国内で1970代に始まる燃料電池の研究開発成果は、約30年を経た2009年5月に、世界に先駆けた固体高分子型燃料電池(PEFC)型「エネファーム」の一般発売開始として実を結んだ。
2024 年1月、PEFC型とSOFC型「エネファーム」の累計販売台数が、50万台を突破したと報じられた。一般販売開始後に15年をかけて累積販売台数が50万台を突破したのである。しかし、国内の一般世帯総数4885万世帯(2020年)に対する普及率は1%に留まる。本当に、導入は順調に進んでいるのであろうか?
定置用燃料電池の開発経緯
国内では1970年代から、エネルギーに関する国家プロジェクトの「サンシャイン計画」(1974~1992年)や「ムーンライト計画」(1978~1992年)、「ニューサンシャイン計画」(1993~2002年)が実施され、太陽光発電、風力発電、燃料電池など様々なエネルギーシステムの開発が進められた。
燃料電池に関して国内では、1990年代にリン酸型燃料電池(PAFC:Phosphoric Acid Fuel Cell)の中規模産業用オンサイト発電装置(出力:100~200kW、発電効率:40%)を、富士電機と東芝が商品化した。しかし、ガスエンジンやディーゼルエンジンに比べて高価なため、政府補助金が消滅すると共に大幅縮小した。
1991年には、東京電力五井火力発電所内に設置された大規模リン酸型燃料電池プラント(出力:1.1万kW、東芝製〉が定格運転に成功した。しかし、実証運転段階で故障が相次ぎ撤退したこともあり、以後、国内では大規模燃料電池プラントの商用化は検討されていない。
2000年代に入ると、燃料電池自動車の公道上での実証運転が始まり、2002年10月には本田技研工業が「FCX」、同年12月にはトヨタ自動車が「FCHV」を、国内と米国でリース販売を開始。
一方、定置用燃料電池は、2005年に家庭用燃料電池「エネファーム」の大規模実証が始まり、実証機が首相官邸や全国各地の住宅に導入されデータ収集が行われ、2009年5月、世界に先駆けて固体高分子型燃料電池(PEFC:Polymer Electrolyte Fuel Cell)型「エネファーム」の一般発売が開始された。
また、2011年10月には、固体酸化物型燃料電池(SOFC:Solid Oxide Fuel Cell)型「エネファームtype S」が市販された。
エネファームは、2019年3月に発表された「水素・燃料電池戦略ロードマップ」、2021年10月に発表された「第6次エネルギー基本計画」で、さらなる導入拡大を進めることが言及されているが、政府は業務・産業用燃料電池も加えて、引き続き導入支援を行うとしている。

そのため、新エネルギー・産業技術総合開発機構(NEDO)は、水素社会の実現に向けた技術開発の方向性を明らかにし、産学官が長期的視野を共有して技術開発に取り組むために、2005年から「燃料電池・水素技術開発ロードマップ」を公開している。
直近では、2023年2月に「定置用燃料電池」、2024年3月に「FCV・HDV用燃料電池」のロードマップを策定し、現在は「水電解」分野のロードマップ策定のため技術課題を整理している。
家庭用燃料電池の技術開発ロードマップ
2019年3月発表の「水素・燃料電池戦略ロードマップ」と、直近の技術開発ロードマップを比較すると、エネファーム普及台数が大きく下方修正されているが、他は寡少修正に留まる。
すなわち、2030年頃までの普及台数は530万台→300万台に修正された。この目標を実現するため、発電効率は(LHV、40~55%以上→40~60%以上)、耐久性は15年、システム価格は5年で投資回収が可能な50万円台→50万円以下をめざし、大幅な小型化や設置簡素化による集合住宅への普及を進めるとした。
特に、2030年以降には金属支持型SOFCによる耐久性の向上や、プロトン伝導セラミック燃料電池(PCFC)やオフガスリサイクルSOFCによる超高効率化に加え、燃料多様化への対応をめざすとした。

業務・産業用燃料電池の技術開発ロードマップ
2017 年以降に、PEFC(数kW~100kW級)、SOFC(数kW級、数10kW級、250kW級)の業務・産業用燃料電池が市場導入されたが、ガスエンジンなどに比べて初期導入コストと運用メリットでの優位性が低く、普及拡大には継続的な低コスト化が不可欠との共通認識が広がった。
ロードマップには、2030年頃からの分散型電源としての自律的な普及拡大をめざし、高効率・高速生産を実現する革新的生産技術による低コスト化と、燃料多様化を進めると記された。
加えて、発電を主としながら、余剰電力で水素製造する「可逆的固体酸化物形燃料電池(rSOC)システム」(リバーシブルSOCシステム)の実用化、 SOFCの排ガスや燃料改質の際に発生するCO2を回収する「CO2分離回収型燃料電池」の実用化をめざすと記された。
一方、新たに2030年以降の普及拡大をめざす中容量ハイブリッドシステム(数100kW~数MW級)、2040年以降の普及拡大をめざす大容量コンバインドシステム(数10MW以上)が、2016年6月策定の経済産業省「次世代火力発電に係る技術ロードマップ」に基づいて記載された。
2030年の性能目標は、中容量ハイブリッドシステムで発電効率60%以上、耐久年数:15年、システム価格:30万円/kW以下とし、大容量のガスタービン燃料電池複合発電(GTFC、発電効率:63%)と石炭ガス化燃料電池複合発電(IGFC、55%)は共に耐久年数:15年、システム単価は量産後従来機並みと設定された。

