2)を原料とし、高温高圧状態でニッケル(Ni)触媒を用い、熱化学的にメタン(CH4)を合成(メタネーション)する技術が見出された。アルミナ上にルテニウム(Ru)触媒を担持させた高効率触媒も開発されている。
一方、最近では熱化学法以外に、電気化学法、光還元法、バイオ法などの研究開発も行われている
「2050年カーボンニュートラル」に向け、再生可能なクリーンエネルギーに転換していくグリーントランスフォーメーション(GX)が政府により推進される中で、注目を集めているのが「メタネーション技術」である。
再生可能エネルギー水素を原料として得られる合成メタン(e-メタン)を、都市ガスの代替として使う試みで、既存の都市ガスのインフラがそのまま使える。合成メタンの燃焼時に排出されるCO2は、製造時に原料として回収されたCO2であり、循環使用するためにCO2排出量は実質ゼロになる。
2021年6月、メタネーション技術の確立と社会実装に向けた「メタネーション推進官民協議会」が設立され、官民両面での取り組みが加速する。政府は、2030年までに都市ガス導管に注入するガスの1%をカーボンニュートラルメタンとし、2050年までに90%とする目標を掲げた。残り10%は、水素直接利用、バイオガスなど。
現在、再生可能エネルギーなどの余剰電力で水電解により水素(H2)を製造し、別途に回収貯留したCO2と共にメタネーション装置に入れ、高温で触媒反応させることで合成メタン(CH4)を製造する方法が進められており、実用化に向けて量産化と低コスト化が進められている。
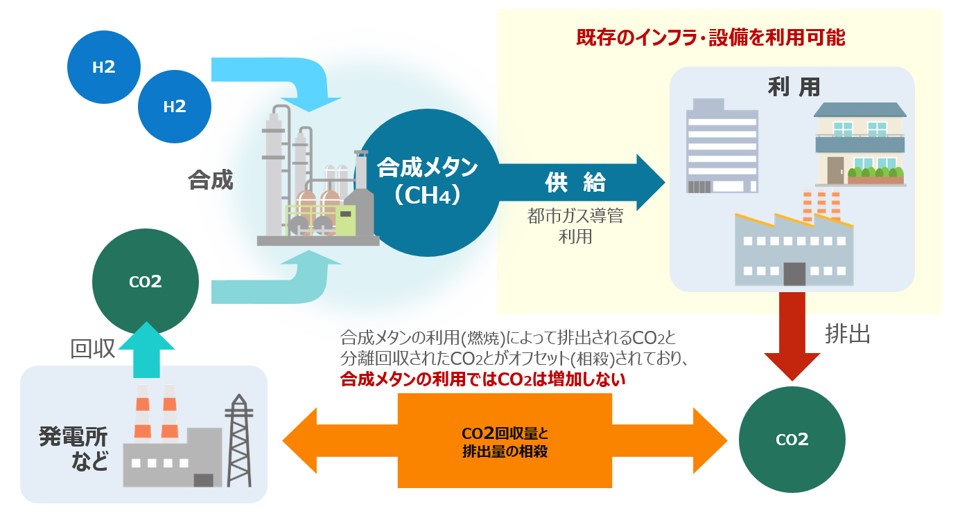
メタネーション装置の開発動向
2019年10月、国際石油開発帝石(現INPEX)と日立造船は、メタネーション試験設備を長岡鉱場の越路原プラント敷地内に完成させた。越路原プラントで天然ガス生産時に付随するCO2と、固体高分子水電解装置(32Nm3/h)により製造された水素から合成メタンを製造する。
日立造船製のプレート型メタネーション反応器は、熱回収効率が87%と高く、運転温度:200℃、運転圧力:0.7MPaであり、生成ガス(メタン濃度:91.2%)をガス精製器を通し、高濃度化(99.6%)が可能である。メタン製造能力は8Nm3/hで、4500h以上の安定製造を確認している。
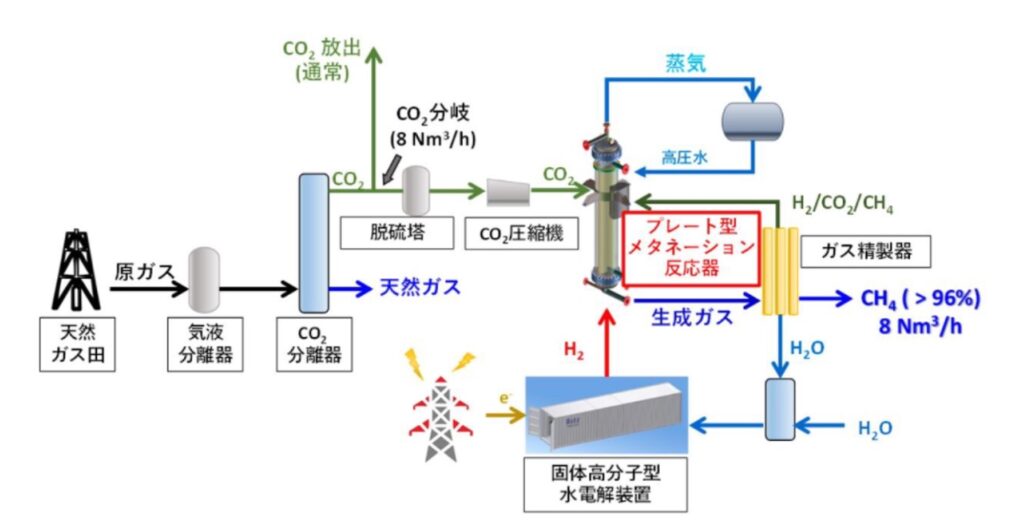