家庭用燃料電池「エネファーム」の市販状況(2009年~現在)
エネファームの商品化動向
家庭用燃料電池システムは、国内統一ブランド「エネファーム」として商品化が進められた。ただし、「エネファーム」は、東京ガス、大阪ガス、ENEOSの登録商標である。当初、燃料電池スタックとして固体高分子型燃料電池(PEFC)型が市販されたが、その後、固体酸化物型燃料電池(SOFC)型が市販された。
いずれも、都市ガスやLPガスを燃料改質装置を通し、得られた水素を燃料電池スタックで空気中の酸素と反応させ、電気化学的に直流電気を得る仕組みである。排熱は熱回収装置で水を温めて貯湯タンクに蓄えて、温水供給を行うコージェネレーションシステムである。
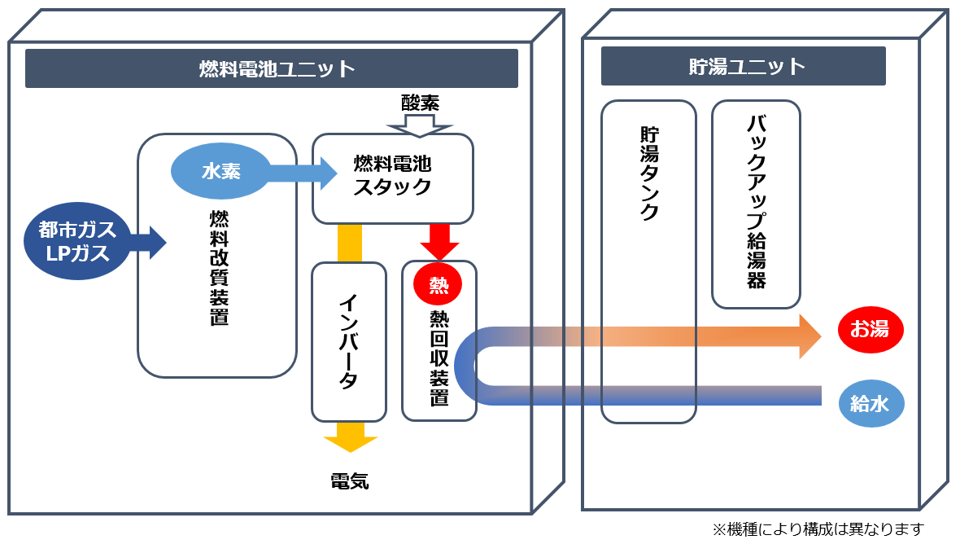
2009年5月、東京ガス、大阪ガス、東邦ガス、西部ガス、新日本石油(現ENEOS)、アストモスエネルギーの6社が、PEFC型「エネファーム」の販売を開始した。PEFCメーカーは、パナソニック、荏原バラード、東芝燃料電池システム、ENEOSセルテックであったが、同5月に荏原製作所が撤退を表明した。
2011年10月、ENEOSセルテックが、SOFC型「エネファームtype S」の販売を発表。しかし、2012年9月には、ENEOSセルテックはPEFC型の製造を中止し、SOFC型の製造に絞り込むと発表。
2012年4月、大阪ガスはアイシン精機、京セラ、長府製作所、トヨタ自動車と共同開発したSOFC型「エネファームtype S」の販売を開始した。京セラがセルスタック、アイシン精機がセルスタックを組み込んだ発電ユニット、排熱利用給湯暖房ユニットを長府製作所が製造した。
2014年10月、2009年にPEFC型、2011年にSOFC型を発売したENEOSが、部品トラブルなどによる販売不振のためエネファームの事業体制を見直し、2015年3月で自社による開発・生産を終了し、他社品の仕入販売に移行すると発表した。
2017年6月、営業赤字に陥った東芝燃料電池システムが、PEFC型「エネファーム」の製造から撤退を表明。
2019年10月、東京ガスは、体積を約60%削減したSOFC型「エネファームミニ」の販売を開始した。京セラは、ダイニチ工業、パーパスと燃料電池ユニット(貯湯タンク内蔵)を共同開発し、東京ガスはこれにパーパス製熱源機を組み合わせて販売する。設置スペースの小さい戸建て住宅やマンション向けを想定した。
複数の企業の撤退により、現在、エネファームを提供するメーカーは、パナソニック(PEFC)、京セラ(SOFC)、京セラがセルスタックを供給するアイシン精機(SOFC)の3社に絞られている。2021年4月にパナソニックは20万台、2020年7月にアイシン精機は10万台の累積販売台数を公表した。
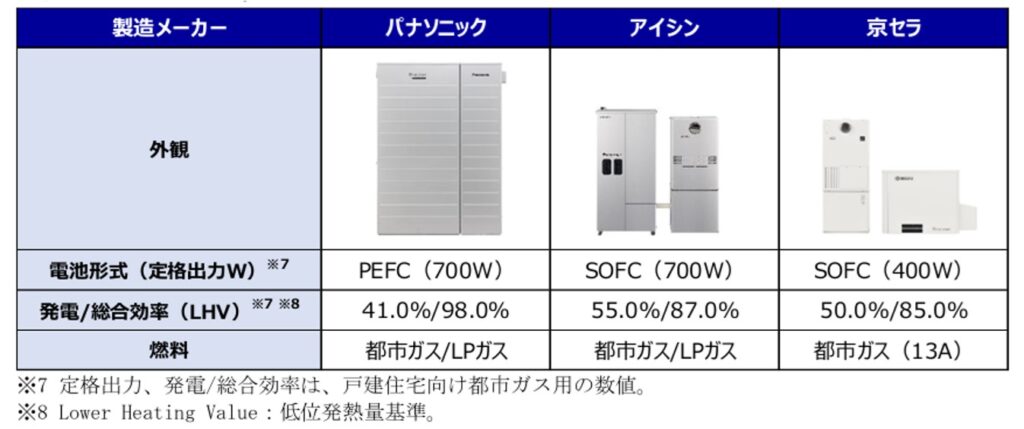
その後も「エネファーム」は継続的な発電効率向上と低価格化、メンテナンスコスト低減が進められる。また、寒冷地対応、停電時発電継続機能、自立起動機能、非常時のタンク水利用の簡便化、外出先からのスマートフォンアプリによる操作など通信機能・IoT化など顧客ニーズ対応も進められた。
一方、「エネファーム」数千台を遠隔制御し、系統電力に対する調整力の供出や系統需給状況に応じた制御の確立に向けたVPP実証への参画など、技術革新も進められている。
ところで、2014年4月、パナソニックはEU向け家庭用燃料電池コジェネシステムを、ドイツのフィスマン・グループと共同で開発し、一部地域で実験的に販売を始めた。また、アイシン精機はドイツのボッシュと共同でEUでの家庭用燃料電池システムの実証試験に参加し、海外市場の開拓をめざすが必ずしも順調ではない。
欧米での燃料電池車は、トラック・バスなどの商用車が先行し、乗用車はこれからである。同様に、欧米では定置用燃料電池も産業用は先行しているが、家庭用燃料電池はこれからであろう。欧米と日本との燃料電池の普及戦略が、大きく異なったことに注目する必要がある。
一方で、国内の定置用燃料電池メーカーの海外展開は順調には進んでいない。心配されるのは、国内市場のみを見ていると、日本特有のガラパゴス化が始まることである。
エネファームの普及状況
2024 年1月、エネファーム普及推進協議体「エネファームパートナーズ」は、「エネファーム」の累計販売台数が50万台を突破したと発表。発売から15年を経て、累積販売台数が50万台を突破したことはめでたいことである。しかし、国内の一般世帯総数は4885万世帯(2020年度)であり、普及率は1%に留まる。
政府が第5次エネルギー基本計画で、エネファーム導入目標を、2020年で累積140万台、2030年で累積530万台としたのは、単なる目安ということなのか?
2020年で累積50万台にも届かず、2021年10月の第6次エネルギー基本計画で、2030年で累積300万台に目標を下方修正した。なぜ下方修正したのか?
2017年度をピークとして、年間のエネファーム販売台数は徐々に低下傾向にある。今後、仮にエネファームの販売台数4万台/年をキープできても、2030年には累積80万台に達するのがやっとであろう。下方修正した累積300万台の意味は、ますます不明である。
政府は目標を単に下方修正するのではなく、導入目標を達成できなかった理由を明確にし、対策を施す必要がある。この反省なくしては、次のステップは期待できない。
エネファームの耐用年数は10年~20年とされており、10年前後から高額なメンテナンス費用が必要となり、20年で撤去する必要がある。今後、販売台数4万台/年をキープできるかは疑問である。
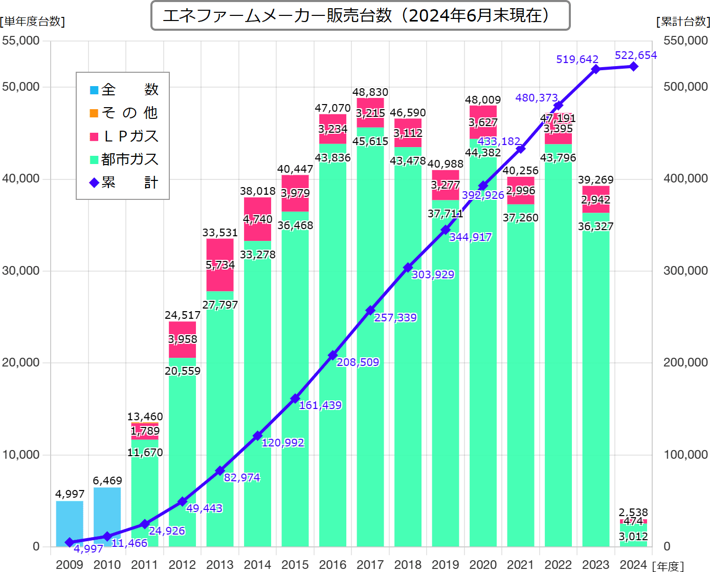
資源エネルギー庁によればエネファームの販売価格は、販売が始まった2009年は300万円超/台であったが、2020年には、ものにより100万円/台を切る水準まで低下しており、エネファーム本体の大きさが年々小型化するなど、設置性なども向上していると胸を張っている。
しかし、2019年にはSOFC型「エネファームミニ」が、設置スペースの小さい戸建て住宅やマンション向けに発売されたが、エネファームの導入台数に大きな影響は与えなかった。
エネファームの販売台数が伸びない理由は、未だに高い「初期費用」と「メンテナス費用」である。一般に、エネファームは初期費用+工事費+オプションを付けると、150~200万円/台と高価である。耐用年数10年が経過すると有料となるメンテナンス費用も無視できない。
一方、給湯に関して、エコキュートは初期費用+工事費で30~50万円程度、メンテナンスの必要はなく、耐用年数10年で全交換しても、エネファームの初期費用の半分で済む。

業務・産業用燃料電池の開発経緯(2000年頃~現在)
世界的な業務・産業用燃料電池メーカーは、2000年頃から販売を継続している富士電機(PAFC)、米国ブルームエナジー(SOFC)、米国フューエルセル・エネルギー(MCFC)があげられる。
一方、国内では、GTーSOFCハイブリッド機を商品化した三菱重工業や、FCEVで先行した自動車メーカー、エネファームメーカーが業務・産業用燃料電池市場への参入を進めている。
富士電機のリン酸型燃料電池(PAFC)
富士電機は、1998年にリン酸型燃料電池(PAFC:Phosphoric acid fuel cell)「FP-100E」を商品化し、国内で唯一、リン酸型常圧水冷式燃料電池の販売を継続している。2018年4月現在で、日本を中心に、韓国、ドイツ、米国、南アフリカに計86台と豊富な納入実績を有している。
現在は、都市ガス型の「FP-100i」(作動温度:200℃、出力:105kW、発電効率:42%、総合効率:91%)と、バイオガスの下水消化ガス(メタン:60%、CO2:40%)型の「FP-100iB」を商品化。また、柔軟な容量拡張性のあるPEFC型水素燃料電池システム(出力:50~480kW、発電効率:40~50%)の受注を始めている。
また、2014年からNEDOプロジェクトに参画してSOFCの要素技術開発を進め、2017年から千葉工場で3000h以上の実証評価を行っている。2018年10月に都市ガス型の業務用SOFC(出力:50kW、発電効率:55%)の販売も報道されたが、商品化には至っていない。

縦5.5m×横2.2m×高さ3.4m、重さ:14トン
米国ブルームエナジーの固体酸化物型燃料電池(SOFC)
2001年設立の米国カリフォルニア州ベンチャー企業のBloom energy(ブルームエナジー)は、SOFC型「ブルームエナジーサーバー」(出力:200kW、発電効率:53%)の開発・製造・販売を進めている。2008年7月にGoogle本社に400kW機、2010年9月にAdobe本社に1200kW機など、30台の納入実績を有する。
都市ガス・バイオガス型で、寸法は幅8m×奥行2.6m×高さ2.1m。米国では分散型電源としてデータセンター、工場、大規模商業施設、官公庁など、持続的な電力供給を必要とする施設で導入されている。
2013年7月、ソフトバンクとブルームエナジーは、ブルームエナジージャパンを設立し、産業用SOFC「ES-5700ブルームエナジーサーバー」の輸入販売を発表。セルスタックは、潮州三環集団製を採用している。
顧客敷地内にサーバーを設置し、発電した電力を販売する仕組みで、顧客は初期投資や発電に使うガス代などは支払わずに電気料金のみを支払う。料金は系統電力と同等か少し下回る程度に設定し、標準で20年程度の長期契約を結び、契約期間中は電気料金を変更しない。
2013年11月、都市ガス型の国内初号機を、福岡市内のソフトバンク「M-TOWER」に設置して運転を開始。その後、2014年6月に慶応義塾大学湘南藤沢キャンパスと東京汐留ビルディングに200kW機を設置するなど、これまで計8台を可動。最大容量は、2019年4月の韓国ブンダン複合火力発電所の8350kW機である。

「Bloomエナジーサーバー」、約9.1m×2.1m×2.6m / 19.9トン
顧客敷地内にサーバーを設置し、発電した電力を販売するブルームエナジーの戦略は、顧客に初期投資やメンテナンス費用を負担させない新方式である。さらなる定置用燃料電池の普及拡大のためには、顧客にメリットのある新しい仕組み作りが必要であることは間違いない。
米国フューエルセル・エネルギーの溶融炭酸塩型燃料電池(MCFC)
米国コネチカット州ダンベリーのFuelCell Energy(フューエルセル・エネルギー)は、1970年頃に600℃レベルの高温で作動する溶融炭酸塩型燃料電池(MCFC:Molten Carbonate Fuel Cell)を開発・商品化し、発電設備(出力:300、1400、2800kW、発電効率:47%)を、米国内だけでなく欧州や韓国でも稼働させている。
また、SOFC(出力:250kW、発電効率:天然ガス62%、バイオガス58%)も商品化しており、コミュニティー向けの中規模発電設備として商品化している。

溶融炭酸塩を電解質に使うMCFCは、燃料電池が水素で発電する際の酸素として火力発電所からの排ガスを供給すると、電解質がCO2を吸収して排出される水蒸気中のCO2濃度が高くなる。そこで、MCFCを使った火力発電所からのCO2回収・貯留技術の商品化も進めている。
2012年3月、韓国の鉄鋼会社Posco(ポスコ)に新エネルギー発電プラント向け製品を供給するほか、MCFCのライセンス生産の提携強化で合意した。子会社のポスコエナジーは、韓国内に生産能力が最大14万kW/年となるMCFC製造工場を設立している。
2020年9月、固体酸化物型電解セル(SOEC:Solid Oxide Electrolysis Cell)の商品化に向けた開発に、米国エネルギー省から300万ドルの補助金を受け、SOEC(水素生産能力:600kg/日、変換効率:HHV90%)の商品化を進めている。
2024年5月、北米トヨタ(Toyota Motor North America, Inc. )と、カリフォルニア州ロングビーチ港の完成車の物流拠点(トヨタロジスティクスサービス)で、バイオマスからグリーン水素・電気・水を生み出す世界最大級の燃料電池施設「Tri-Gen(トライジェン)」を開設した。
「Tri-Gen」は、水素製造施設(製造能力:1.2トン/日)、MCFC発電所(出力:2300kW)、水素ステーションが併設され、畜産場の家畜排泄物や余剰食品等の廃棄物系バイオマスから水素を取り出し、FCEV「ミライ」やゼロエミッショントラックに供給している。さらに、最大1400ガロン/日の水供給も行う。

三菱重工業の加圧型SOFCーMGTハイブリッドシステム
三菱重工業は、円筒型セルスタックの加圧型SOFC(作動温度:700~1000℃)で、都市ガスを改質して水素と一酸化炭素を作り、SOFCで使いきれない都市ガスを、トヨタ・タービンアンドシステム製マイクロガスタービン(MGT)で燃焼させる加圧型複合発電システム(ハイブリッドシステム)を開発した。
2013年9月、SOFC-MGTハイブリッドシステム「MEGAMIE」(出力:250kW、発電効率:55%)の実証試験により、4000h超の長時間連続運転を達成。その結果を受け2015~2017年にNEDOプロジェクトにより、国内4地点で改良型ハイブリッドシステムの実証試験が繰り返され、2017年8月に商品化した。
2019年2月、商用初号機「MEGAMIE」(作動温度:900℃、出力:220kW、発電効率:55%)が、三菱地所東京丸の内ビルディングで稼働した。安藤・間技術研究所(水素利活用)、アサヒビール茨城工場(バイオガス利活用)、2021年にドイツのガス・熱研究所(Gas-und Wärme-Institut Essen)に納入。
また、2020年1月、日本特殊陶業と円筒セルスタックの製造販売の共同出資会社Cecylls(セシルス)を設立してSOFC事業を進めているが、赤字を継続している。
一方、NEDOプロジェクトにより、MGTを適用したMW 級システムの開発を進めており、さらにMGTに代わりターボチャージャーを空気供給源とした「改良型MEGAMIE」の開発も推進している。