2021年10月、INPEXと大阪ガスは、大規模メタネーション装置(製造能力:約400Nm3/h)の導入のNEDOプロジェクト(~2025年度末)を開始した。INPEX長岡鉱場の越路原プラントからCO2を回収貯留し、メタネーション設備を接続し、製造した合成メタンをINPEXの都市ガスパイプラインへ注入する。
2022年3月、東京ガスは横浜テクノステーションで、メタネーション実証試験を開始。主に太陽光発電の電力で、英国ITM Power製の固体高分子型水電解装置(製造能力:30.9kg/h、圧力:1MPa未満)で水素を製造し、横浜市清掃工場の排ガスから三菱重工業製のCO2分離回収装置で得られたCO2をトレーラーで受け入れる。
日立造船製の多管シェル&チューブ型メタネーション装置(CH4製造能力:12.5Nm3/h)でメタン合成を行う。2020年代中頃に数百Nm3規模に拡大し、2030年にガス販売量の1%に合成メタン導入の目標を掲げている。

2022年6月、日立造船が、小田原市環境事業センターのごみ焼却施設から排出されるCO2を回収貯留し、LPガスの改質水素と反応させるメタネーション実証装置の運転を開始した。排ガスからのCO2分離にはエア・ウォーターの技術を活用しており、合成メタンの製造能力:125N㎥/hである。
2022年8月、日本特殊陶業はメタネーション装置を開発し、2023年4月から小牧工場で実証実験を行うと発表。自社のゼオライト膜でガスエンジン排ガスからCO2を回収貯留し、水電解で得られた水素と反応させて1Nm3/h(0℃、1気圧)の合成メタンを製造して、ガスエンジンの燃料として再利用する。
将来的に、4Nm3/hのメタネーション装置を開発し、2030年に中小規模工場への販売を目指す。製造コストは100円台/Nm3と、現状の1/3程度に引き下げ計画である。
2022年9月、豊田自動織機は高浜工場でメタネーションの実証実験を始めた。ボイラから排出されるCO2を回収貯留し、化石燃料由来のグレー水素と混ぜて合成メタンを製造し、別ボイラの燃料で再利用する。将来的に太陽光発電によるグリーン水素へ切り替え、全工場にメタネーション設備を導入する。
2022年10月、IHIは、合成メタンを製造できる「小型メタネーション装置」の販売を開始した。2019年5月からシンガポール科学技術庁化学工学研究所と共同で触媒開発した技術がベースで、シェル&チューブ型反応器で、合成メタン製造量:12.5Nm3/hで、外形寸法は幅2250×長さ6100×高さ2850mmである。
2024年5月、IHIは、東邦ガス知多e-メタン製造実証施設向けに「メタネーション標準機」を納入した。東邦ガスでは、5Nm³/hで運転する。2030年には大型装置(数千~数万Nm³/h)の商用化も予定している。