出典:三菱重工業
自動車メーカーによる産業用燃料電池の開発
2016年1月、本田技研工業が英国Ceres power(セレスパワー)と家庭用SOFCの共同研究を始めた。セレスパワーのSOFCスタックは、酸化セリウム系電解質(CGO)セルを採用したフェライト系ステンレス鋼基材の金属支持型セルで、作動温度:550~600℃、発電効率:50%以上である。
同年6月、セレスパワーは、EVの航続距離拡大のための車載用SOFCスタック開発を目的とした英国日産自動車、インクジェット印刷技術の英国M-Solvとのコンソーシアムを発表した。バイオ燃料のような代替燃料を使用し、世界的な自動車排ガス規制をクリアする狙いである。
同年9月、セレスパワーは米国カミンズと5kW-SOFCモジュラーシステムの開発計画を発表。高い発電効率と最大出力:100kWまでの複合分散型電源利用を想定し、データセンター市場のほか商用熱電併給など幅広い適用を想定する。作動温度を下げれば、周辺機器の耐高温性も不要で、低コスト化が実現できる。
2019年9月、トヨタ自動車は定置型燃料電池(定格出力:100kW)を開発し、愛知県豊田市の本社工場敷地内に設置して実証運転を開始した。FCEV「ミライ」用のFCスタックや蓄電池など2セットで構成され、2020年12月まで実証試験を進めて商品化をめざす。
2020年12月、ドイツのBosch(ボッシュ)は英国セレスパワーとの連携強化に合意し、2024年の産業用SOFCの本格生産(出力規模で約20万kW/年)に向けた計画を発表した。2023年7月、シュトゥットガルトのフォイヤバッハ工場で、燃料電池パワーモジュールの量産を開始した。パイロット顧客は米国ニコラ・モーターズである。
2024年3月、日産自動車は、栃木工場でのバイネックスと共同開発したバイオエタノール燃料の定置型SOFC(出力:3k W)の試験運用を発表。2027年までに耐久性に優れた金属支持型セルで出力:5kW、2029年に出力:20kW、その後も段階的に出力を高めて工場電源として利用する。
また、日産自動車は、オーストラリアでソルガム(別名:タカキビ)の栽培からバイオエタノール製造まで、バイオマス発電の電力を使う計画で、将来的にはバイオエタノールからメタネーション技術により樹脂を合成し、自動車部品として使うことを想定している。

「エネファーム」メーカーによる産業用燃料電池の開発
2021年10月、パナソニックは高純度の水素で発電する純水素型PEFC「H2 KIBOU」の発売を開始した。セルスタックを「エネファーム」と共用化し、業務用途をターゲットに単相3線式のPH1(出力:5kW、発電効率:56%)で、複数台を連結制御することでMWクラスへの出力アップに対応する。
2023年6月、三相3線式あるいはDCに対応した「PH1+(三相線タイプ)」を最大出力を高めて、2024年12月に三相3線式の「PH3」(出力:4~9.9kW、発電効率:56%)を発売する。システム全体の構成を見直して初期コストを低減し、総点検停止までの期間を15年に拡大してライフサイクルコスト(kWh単価)を低減する。

2024年3月、アイシンは家庭用燃料電池「エネファーム」で培った技術を生かし、高効率な産業用純水素SOFCや固体酸化物型電解セル(SOEC)の実用化を加速している。水素還流技術を採用するなどして発電効率を高め、SOFCは2024年度中に自社工場や事業所での実証を開始する。
政府の示す「水素基本戦略」では、業務・産業用燃料電池の発電効率を現状の40~55%から2030年には60%への引き上げをめざしており、アイシンも「純水素型SOFC」で60%を目標とする。また、アルミニウム溶解炉の排ガスからCO2を分離・回収し、水素と反応させる「SOECメタネーション」の開発も進める。
その他、産業用燃料電池関連の動向
2014年7月、米国GEが産業用SOFC市場への参入を表明した。天然ガス型で出力:1000kW~1万kW、発電効率:65%、総合効率:95%。フェライト系ステンレス鋼支持基板上にアノード(Ni-YSZ)と緻密質電解質(YSZ)の形成に溶射技術を適用し、カソード(LSCF)はスクリーンプリント焼結した金属支持型である。
大学で金属支持型SOFCセル(出力:50kW)の実証試験で4万時間以上を達成し、ニューヨーク州北部に製造プラントを建設した。2014年にスタックデザインを完成し、2016年計画のFC-ガスエンジン・ハイブリットシステム(出力:1000kW)のプロトタイプ作製は中止し、SOFC単体(出力:1000kW)プラグラムへの変更を発表した。
しかし、その後のGEの動向は不明である。
一方、豊田通商は、2016年8月にカナダのバラードと純水素型燃料電池(出力:1.7/5kW、温度:70~90℃、効率:30~35%)、2020年11月にドイツのSFCと直接メタノール(90%)型燃料電池(出力:40~500W、温度:70~90℃、効率:<30%)などと販売契約を結び、小型燃料電池のラインナップを進めている。
これらのメタノール改質型燃料電池は、主にモビリティ向け、携帯基地局のバックアップ電源、 洋上風力発電用の風況観測機器用電源として活用されている。
2025年3月、森村SOFCテクノロジーは、固体酸化物形燃料電池(SOFC)を活用した発電システムを開発した。小型で集合住宅などに設置できる第1号機(出力:600W)を、日本特殊陶業の小牧工場の施設内に設置し、実証実験を始めた。2027年度中の商品化を目指す。48kgと軽量で、家屋の壁面に設置できる。
排熱利用をしないモノジェネレーションに特化したことで大幅な小型・軽量化を実現した。業界トップクラスの発電効率:65%を実現。水素混合での実証運転を開始しており、2027年度の商品化をめざす。
国家プロジェクトによるSOFCの開発
2010年代入り、国内の定置型燃料電池の開発は、家庭用「エネファーム」から業務・産業用燃料電池へと移行する。すなわち、マンションや工場向けが商品化されると共に、分散電源として燃料電池発電所の設置が始まり、スマートグリッドの中心的な構成要素として期待されている。
NEDOプロジェクト「SOFC実用化推進技術開発」
2013~2017年、NEDOプロジェクト「SOFC実用化推進技術開発」が推進され、2015年から業務・産業用燃料電池の平板積層型SOFCが、デンソー(出力:5kW)、京セラ(2.8kW)、日立造船(20kW)、三浦工業(4.2kW)、ブラザー工業(4.4kW)から市販された。
2017年6月、セル製造メーカーであった京セラが、エネファームtype S向け700Wセルスタックを4個搭載した業務用SOFC(出力:約3kW、発電効率:52%、総合効率:90%)を商品化し、同年7月から東京ガスや大阪ガスなどの供給エリアで発売を開始した。
2018年2月、ブラザー工業は純水素燃料用PEFC「BFC4-5000-DC380V」(出力:4.4kW)の販売を開始。72時間連続運転が可能な発電安定性を有し、非常用電源などのBCP対策(事業継続対策)に有用である。
「気液分離+水素循環システム」により、セルスタックから水と共に排出される水素オフガスを回収してセルスタックに再供給する。そのため同サイズの燃料電池と比較して2倍の電流量が得られ、長期運転による電圧降下が少なく、急な電力需要の増減に対応する高い負荷追従性を実現している。
2019年8月、日本特殊陶業が主体で日本ガイシ、TOTO、ノリタケカンパニーリミテドと平板積層型SOFCの研究開発の共同出資会社「森村SOFCテクノロジー」を設立し、2021年4月、業務・産業用SOFCセルスタックの本格量産を始め、日立造船などに供給を進め、2025年から家庭用SOFCセルスタックの供給も開始する。
2021年5月、日立造船は中小工場や介護施設向けのSOFC市場(出力:20kW以上、発電効率:52%超)へ参入を公表。平板積層型SOFCスタックは、森村SOFCテクノロジーから供給を受ける。
2017年7月、大阪府バッテリー戦略研究センターと協力してORIST和泉センターに設置して、4000h以上の連続運転、2018年3月、大阪市建設局管理施設の「咲くやこの花館」設備棟前などで実証実験を進めてきた。

2023年5月、デンソーは愛知県西尾市の西尾製作所で、太陽光発電(出力:60kW)と蓄電池(出力:70kW、容量:73kWh)、EV搭載の蓄電池、同社が開発した都市ガス型SOFC(4.5kW、発電効率:65%)を組み合わせ、効率的なエネルギー管理を行う実証実験を開始した。得られた成果はデンソー福島に導入する。
2024年3月、東京ガスと三浦工業は、共同開発したSOFCシステム「FC-6M」(出力:5.8kW、発電効率:63%)の商品化に合意。2020年4月から進めてきた実証試験で耐久性や信頼性の検証を終え、2024年10月より三浦工業から販売を開始する。森村SOFCテクノロジー製のセルスタックを使用する。
排熱利用なしでも省エネルギーやCO2排出量削減に貢献可能なモノジェネレーションシステムで、今後、バイオガス、水素、合成メタン(e-メタン)への対応検討も進める。
内閣府「戦略的イノベーション創造プログラム」での燃料電池開発
2014~2018年、内閣府「戦略的イノベーション創造プログラム(SIP)」のエネルギーキャリアで、京都大学、ノリタケカンパニーリミテド、IHI、日本触媒、豊田自動織機、三井化学、トクヤマがアンモニアを直接燃料として使用するSOFCスタック(出力:1kW級)の開発に成功した。
アンモニア(NH3)を気体で供給し、700~900℃に加熱した電極に触れると窒素と水素に分解し、空気中の酸素と水素が反応して発電する。発電効率は50%を超え、1000hの連続運転に成功。
2018年5月、IHIはアンモニアを燃料として直接供給するSOFCシステム(出力:1kW級)で発電に成功した。改質機を使わない点が特長で、今後、大型SOFCシステム(出力:数10~数100kW)を開発し、業務・産業用として2020年代前半の市場投入をめざす。
2023年11月、アイシンと東北大学は、NEDOプログラムでアンモニア型SOFCの高効率発電に関する研究開発を進め、現在開発中の純水素SOFCシステムの技術を活用しながら、同程度の高効率発電をめざして開発を進め、2027年度に自社工場・事業所で実証実験開始することを発表した。
エネファームの販売台数が伸びない理由は、高い「初期費用」と「メンテナス費用」である。この対策が十分に行われないまま、新たな国家プロジェクトとして業務・産業用燃料電池の開発を進めた。その結果、国内の業務・産業用燃料電池メーカーは乱立の状況にある。
欧米では家庭用燃料電池よりも業務・産業用燃料電池が先行しているが、世界的に稼働している業務・産業用燃料電池は多くはない。果たして、何社が生き残るのであろうか?
再生可能エネルギー由来のグリーン水素
再生可能エネルギーの電力から水電解で水素を製造する方法は、製造段階からCO2を発生せず、得られた水素は長期間の貯蔵・輸送が可能で、風力発電や太陽光発電の出力変動対策となり、発電所の設置場所が需要地と離れている場合の送変電問題を解決するための有効な手段となる。
そのため、2013年から経済産業省により「低コスト・高効率でCO2フリーの再生可能エネルギー水素の製造技術開発」が推進された。
グリーン水素とは?
非化石資源由来の水素製造方法として、再生可能エネルギーで得られた電力を用いて水電解法による製造方法が知られている。得られた水素は「再生可能エネルギー水素」、あるいは「グリーン水素」とも呼ばれ、将来の水素社会を支える水素源として本命視されている。
現在、水電解法で多くの実績を有するのは、旭化成などにより大型装置が商用化されているアルカリ水電解(変換効率:70~90%)である。また、PEFCの逆反応を利用したコンパクトで高い変換効率(~90%)の固体高分子型水電解(PEEC:Polymer Electrolyte Electrolysis Cell)が商品化されている。
いずれも再生可能エネルギーの大きな電力変動下でも、安定して高効率で水電解が行える装置開発と、PEECでは装置の大型化開発が進められている。
また、SOFCの逆反応を利用した固体酸化物型水蒸気電解(SOEC: Solid Oxide Electrolysis Cell)は、作動温度が高いため熱利用が鍵となるが変換効率は極めて高く、アニオン交換膜(AEM:Anion Exchange Membrane)を使うAEM形水電解は、触媒に貴金属を使わないため、共に研究開発が進められている。
国際エネルギー機関(IEA)によれば、水素の世界需要は運輸や発電分野で増え、2050年に約3億トンと2019年の4倍に拡大する見通しである。現状は天然ガスやナフサ由来であるが、IEAは2050年には半分近くが再生可能エネルギー由来(グリーン水素)で製造されると予想している。
政府は2050年に水素製造装置の世界市場が4.4兆円に拡大すると予測している。一方、グリーン水素の大規模生産は、再生可能エネルギー価格の安い欧州、中東、オーストラリア、チリなどが有利で、国内では再生可能エネルギー価格が依然として高く、グリーン水素の自給自足は難しいと見て輸入に頼ろうとしている。
一方、2023年2月、欧州連合は「グリーン・ディール産業計画」で、2030年までに最低1億kW分の水電解装置を導入し、1000万トン/年のグリーン水素製造の域内生産を目標に掲げている。また、域外から年間1000万トン/年のグリーン水素輸入もめざしている。
燃料電池を使った水素製造装置の開発動向
1993年に神鋼環境ソリューションは、固体高分子電解質膜を利用した純水を直接電気分解する「HHOG」を商品化し、水素ステーションなど国内外で200基(2022年3月末)を超える納入実績を有する。水素製造能力:1~100Nm3/h、水素ガス供給圧力:0.82MPaGをラインアップしている。
2015年5月、日立造船は、再生可能エネルギー利用による水素ステーション向けの固体高分子型水素製造システム「ハイドロスプリング」(製造能力:1Nm3/h、圧力:0.8MPaG)を九州大学内の水素スタンドに納入。
2018年6月、ハイドロスプリング(製造能力:1~200Nm3/h)を発表した。風力や太陽光発電などの再生可能エネルギーの急激な電力負荷変動に追従し、システム全体(2.44mW×12.2mD×2.9mH)は40フィートコンテナに収納した可搬式とした。