2022年、JFEスチールから実証機(500Nm³/h)を受注しており、高炉排ガスからのCO2回収(20トン/日)も含めて2025年の稼働を予定する。吸熱反応のCO2回収と発熱反応のメタネーションを組み合わせ、エネルギー効率を高める。

SOECメタネーションの開発動向
2020年7月、デンソーは、安城製作所のアルミ溶解炉などから出たCO2を回収し、太陽光発電を使って水電解で得た水素を使いSOECメタネーションの実証実験を始めた。合成メタンはガス燃料に使い、CO2を工場内で循環させる。2025年度から社外での実証実験にも取り組み、2030年度の事業化をめざす。
2022年4月、大阪ガスは金属支持型SOECで水素を製造し、回収されたCO2から都市ガスを製造するメタネーション試験設備を大阪市酉島地区に建設すると発表した。
2027年度までに200世帯程度、2030年度までに1万世帯分の都市ガス製造を実現し、設備の大型化などで製造コスト削減を進め、2040年頃の事業化を目指す。2023年8月には、石油元売りのENEOSと共同で大阪湾岸での大規模施設の建設に向けた検討に入った。
2022年4月、大阪ガスは大阪市や大阪広域環境施設組合と、再エネ由来の水素と生ごみを発酵させて製造したバイオガス(メタン約60%とCO2約40%)中のCO2でメタネーションを行い、合成メタンを需要家に供給する。環境省「水素サプライチェーン構築・実証事業」(2022年度~25年度)で行う。
2024年6月、 大阪ガスは、舞洲工場のエネルギー技術研究所内にSOECメタネーションのラボスケール試験装置(製造能力:0.1Nm3/h))を設置し、e-メタンの製造を開始した。SOEC電解装置で再エネ電力で水とCO2を電気分解し、生成した水素や一酸化炭素からメタン合成反応装置の触媒反応でe-メタンを合成する。
外部水素の調達が不要で、高温(約700~800℃)の電気分解により、必要な再エネ電力等を低減し、メタン合成時の排熱の有効利用により、従来のメタネーション(約55~60%)を大幅に上回るエネルギー変換効率約85~90%の実現をめざす。
その後、2025~2027年度にベンチスケール試験(e-メタン製造規模:10Nm3/h級、一般家庭約200戸相当)、2028~2030年度にパイロットスケール試験(400Nm3/h級、約1万戸相当)を進め、2030年度にe-メタン製造技術の確立、実証フェーズを経て、2030年代後半から2040年頃の実用化をめざす。
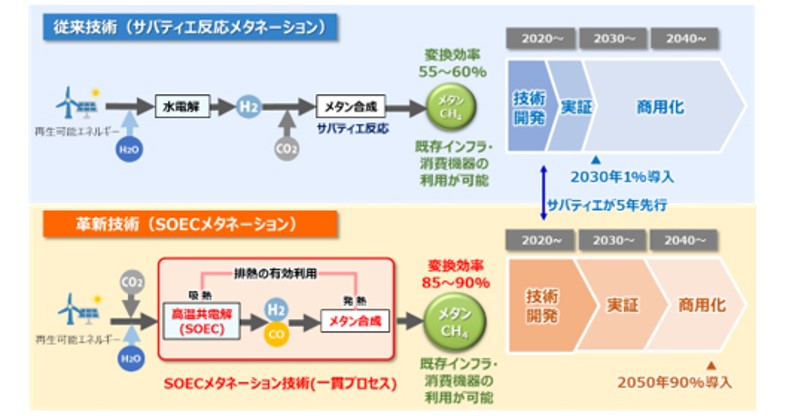
コメント