2022年4月、高砂熱学工業は、石狩厚田グリーンエネルギーを設立し、マイクログリッドの運営を開始した。系統電力と太陽光発電の両方から電力を供給し、太陽光発電の余剰電力は、蓄電池および固体高分子形水電解装置「Hydro Creator」(製造能力:5Nm3/h、圧力:0.9MPaG)でグリーン水素を製造して貯蔵する。
水素電力貯蔵システムの開発
再生可能エネルギー水素は、風力発電や太陽光発電のような大きな出力変動を水素製造・貯蔵で平準化したり、遠隔地の発電所から送電を行い需要地で水素を製造・発電するなどエネルギー輸送対策としても有効である。現在、低コスト化をめざして国内外で実証試験が進められている。
水素電力貯蔵とは?
電力と比べて、水素は大規模かつ長期の貯蔵が可能であり、電力のような送電ロス問題も無視できる。この特性を利用して、電力を水素に置き換えて貯蔵する水素電力貯蔵システム(Hydrogen power storage system)の開発が進められている。海外では幾つかの水素電力貯蔵システムが実用化されている。
■カナダのブリティッシュ・コロンビア州ベラクーラでは、「HARP(Hydrogen Assisted Renewable Power System)」プロジェクトが進められている。年間雨量の変動に起因する水力発電の出力変動を平準化するため、余剰電力による水電解で得た水素をタンク貯蔵し、需要に応じて燃料電池で発電・供給している。
■ドイツのブランデンブルク州プレンツラウでは、風力発電の余剰電力による水電解で得た水素をタンク貯蔵し、需要に応じてバイオガスと混ぜてコージェネレーションプラントに送り、電気と熱に変換して利用している。また、貯蔵された水素の余剰分は燃料電池車(FCEV)用にベルリンに搬送されている。
水素電力貯蔵システムは、水素製造プロセス、水素貯蔵プロセス、水素発電プロセスを組み合わせたシステム(例えば、アルカリ水電解/高圧水素タンク/PEFC)であり、実証段階からより高効率なシステム(例えば、SOFC/高圧水素タンク/SOEC)の研究開発まで、様々な組み合わせの開発が検討されている。

二次電池と水素電力貯蔵について、体積エネルギー密度と質量エネルギー密度の関係を対数グラフで示すが、二次電池ではNaS電池とリチウムイオン電池が高いエネルギー密度を有している。しかし、これらの二次電池に比べて水素貯蔵プロセスは、より多くのエネルギーをコンパクトに貯蔵できることが分かる。
また、水素貯蔵プロセスの種類によってもエネルギー密度に大きな差が生じ、高圧水素タンクに比べて有機ハイドライドと、液体水素が高いエネルギー密度を有していることも分かる。
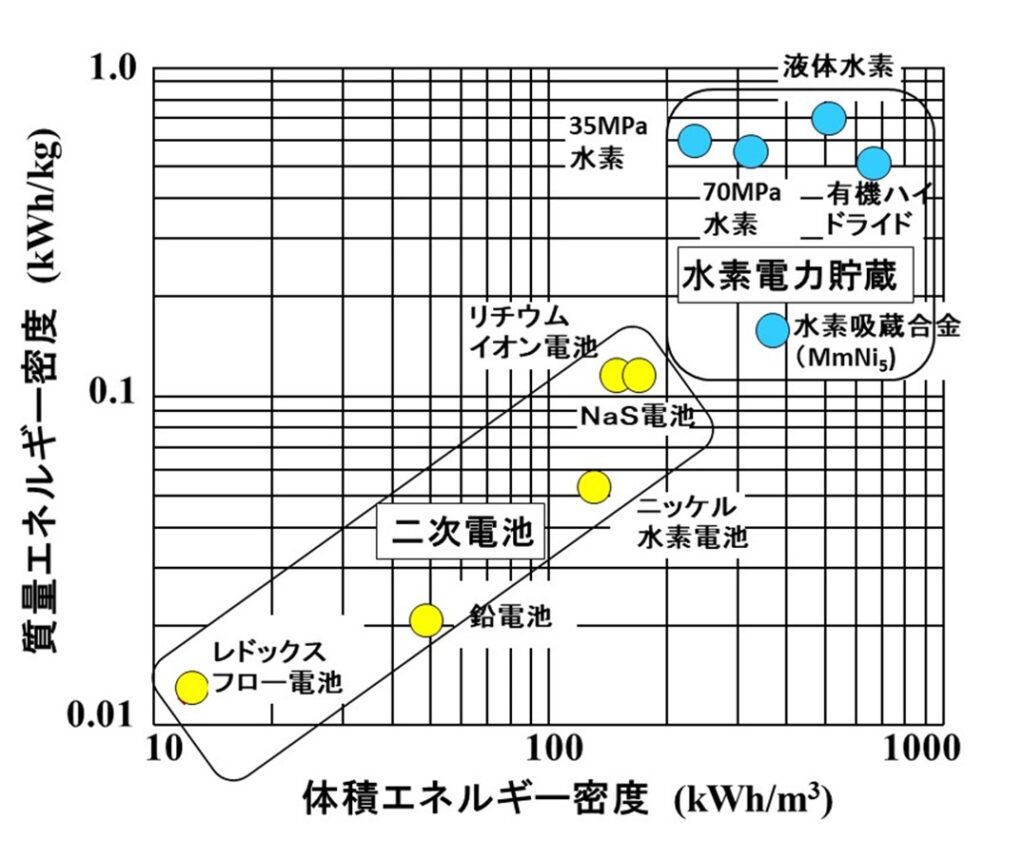
政府は2021年4月から電力需給調整市場の創設を始めており、2024年度から最終段階となる周波数を瞬時に調整する一次調整力の売買を始めると発表した。これにより送配電事業者の要請で電力需給の調整に貢献すると、その事業者から対価を得られる仕組みが完成した。
経済産業省は再生可能エネルギー発電量の出力制御を減らす対策として、①蓄電池の活用、②火力発電所の出力抑制、③送電網の強化などをあげており、水素製造による電力貯蔵は②に該当する。
2022年4月以降、東京電力HDは水素の製造装置を電力の送配電網と連結し、再生可能エネルギーの出力調整を水素製造量の増減で調整することを公表している。
燃料電池を使ったシステムの開発動向
2015年4月、川崎市と東芝は水素電力貯蔵ステム(容量:350kWh)を、川崎市内臨海部の川崎市港湾振興会館(川崎マリエン)および東扇島中公園に設置し、実証試験を開始した。
この自立型エネルギー供給システム「H2One(エイチツーワン)」は、太陽光パネル(出力:30kW)、水電解装置(製造量:1Nm3/h)、水素貯蔵タンク(容量:270m3)、純水素型PEFC(出力:30kW)とリチウムイオン電池で構成され、災害時の非常用電源システムとして商品化された。
2016年3月、水素吸蔵合金を貯蔵タンクとした「H2One」は、長崎県佐世保市のハウステンボス敷地内の「変なホテル」、2016年4月、横浜市港湾局の横浜港流通センター、2017年4月、川崎市のJR東日本武蔵溝ノ口駅と山口県周南市地方卸売市場、2018年3月、楽天生命パーク宮城に設置された。
2018年8月、福井県敦賀市と東芝エネルギーシステムズは、水素サプライチェーン構築の基本協定を締結した。2019年10月、再生可能エネルギーによる水素電力貯蔵システム「H2One」と、毎日FCV8台分の水素を供給できる水素ステーションで構成される「H2Oneマルチステーション」が開設された。

2016年6月、山梨県とパナソニックは、甲府の県施設「ゆめソーラー館やまなし」の屋根の太陽光パネルで発電し、水電解装置により水素を製造して貯蔵し、必要に応じて純水素型燃料電池(出力:700W)で発電する実証試験を開始。2018年6月、新たに開発した純水素燃料電池(5kW×3台)を増設した。
2017年6月、清水建設と産業技術総合研究所は、建物付帯型水素エネルギー利用システム「Hydro Q-BiC」を開発し、福島再生可能エネルギー研究所(FREA)内で実証運転を始めた。
2022年7月、トヨタ系自動車販売会社などのユーグループは、本社ビル「プリズムビル」の改修に合せて、清水建設が開発した水素エネルギー利用システム「Hydro Q-BiC」を導入した。
太陽光発電(出力:20kW)を使い高分子型水電解装置により水素を製造し、水素吸蔵合金タンク(450Nm3、蓄電容量ベース:674kWh)、東芝製純水素型燃料電池(出力:100kW)、リチウムイオン電池を利用して、ビルのピークカットや非常時電源として活用する。
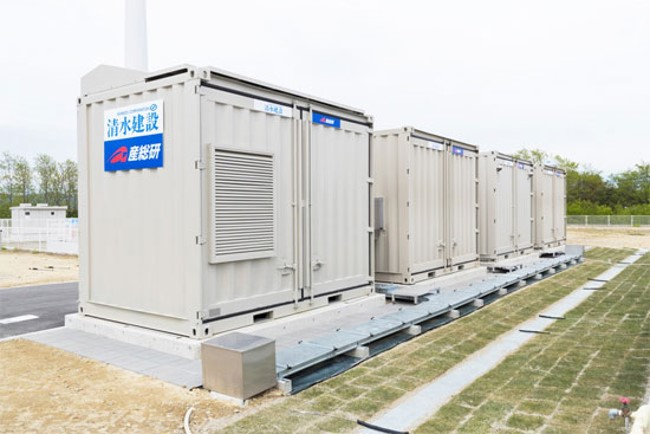
2018年6月、トヨタ自動車とセブン-イレブン・ジャパンは、水素電力貯蔵システムを組み込んだ新しいコンビニ店舗の実現をめざすと発表した。
2019年から太陽光発電システム、水電解装置、水素ステーション、小型トラック、PEFC(出力:10kW)、ハイブリッド車の使用済み蓄電池を再利用した蓄電システムを導入し、非常時に店舗への給電機能付き充電器などを順次設置し、店舗のエネルギー需要に合わせ、これらの機器を統合制御するBEMSを導入する。
2024年4月、日本特殊陶業は水素製造と燃料電池による発電を1台の装置で可能にする「リバーシブルSOCシステム」を開発した。水を電気分解して水素を生成する固体酸化物形電解セル(SOEC)と、水素と酸素から電気を生成する固体酸化物形燃料電池(SOFC)の動作を切り替えられる。2025年度中の製品化をめざす。
SOEC作動温度は700~750℃、AC100V電源で水素製造量は最大0.9Nm3/h、SOFC発電能力は最大740Wである。SOEC/SOFCの切り換えは最大1hを要し、往復変換効率は31%と低い。

メタネーション技術の開発
水素(H2)と二酸化炭素(CO2)を原料とし、触媒(Ni、Ruなど)を用いて熱化学的にメタンを合成する(メタネーション)技術が開発され、実用化されている。
現在、再生可能エネルギーを使いメタンを合成するメタネーション変換効率は55~60%である。最近、再生可能エネルギーを使いSOFCの逆反応であるSOECメタネーションの開発が進められている。水蒸気とCO2を使って電気分解し、高い変換効率85~90%を達成している。
メタネーション技術とは?
1902年、フランスのPaul Sabatier(ポール・サバティエ)は、水素(H2)と二酸化炭素(CO2)を原料とし、高温高圧状態でニッケル(Ni)触媒を用い、熱化学的にメタン(CH4)を合成するメタネーション技術を見出した。アルミナ上にルテニウム(Ru)触媒を担持させた高効率触媒も開発されている。
一方、最近では熱化学法以外に、電気化学法、光還元法、バイオ法などの研究開発も行われている
「2050年カーボンニュートラル」に向け、再生可能なクリーンエネルギーに転換していくグリーントランスフォーメーション(GX)が政府により推進される中で、注目を集めているのが「メタネーション技術」である。
再生可能エネルギー水素を原料として得られる合成メタン(e-メタン)を、都市ガスの代替として使う試みで、既存の都市ガスのインフラがそのまま使える。合成メタンの燃焼時に排出されるCO2は、製造時に原料として回収されたCO2であり、循環使用するためにCO2排出量は実質ゼロになる。
2021年6月、メタネーション技術の確立と社会実装に向けた「メタネーション推進官民協議会」が設立され、官民両面での取り組みが加速する。政府は、2030年までに都市ガス導管に注入するガスの1%をカーボンニュートラルメタンとし、2050年までに90%とする目標を掲げた。残り10%は、水素直接利用、バイオガスなど。
現在、再生可能エネルギーなどの余剰電力で水電解により水素(H2)を製造し、別途に回収貯留したCO2と共にメタネーション装置に入れ、高温で触媒反応させることで合成メタン(CH4)を製造する方法が進められており、実用化に向けて量産化と低コスト化が進められている。
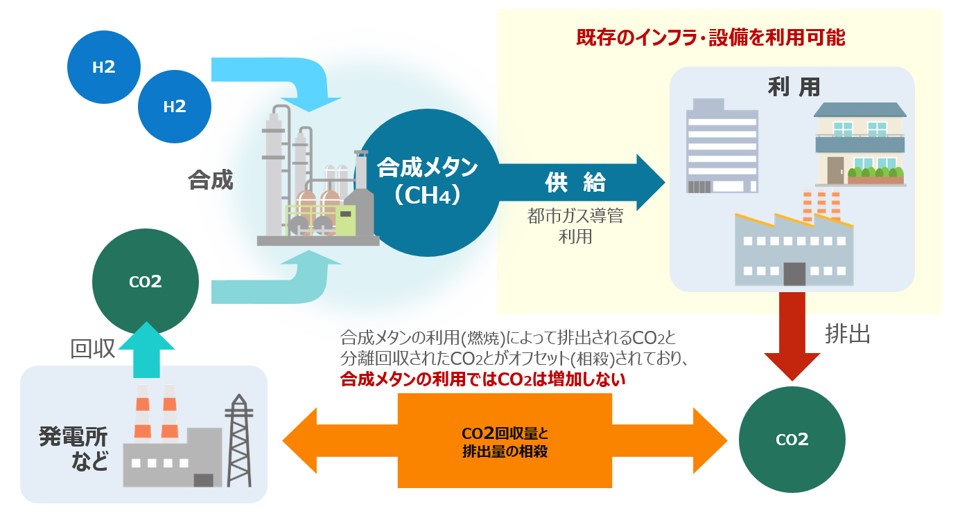
メタネーション装置の開発動向
2019年10月、国際石油開発帝石(現INPEX)と日立造船は、メタネーション試験設備を長岡鉱場の越路原プラント敷地内に完成させた。越路原プラントで天然ガス生産時に付随するCO2と、固体高分子水電解装置(32Nm3/h)により製造された水素から合成メタンを製造する。
日立造船製のプレート型メタネーション反応器は、熱回収効率が87%と高く、運転温度:200℃、運転圧力:0.7MPaであり、生成ガス(メタン濃度:91.2%)をガス精製器を通し、高濃度化(99.6%)が可能である。メタン製造能力は8Nm3/hで、4500h以上の安定製造を確認している。
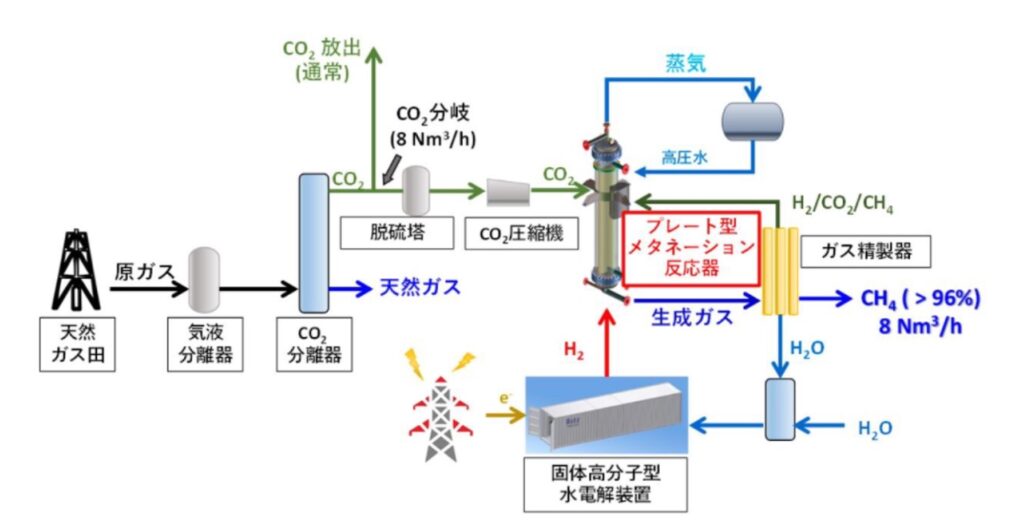
2021年10月、INPEXと大阪ガスは、大規模メタネーション装置(製造能力:約400Nm3/h)の導入のNEDOプロジェクト(~2025年度末)を開始した。INPEX長岡鉱場の越路原プラントからCO2を回収貯留し、メタネーション設備を接続し、製造した合成メタンをINPEXの都市ガスパイプラインへ注入する。
2022年3月、東京ガスは横浜テクノステーションで、メタネーション実証試験を開始。主に太陽光発電の電力で、英国ITM Power製の固体高分子型水電解装置(製造能力:30.9kg/h、圧力:1MPa未満)で水素を製造し、横浜市清掃工場の排ガスから三菱重工業製のCO2分離回収装置で得られたCO2をトレーラーで受け入れる。
日立造船製の多管シェル&チューブ型メタネーション装置(CH4製造能力:12.5Nm3/h)でメタン合成を行う。2020年代中頃に数百Nm3規模に拡大し、2030年にガス販売量の1%に合成メタン導入の目標を掲げている。

2022年6月、日立造船が、小田原市環境事業センターのごみ焼却施設から排出されるCO2を回収貯留し、LPガスの改質水素と反応させるメタネーション実証装置の運転を開始した。排ガスからのCO2分離にはエア・ウォーターの技術を活用しており、合成メタンの製造能力:125N㎥/hである。
2022年8月、日本特殊陶業はメタネーション装置を開発し、2023年4月から小牧工場で実証実験を行うと発表。自社のゼオライト膜でガスエンジン排ガスからCO2を回収貯留し、水電解で得られた水素と反応させて1Nm3/h(0℃、1気圧)の合成メタンを製造し、ガスエンジン燃料として再利用する。
将来的に、4Nm3/hのメタネーション装置を開発し、2030年に中小規模工場への販売を目指す。製造コストは100円台/Nm3と、現状の1/3程度に引き下げ計画である。
2022年9月、豊田自動織機は高浜工場でメタネーション実証実験を始めた。ボイラから排出されるCO2を回収貯留し、化石燃料由来のグレー水素と混ぜて合成メタンを製造し、別ボイラの燃料で再利用する。将来は太陽光発電によるグリーン水素へ切り替え、全工場にメタネーション設備を導入する。
2022年10月、IHIは、合成メタンを製造できる「小型メタネーション装置」の販売を開始。2019年5月からシンガポール科学技術庁化学工学研究所と共同で触媒開発した技術がベースで、シェル&チューブ型反応器で、合成メタン製造量:12.5Nm3/hで、外形寸法は幅2250×長さ6100×高さ2850mmである。
2024年5月、IHIは、東邦ガス知多e-メタン製造実証施設向けに「メタネーション標準機」を納入。東邦ガスでは、5Nm³/hで運転する。2030年には大型装置(数千~数万Nm³/h)の商用化も予定。
2022年、JFEスチールから実証機(500Nm³/h)を受注しており、高炉排ガスからのCO2回収(20トン/日)も含めて2025年の稼働を予定する。吸熱反応のCO2回収と発熱反応のメタネーションを組み合わせ、エネルギー効率を高める。

SOECメタネーションの開発動向
2020年7月、デンソーは、安城製作所のアルミ溶解炉などから出たCO2を回収し、太陽光発電を使って水電解で得た水素を使いSOECメタネーションの実証実験を開始。合成メタンはガス燃料に使い、CO2を工場内で循環させる。2025年度から社外での実証実験を始め、2030年度の事業化をめざす。
2022年4月、大阪ガスは金属支持型SOECで水素を製造し、回収されたCO2から都市ガスを製造するメタネーション試験設備を大阪市酉島地区に建設すると発表した。
2027年度までに200世帯程度、2030年度までに1万世帯分の都市ガス製造を実現し、設備の大型化などで製造コスト削減を進め、2040年頃の事業化を目指す。2023年8月には、石油元売りのENEOSと共同で大阪湾岸での大規模施設の建設に向けた検討に入った。
2022年4月、大阪ガスは大阪市や大阪広域環境施設組合と、再エネ由来の水素と生ごみを発酵させて製造したバイオガス(メタン約60%とCO2約40%)中のCO2でメタネーションを行い、合成メタンを需要家に供給する。環境省「水素サプライチェーン構築・実証事業」(2022年度~25年度)で行う。
2024年6月、 大阪ガスは、舞洲工場のエネルギー技術研究所内にSOECメタネーションのラボスケール試験装置(製造能力:0.1Nm3/h))を設置し、e-メタンの製造を開始した。SOEC電解装置で再エネ電力で水とCO2を電気分解し、生成した水素や一酸化炭素からメタン合成反応装置の触媒反応でe-メタンを合成する。
外部水素の調達が不要で、高温(約700~800℃)の電気分解により、必要な再エネ電力等を低減し、メタン合成時の排熱の有効利用により、従来のメタネーション(約55~60%)を大幅に上回るエネルギー変換効率約85~90%の実現をめざす。
その後、2025~2027年度にベンチスケール試験(e-メタン製造規模:10Nm3/h級、一般家庭約200戸相当)、2028~2030年度にパイロットスケール試験(400Nm3/h級、約1万戸相当)を進め、2030年度にe-メタン製造技術の確立、実証フェーズを経て、2030年代後半から2040年頃の実用化をめざす。
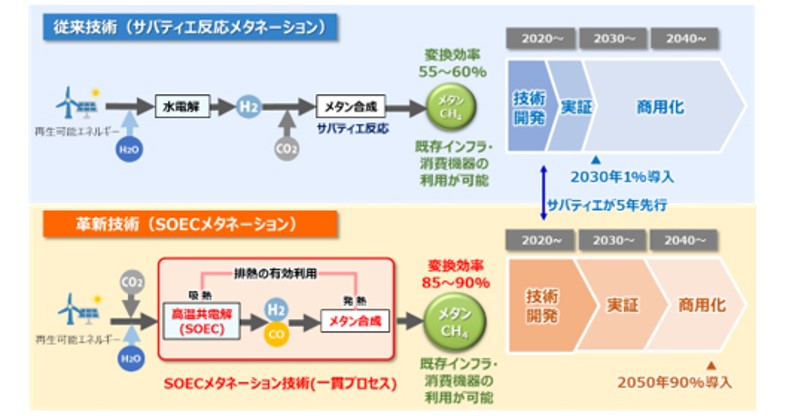